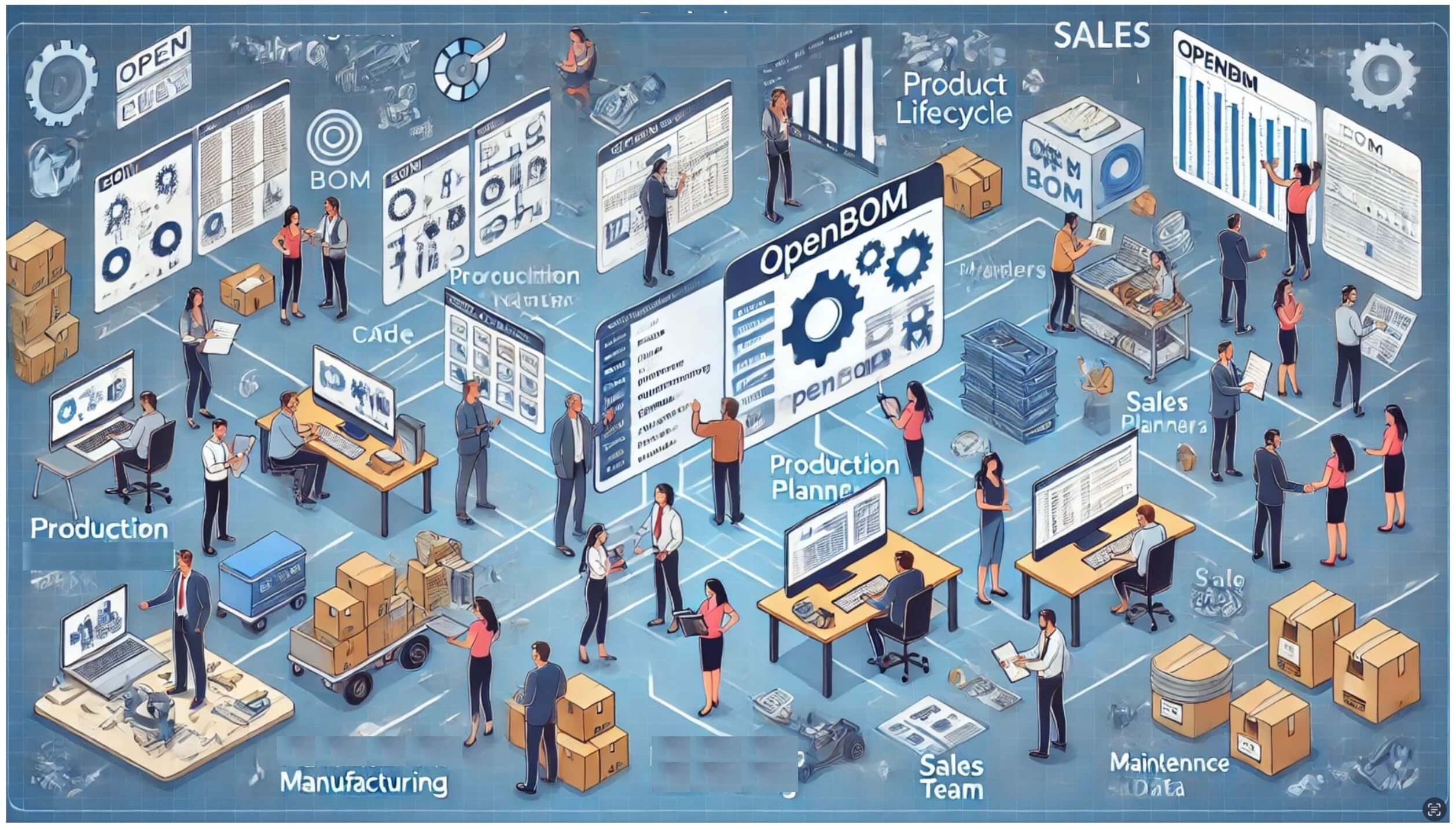
PLM, short for Product Lifecycle Management, refers to the comprehensive process of managing product-related information throughout its entire lifecycle in the engineering and manufacturing industries. There are two aspects of PLM: (1) PLM is a business strategy and (2) PLM is a software.
