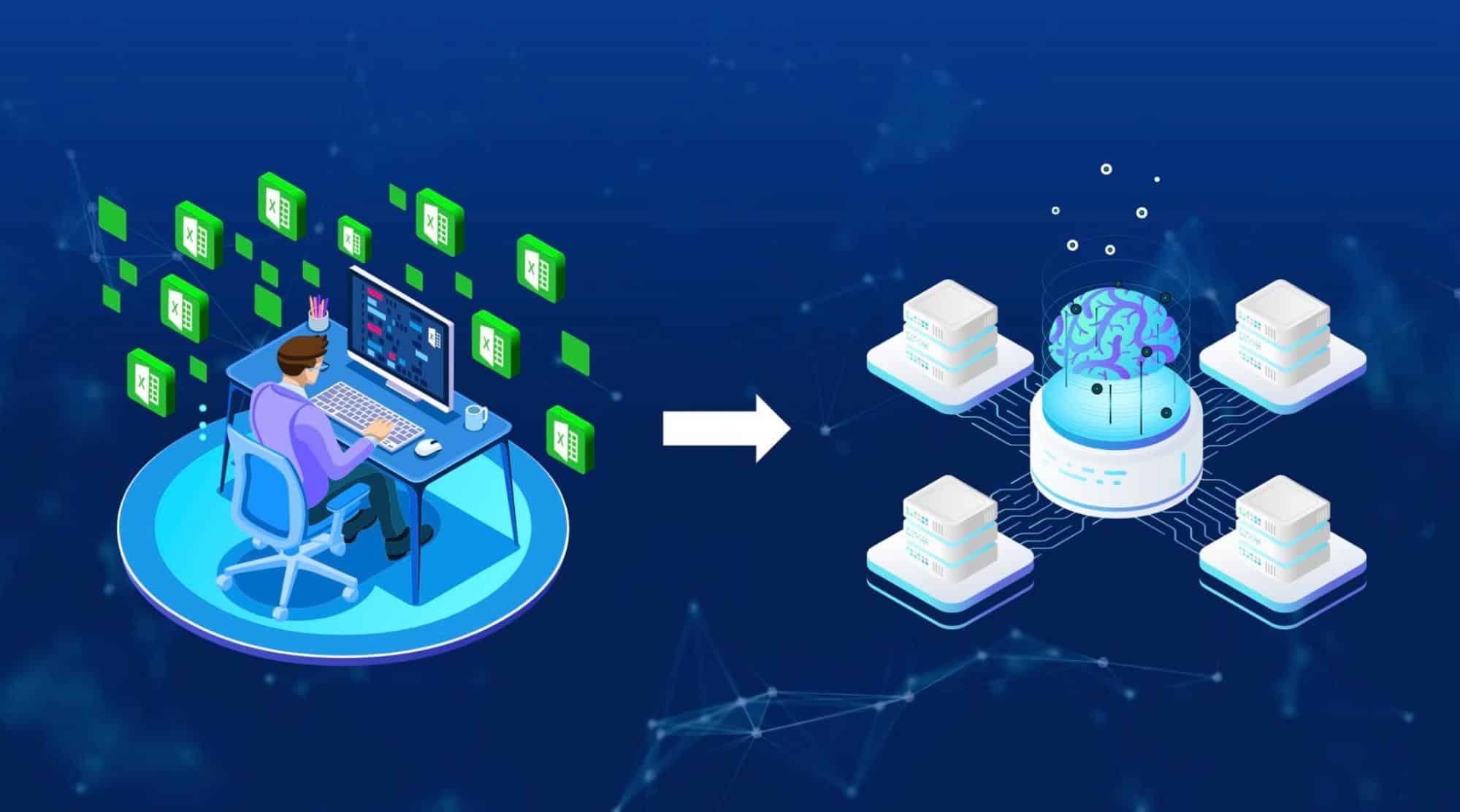
In today’s economy, manufacturing companies are under pressure to be more efficient and reduce costs. Process improvement is a key part of achieving these goals, and businesses are looking for ways to improve their operations. Manufacturing companies are under continuous pressure to improve their process. In the modern data-driven world, there is a huge cost of not having a data management strategy.
