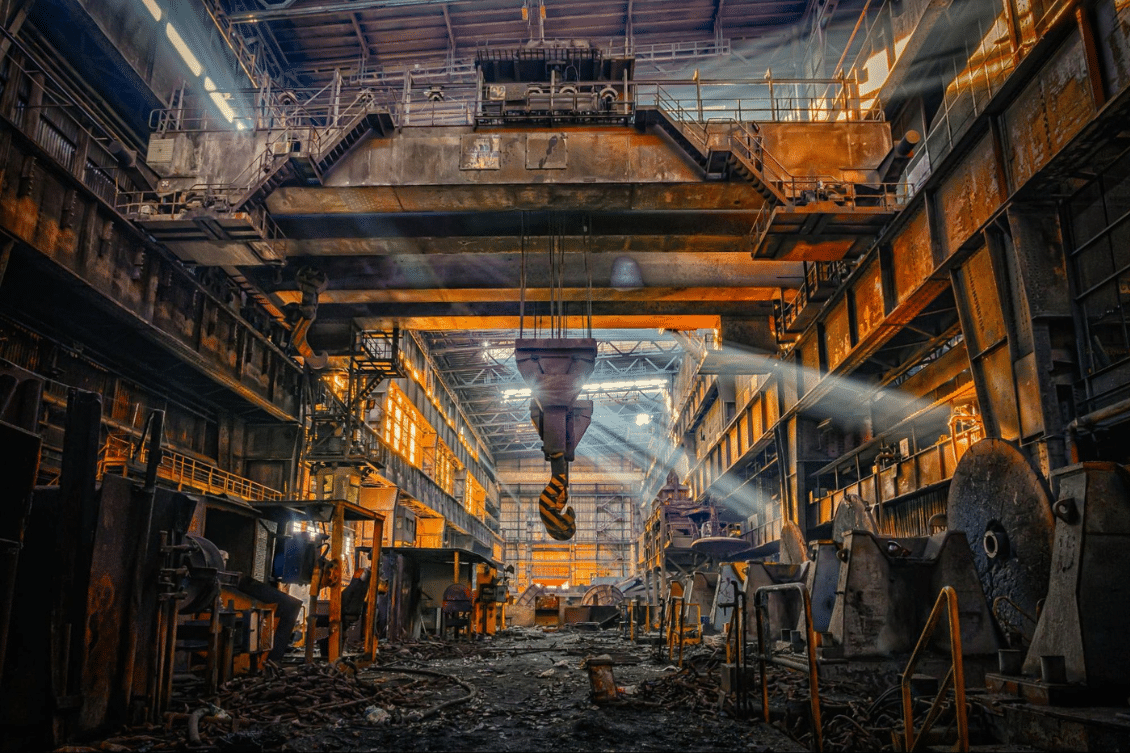
To gain a competitive advantage, companies often look to how they can reduce their production costs by exploring low-cost sourcing options. This approach involves outsourcing parts of the manufacturing process to suppliers who offer significantly lower prices than your current supplier. At first glance, this strategy is compelling; it promises substantial cuts in costs, potentially boosting profit margins in an era where every penny counts.
However, the initial financial appeal of low-cost sourcing is often more complex than it appears. While the upfront costs may indeed be lower, numerous hidden factors can erode these savings over time. These include issues related to quality control, supply chain reliability, compliance risks, and more. Such hidden costs can not only negate the initial savings but also introduce unforeseen challenges that could impact the overall health of a business.
The pursuit of minimizing expenses through low-cost sourcing is a task that requires a deep dive into both the visible and invisible expenses involved. This blog aims to unpack these hidden costs, offering a comprehensive look at why the cheapest option is not always the most cost-effective in the long run. By understanding these complexities, businesses can make more informed decisions that balance cost with risk and quality, ensuring sustainable success in their sourcing strategies.
Quality Control Issues
One of the most significant risks associated with low-cost sourcing is the compromise on quality to maintain lower price points. Suppliers looking to offer attractively low costs often reduce their expenses by using inferior materials, employing less skilled labor, or cutting corners in the manufacturing process. These compromises can lead to defective or substandard products that fail to meet the quality expectations set by both the company and its customers.
For businesses that choose low-cost sourcing, this necessitates a heightened focus on quality assurance measures. Companies often find themselves investing in extensive quality control systems, including more frequent on-site inspections and rigorous testing of products before they hit the market. These additional steps not only increase operational costs but also consume time, potentially offsetting the savings gained from lower production costs.
An example of this comes from the automotive industry, where several major car manufacturers had to recall millions of vehicles due to faulty airbags provided by a low-cost supplier. The airbags, which were prone to explode and project shrapnel, were linked to numerous injuries and deaths, leading to massive financial losses and brand reputation damage.
Another case involved a well-known toy company that outsourced production to a low-cost supplier overseas. The supplier used lead paint, a cheaper alternative that violated safety standards. The result was a global recall that not only cost millions of dollars but also severely damaged the brand’s reputation among parents concerned about product safety.