PLM (Product Lifecycle Management) as a business strategy is an approach that helps to integrate people, processes, technology, and data to optimize the management of a product’s lifecycle across all stages of its life from requirements, moving to design, engineering, manufacturing planning and later to sales and maintenance. As a strategy, PLM helps cross-functional engineering and manufacturing teams to streamline operations, reduce costs, accelerate development, to improve product quality and support. By centralizing product-related data and enabling real-time collaboration, PLM supports decision-making and ensures data traceability across design, engineering, manufacturing, and service stages. The centralized product data is essential for manufacturing businesses to operate in the modern business and competitive environment – to innovate, control cost, manage turbulence of supply chain and maintain sustainability of products through the product lifecycle.
PLM (Product Lifecycle Management) software is a digital solution that enables engineering teams and manufacturing organizations to organize product-related data and processes throughout the entire lifecycle, from initial concept and design to manufacturing, maintenance, and end-of-life. It provides a centralized data management platform to manage product information, facilitating seamless collaboration across departments, and integrating with engineering systems (like CAD, CAM, CAE) and other enterprise systems like (ERP, CRM, MES, etc.) By organizing data and processes, the PLM digital platform ensures traceability of changes and helps businesses improve operational efficiency, enhance product quality, and accelerate innovation. PLM software together with other tools and technologies is an essential element in implementing your company’s PLM strategy for modern product development and manufacturing.
How OpenBOM Reimagine PLM Software
If you’re in the engineering and manufacturing business, managing a product’s lifecycle – from early ideation to maintenance and support – is critical. You may have heard of PLM (Product Lifecycle Management) and thought, “PLM is for large companies.”You may have heard that managing data using Excel and sharing files using Dropbox, Google Drive, or Sharepoint is all you need. While this might seem true when working on prototypes in your garage, scaling your product for even a handful of users quickly highlights the complexity of data management. Even a product with 100 parts can drive the level of complexity pretty high when you need to integrate multiple aspects of design (mechanical, electronics, software), manage changes, and connect to contractors and suppliers. The need for basic PLM principles to save time, reduce costs, and maintain quality is quickly becoming obvious.
But unfortunately, traditionally rooted in the complexities of aerospace, defense, and automotive industries, PLM has earned a reputation for being overly complex. At OpenBOM we say PLM doesn’t have to be that way. OpenBOM is reimagining PLM with a modern, accessible approach that breaks down traditional barriers.
Here are five key differentiators that set OpenBOM apart:
- Multi-Tenant Networking Platform: Connects design teams, manufacturers, suppliers, and contractors in a single collaborative, cloud-based ecosystem.
- Flexible Data Management with Intuitive User Experience: Combines powerful data management with a familiar spreadsheet-like interface for a seamless user experience.
- Seamless Integration: Works effortlessly with leading engineering and enterprise systems, ensuring smooth data flows across tools and departments.
- Open API for Customization: Offers an open API to support custom workflows and integrations tailored to your unique needs.
- SaaS Out-of-the-Box Accessibility: Ready to use in under a minute with a subscription-based model, enabling rapid deployment and immediate value.
By reimagining PLM and making it accessible to companies of any size, OpenBOM empowers manufacturers to achieve operational efficiency and success without the traditional complexity.
Digital Paradigm Shift and OpenBOM PLM Software
We live at the era of digital transformation and OpenBOM plays a key role in supporting engineering teams and manufacturing companies in this transformation from both data management and process management perspective.
The traditional document-based paradigm in engineering and manufacturing has long served as the backbone for organizing information. However, as products grow more complex and supply chains become more dynamic, the reliance on static documents creates silos, and inefficiencies, and limits the ability to adapt to rapid changes. These key challenges manufacturing companies are experiencing today:
- Product Complexity Growth
Increasing complexity demands interconnected, flexible data systems to manage intricate designs and processes. - Cost and Competition Pressure
Pressure to reduce costs and stay competitive highlights inefficiencies in traditional document-driven workflows. - Supply Chain Turbulence
Global disruptions require real-time data sharing and collaboration, which static documents cannot provide. - Traceability and Maintenance
Reliable traceability throughout the lifecycle is critical, but document-based systems often lack the accuracy and accessibility needed. - Regulation and Compliance
Ensuring compliance in a fast-changing regulatory landscape demands organized, reliable, and easily auditable data systems.
While 68% of industrial CEOs are investing in digital transformation, only 25% of manufacturers trust their data’s organization and reliability, exposing a critical flaw in the document paradigm. To meet the demands of modern manufacturing, it’s time to shift from a document-based approach to a data-driven paradigm that enables connected, real-time, and reliable management of engineering and manufacturing processes. This transformation is essential for navigating complexity, improving traceability, and achieving operational excellence.
Data management transformation supported by OpenBOM is a move from the management of multiple documents to cohesive data-drive-connected information.