In this blog post, we’ll discuss some of the most common process improvement techniques and how they can help your business. We’ll also provide tips on how to get started with process improvement.
Forget the past
Change is hard. Even if a company understands how bad and unreliable Excel can be, to make a switch requires an effort. The real difficulties lie not so much in developing new ideas as in escaping from old ones. Modern cloud technologies create a huge acceleration to think about new PLM development and escaping old Excel ideas. However, as much as companies moved forward, old Excel ideas kept the systems at the same place, and ideas deteriorated towards only using Excels and old document servers instead of modern cloud-native PLM systems.
Check out our article – How to Escape from Old Excel Ideas to learn about typical paradigms many companies are trying to continue using when moving from their Excel data management practices to modern PLM systems. Here they are and the problems they will cause you.
- Excel for A Project (data is connected and goes beyond a single file boundary)
- Pseudo-hierarchies (it is important to manage data structures and where used)
- Copy data (copy of the data brings redundancy and kills a single source of truth)
- Excel spaghetti (linking values between Excel files creates a mess)
A Foundation of Data-Driven Processes
Here is the question we often hear from companies – can you help us copy a BOM from CAD files to our ERP (MRP) system? At first glance, it sounds like a very legitimate question and the need of the company to keep data flowing and help to organize processes, but I often recommend to these companies to take a deeper look at how data and processes are organized and what is the value of a single source of information about the product as well as multi-disciplinary BOM (xBOM) data management strategy.
The danger of sending data from one application to another, or what is called “point-to-point” integration is in the creation of multiple data silos that are disconnected and don’t present a continuous set of information to an entire organization.
In the past, CAD and PDM systems formed a silo, which was represented by engineers and R&D organizations. Most of the products were simple and a single CAD file provided a pretty much clear representation of what is in the product. Even so, if the CAD file didn’t provide a full data representation, it worked. Mistakes happened, but it was less dramatic than it is now.
A modern product includes multiple sub-systems and includes mechanical, electrical, PCB, and software components. The data about the product is not coming from a single CAD and must be collected from multiple data sources and also validated by multiple users. Teams must use a PLM system (or BOM management system) to incorporate product development and change management processes, at least, to establish a unified multi-disciplinary BOM structure representing all systems and elements of the product.
5 Typical Mistakes In Data And Process Planning
Working with thousands of engineers and manufacturers, I found the following five mistakes in data management strategic planning that can cost your company a lot of money down the road of manufacturing, delay your production schedule, and impact the total cost of the product (or project).
- Use siloed (not connected) data management – CAD, PDM system, Inventory System
- Not having a single source of product information and changing history
- Use Excel and emails to exchange information
- Use Manufacturer or Supplier identification for components in the Bill of Materials
- Relies on part lists on Drawing as a BOM management system.
The absence of a centralized database or reference system containing a comprehensive set of information about the product, revisions, and history of changes, which includes reference to all data sources used for product definition might sound like a big task for manufacturers. However, not having a data strategy will fire back and return with an increased cost of changes, missing cost goals, and production delays.
Conclusion
One of the biggest mistakes manufacturing companies makes by oversimplification of data management challenges…It often sounds like this – “we just need to send a CAD part list to our inventory system” to order parts. What is behind such a mistake is a tunneled vision and siloed task management. Engineers feel like their tasks are done by exporting Excel spreadsheets from the CAD system and shouting it over the wall of manufacturing to whoever is supposed to take care of manufacturing planning. The cost of such mistakes is huge and usually found too late.
REGISTER FOR FREE to check how OpenBOM can help you to establish the right data management strategy and create a foundation for product data management, creating a single source of truth and connecting people and systems into a single connected data-driven collaborative process.
Best, Oleg
Join our newsletter to receive a weekly portion of news, articles, and tips about OpenBOM and our community.