Supply Chain and Logistic Risks
Opting for low-cost sourcing often means dealing with extended supply chains, which inherently introduces a range of risks and complications. These extended supply chains, frequently spanning multiple countries, can significantly complicate logistics and increase vulnerability to various disruptions.
The lengthier the supply chain, the greater the likelihood of delays and disruptions. Factors such as transportation issues, problems at ports, and delays in customs can all add substantial time to delivery schedules. This not only affects the ability to meet customer demands in a timely manner but also increases the costs related to warehousing and inventory management. Companies may need to keep larger stocks to buffer against delays, tying up capital that could otherwise be used more productively.
Supply chains that stretch across borders are also exposed to geopolitical and economic instabilities. Changes in trade policies, tariffs, and political tensions can lead to sudden increases in costs or compel businesses to find new suppliers abruptly. For example, the imposition of tariffs on goods from certain countries can erase all savings from low-cost sourcing, forcing companies to reassess their supply chain strategies entirely.
Communication and Cultural Barriers
When sourcing from low-cost suppliers, especially those in different countries, businesses often encounter significant communication and cultural barriers. These barriers can lead to misunderstandings, misinterpretations, and errors, all of which can disrupt the smooth flow of operations and impact the quality of the end product.
Language differences are one of the most immediate obstacles. Miscommunications can occur during crucial interactions, such as contract negotiations, quality specifications, and production timelines. Even when both parties speak a common language, such as English, nuances and technical terms can be misunderstood or lost in translation, leading to product discrepancies and operational delays.
Cultural differences in how business is conducted can also lead to complications. Practices that are standard in one country might be unusual or even unacceptable in another. For instance, the approach to deadlines, quality control, and hierarchical decision-making can vary widely between cultures. These differences can result in conflicts or dissatisfaction if not managed properly.
Compliance and Ethical Considerations
In an era where consumers are increasingly aware and concerned about ethical practices, businesses must be vigilant in ensuring that their supply chains uphold environmental and labor standards. However, low-cost sourcing often introduces significant risks in these areas, particularly when partners are located in regions with different regulatory standards or lax enforcement.
Operating across diverse regulatory environments poses a major challenge. Suppliers in low-cost countries may not be subject to stringent environmental protections or labor laws, which can tempt businesses to overlook non-compliance to reduce costs. However, this oversight can lead to serious consequences, including legal liabilities and reputational damage if the practices come to light. Moreover, differences in regulation not only complicate compliance efforts but also require businesses to invest in additional resources to monitor and ensure adherence to acceptable standards consistently.
A prime example of these risks occurred in the apparel industry, where several prominent brands faced public outcry and legal issues after it was discovered that their suppliers were involved in sweatshop practices. The revelations led to boycotts, damaging the brands’ reputations, and forcing them to reevaluate and reconstruct their supply chain practices at considerable expense.
Dependency and Supplier Stability
Relying on a single, low-cost supplier can seem like an efficient way to reduce production costs, but it comes with significant risks. This dependency can lead to critical vulnerabilities within a supply chain, especially if the supplier faces instability issues such as financial difficulties, leadership changes, or production disruptions. Understanding these risks and their potential hidden costs is crucial for businesses aiming to maintain a robust supply chain.
The most immediate risk of dependency is the lack of flexibility it creates. If the sole supplier cannot meet production needs due to capacity issues or economic troubles, the entire production line can stall, leading to inventory shortages and unmet customer demands. This scenario can quickly escalate from a supply chain hiccup to a full-blown business crisis, affecting sales and damaging customer relationships.
An example of supplier instability impacting a business can be seen in the electronics industry, where a major smartphone manufacturer lost significant market share after its sole battery supplier faced a production halt due to a factory fire. The delay in sourcing an alternative supplier and the subsequent production delays led to a missed product launch date, benefiting competitors.
Conclusion
The allure of low-cost sourcing is undeniable for businesses looking to optimize production costs and improve profit margins. However, as explored throughout this blog, this strategy is fraught with hidden risks that can potentially negate initial savings and pose serious threats to business stability and reputation. Issues such as quality control challenges, supply chain and logistic risks, communication barriers, compliance dilemmas, and supplier dependency underscore the complexity of low-cost sourcing.
Businesses must therefore approach low-cost sourcing with a comprehensive understanding of these associated costs and challenges. It is essential to implement robust risk management strategies, such as diversifying supplier bases, strengthening quality assurance protocols, investing in compliance and ethics programs, and building effective communication channels across cultural divides. By doing so, companies can protect themselves from the unpredictable variables that come with low-cost sourcing and establish a more resilient, sustainable, and ethically responsible supply chain.
Interested in OpenBOM? Let us know. We are happy to talk.
By: Jared Haw
Join our newsletter to receive a weekly portion of news, articles, and tips about OpenBOM and our community.