Process management transformation supported by OpenBOM is a move from a document-driven email/spreadsheet/file-based process to a collaborative environment with a connected process.
OpenBOM Product Lifecycle Digital Twin
The foundation of OpenBOM PLM is a concept of product lifecycle digital twin. It represents an important technological trend in engineering and manufacturing, offering a virtual representation of physical objects, processes, and systems throughout their lifecycle. This dynamic model integrates real-time data, simulation, machine learning, and predictive analytics to inform better decision-making and optimize performance. By mapping product development and manufacturing as interconnected digital processes, organizations can make an analysis and impact of potential changes, analyze engineering complexities, supply chain disruptions impact, and also process inefficiencies. Beyond troubleshooting, the digital twin allows seamless planning, monitoring, and identifying new opportunities for product improvements, customer problems, and business opportunities.
Integrating Digital Twins Across the Product Lifecycle
The product lifecycle twin links engineering, manufacturing, support, and beyond, aligning with the vision of connected digital information.
This strategic integration supports resilience, adaptability, and streamlined workflows, addressing complex product development and manufacturing challenges while maintaining data consistency across the lifecycle.
OpenBOM’s Graph-Based Approach to Lifecycle Twins
OpenBOM advances the implementation of product lifecycle digital twins through its xBOM Product Knowledge Graph Model. The graph-based architecture empowers organizations to create tailored lifecycle representations, connecting critical organizational functions and ensuring accurate, accessible data management. By transitioning from document-based processes to connected data models,
OpenBOM facilitates seamless collaboration across design, engineering, and manufacturing teams. Its multi-tenant, flexible structure supports virtual xBOM views, enabling the creation of specific BOM types such as Concept BOM, EBOM, MBOM, and SBOM. These types provide clarity and control over distinct lifecycle stages, from initial design concepts to customer-specific configurations.
Practical Applications and Simple User Experience
OpenBOM’s introduction of xBOM types illustrates the practical value of lifecycle digital twins. For instance, the Concept BOM aids designers in validating initial item master data and concepts, setting a strong foundation for subsequent stages. The EBOM bridges design and manufacturing by ensuring accurate engineering documentation and CAD integration. The MBOM facilitates efficient production planning, vendor management, and cost optimization, while the SBOM streamlines sales configurations and after-sales support. Together, these xBOM types enable organizations to model, analyze, and optimize their processes comprehensively, driving innovation and operational efficiency across the product lifecycle.
The functionality of OpenBOM is supported by easy to use and flexible data-driven user experience. It is visual and intuitive.
Real-Time Data Management, Collaboration, and Data Sharing
The production life cycle definition starts from the information. Product information is a foundation of design, planning, and manufacturing. How do you manage it efficiently? How do you define the lifecycle of a product?
You can easily export data from CAD to Excel, but you will spend a lot of time making updates, especially if you add more data such as cost, suppliers, planning, and other pieces of information.
Data sharing is another challenge. Send emails with Excel is easy, but finding the right Excel is hard. You will make mistakes and your team will end up using the wrong Excel.
Think about counting unique parts in multiple CAD assemblies. It is tons of work. And if you add more items added outside of CAD, you can spend hours doing it and you will make mistakes.
Rollup cost is another level of complexity, translating units of measures used in BOM to purchasing units will turn you into a chief Excel officer.
Manual tracking of change history, revisions, and managing change approvals will slow down processes and will lead to mistakes.
So, you end up with wrong parts, purchase orders with mistakes, delays, additional costs, hard time to forecast, lost opportunity to use volume orders, and many other problems. Sending wrong information to contractors can be even more expensive and disruptive for business. Your team working with the wrong information will spend more time working on the wrong design and product planning.
The root cause of all the problems I described above is inefficient data management. Organizing and managing data in a modern distributed environment is a challenge that cannot be solved using traditional database systems or file servers. OpenBOM provides a uniquely flexible and scalable approach in data organization to manage different aspects of the product development process, change management, quality management system, maintenance, purchasing, and others.
These are the top 5 things that create a unique value proposition of OpenBOM:
Simplifying Complex Bill of Materials (BOM) Management
Product record and a single version of the truth. OpenBOM creates unique data records for all items and corresponding information – Part Numbers, descriptions, revisions, cost, manufacturer, suppliers, lead time, etc. Automatic quantity calculation, formulas, and custom rollups. You can combine multiple assemblies into a single multi-level BOM and automatically calculate everything you need for planning and purchasing.
OpenBOM excels at breaking down the complexities of BOM management by offering a cloud-native, graph-based data model. This enables users to create and manage multi-level BOMs with ease, ensuring data accuracy and traceability. With features like xBOM services, flexible data representation, and multi-view architecture, OpenBOM simplifies handling various BOM types (e.g., EBOM, MBOM, Service BOM) while providing intuitive tools for real-time updates and visualization.
BOMs use items and extend them with usage information (eg. Quantity, Project). The OpenBOM data model is flexible and you can extend it at any time. The extension is a big deal as it allows every company to be different, yet provides a way to organize the data.
Streamlining CAD Data Management and BOM Creation
OpenBOM integrates seamlessly with leading CAD systems, offering functionality that allows for real-time data synchronization. It automates the extraction of metadata and BOMs from CAD designs, eliminating manual data entry and reducing errors.
Automatic BOM creation and updates from any CAD system are simple with OpenBOM. You won’t need to count parts manually anymore. A single click on the button will create BOM and update it when you do it next time. All changes are tracked and revisions can be created
By bridging the gap between engineering and manufacturing, OpenBOM ensures that product data remains consistent, up-to-date, and easily accessible across the organization.
Improving Order Management (RFQ, PO, Inventory)
OpenBOM goes beyond traditional PLM by enabling efficient inventory control and order processing workflows. It supports RFQ (Request for Quote), purchase orders, and inventory tracking, ensuring that procurement aligns with the design and manufacturing processes.
OpenBOM provides support for an out-of-the-box purchasing planning process. OpenBOM creates an Order BOM (planning BOM), which can scale the quantity to the level of the order, keep track of stock level (quantity on hand), and automate the process of purchase order creation.
OpenBOM integrated approach allows users to manage vendor relationships, track parts availability, and reduce delays in production, fostering a more efficient supply chain.
Ensuring Accurate Data Transfer to ERP
The platform’s robust integration capabilities ensure smooth and accurate data transfer to ERP systems. OpenBOM bridges the gap between engineering (CAD, PLM) and enterprise systems (ERP, MRP), eliminating data silos and manual entry errors. This ensures that BOMs and associated data flow seamlessly into ERP environments, enabling better planning, resource allocation, and cost control.
Enabling Seamless Collaboration with Engineering Teams and Contract Manufacturers
Instant data sharing mechanism with a click of the button or automatic role-based sharing using team views. OpenBOM instant share and Google-sheet like collaboration and simultaneous editing will guarantee you have all information up to date shared with everyone.
OpenBOM empowers distributed teams and contract manufacturers with real-time, cloud-based collaboration. Its data-sharing capabilities allow teams to share and update BOMs, change orders, and production details without delays or miscommunication. By supporting granular user permissions and enabling secure data sharing, OpenBOM enhances collaboration across the entire supply chain, fostering trust and operational efficiency.
These value propositions make OpenBOM an indispensable tool for modern engineering and manufacturing organizations, offering a holistic approach to managing data, processes, and collaboration.
How to start using OpenBOM – Notes about adoption and implementation
For a long period of time, the selection of PLM was usually a complex process. PLM systems are famous for their complexity. How to start using OpenBOM, implement it successfully, and not be impacted by a typical “PLM fear”.
Addressing Common PLM Fears with OpenBOM
Adopting Product Lifecycle Management (PLM) systems has traditionally been daunting due to their complexity, extensive setup time, and the steep learning curve they demand. Engineers often resist switching from familiar tools like Excel, fearing compatibility issues, slow adoption, and a lack of tangible value. OpenBOM recognizes these widespread concerns and has designed solutions to simplify the transition to modern engineering software. By addressing these fears head-on, OpenBOM enables companies to confidently embrace digital transformation without sacrificing usability or flexibility.
Simplifying the Experience Through Familiarity
One of OpenBOM’s core strategies is to make the user experience approachable and intuitive. By offering a familiar spreadsheet-like interface, OpenBOM bridges the gap between traditional tools and advanced PLM systems. This design mirrors Excel’s usability while enhancing it with features like real-time collaboration and robust data management. The result is a system that feels instantly recognizable, helping users transition seamlessly with minimal resistance. Additionally, OpenBOM provides a free trial, allowing users to test the system firsthand and see how it can align with their workflows.
Integration and Compatibility for Effortless Adoption
To ensure a smooth transition, OpenBOM integrates deeply with popular CAD systems and supports seamless data import/export processes. This compatibility allows users to migrate their existing data from spreadsheets or other tools effortlessly while continuing to use familiar CAD environments. OpenBOM’s plug-ins and export capabilities eliminate fears of data lock-in, ensuring teams can adopt the system at their own pace without disrupting existing workflows. This dual approach fosters confidence in the software’s adaptability and reduces hesitation often associated with new systems.
Education, Support, and Simplified Product Loops
Education and ongoing support are critical to OpenBOM’s adoption strategy. Comprehensive resources, including articles, videos, and integrated application support, empower users to get help when needed. Furthermore, OpenBOM’s design focuses on a straightforward product loop: capturing CAD data with one-click functionality, collaborative editing with a spreadsheet-like UX, and seamless data sharing. This streamlined experience reinforces ease of use from the start, ensuring users can quickly achieve meaningful results with minimal training.
Onboarding and Commitment to User Success
To solidify adoption, OpenBOM offers tailored onboarding workshops and dedicated support during the trial and beyond. These personalized sessions guide users through specific functionalities, fostering confidence and competence. By prioritizing simplicity, familiarity, and user-centric design, OpenBOM removes traditional PLM fears and positions itself as a practical solution for digital transformation. For companies looking to modernize product information management, OpenBOM provides an accessible pathway with measurable value from day one.
So, where to start?
How to organize product information using OpenBOM? It is important to learn about potential mistakes. The following example will demonstrate to you what means to build a product lifecycle in OpenBOM.
OpenBOM helps you to organize information about the product. As much as it sounds simple and obvious, the organization of the data is one of the most important and complex processes to accomplish in the organization. Even the smallest organization with just a few people can create an enormous amount of complexity by not organizing data.
As I always say to our customers, if you have a mess, don’t bring the computer to the mess. Because it will create a “computerized mess”. You need to clean the data, and think about data organization, classification, storage, semantics, files, and many other things. But, don’t worry, it is not as complex as it might sound in the first place.
Here is a process we recommend to have when you start working with OpenBOM to organize data and properly capture the information you have in the company.
Identify the existing data sources
It is very important to start with the data in the first step. How the data is created, and what systems are used to generate the data. If information is created manually, then who does it, and who controls the data sources? The data source can be an Excel file, it can be an export from an existing system or it can be CAD files or local databases. To find all data sources, to decide what to do, what information will be transferred to OpenBOM, and what information will stay with existing data sources, how data will be exported and synchronized is the first step to understanding how to organize data.
Classify items and the way to collect item information
Classification of information is the process of identifying what pieces of information need to be managed and how to identify data. A typical process of information classification includes defining Part Numbers and typical attributes that are managed on the item level and instance level.
Item information represents the data that is the same for all usages of the item (think description, cost, manufacturer, etc. Data is organized in catalogs and the OpenBOM catalog defines the set of attributes for all items stored in this catalog. A set of catalogs is a classification schema. Classification can be different for each company. Usually includes types of items (standard, engineering), can include contractors, or any other specific ways to classify.
To define a continuous process to create items
Once you identified sources of item information you need to decide how to manage this information. The main part of the process is to create an Item. In OpenBOM you can create items in multiple ways. The easiest and simplest one is just adding an item to the catalog manually. Similarly, if you need to add an item directly from the CAD system, you can use the OpenBOM CAD Add-in “Save Item” command.
Another way to add items is to get them continuously imported to the catalog using Import Command. Catalog import is a powerful tool to import new item data and also import some other and merge it with the information about available items.
The last method, you can think about is to save “Create/Update Catalog” commands from OpenBOM CAD add-ins. This command can take an entire set of parts and sub-assembly in a specific design and export it to a catalog.
To organize access control and change process for items
OpenBOM access control is based on data ownership and sharing settings. If you’re a single OpenBOM user, nobody except you has access to item data by default. In order to get access, you will need to share the data manually. You can share with anyone who has an OpenBOM account using the Share command.
If you’re part of the OpenBOM Team or Company, you can share automatically the data. The default access levels are none, read-only, edit, and View. The last method involves the definitions of Team Views. Each user in the team (or company) will have a list of applied views and the list will restrict the data access.
Where to continue and get more information?
It is easy to start using OpenBOM. You can do it by registering for free and starting your journey. The OpenBOM team will support you all the way through the process. Here are some useful resources and recommendations:
- Start simple, creating a minimum viable prototype to check your ideas
- Watch videos, live demos, and training sessions
- Read online documentation
- Ask OpenBOM Support
Once you decide to embark on your OpenBOM journey, we will provide you with the custom-tailored onboarding process. Contact our support to learn more.