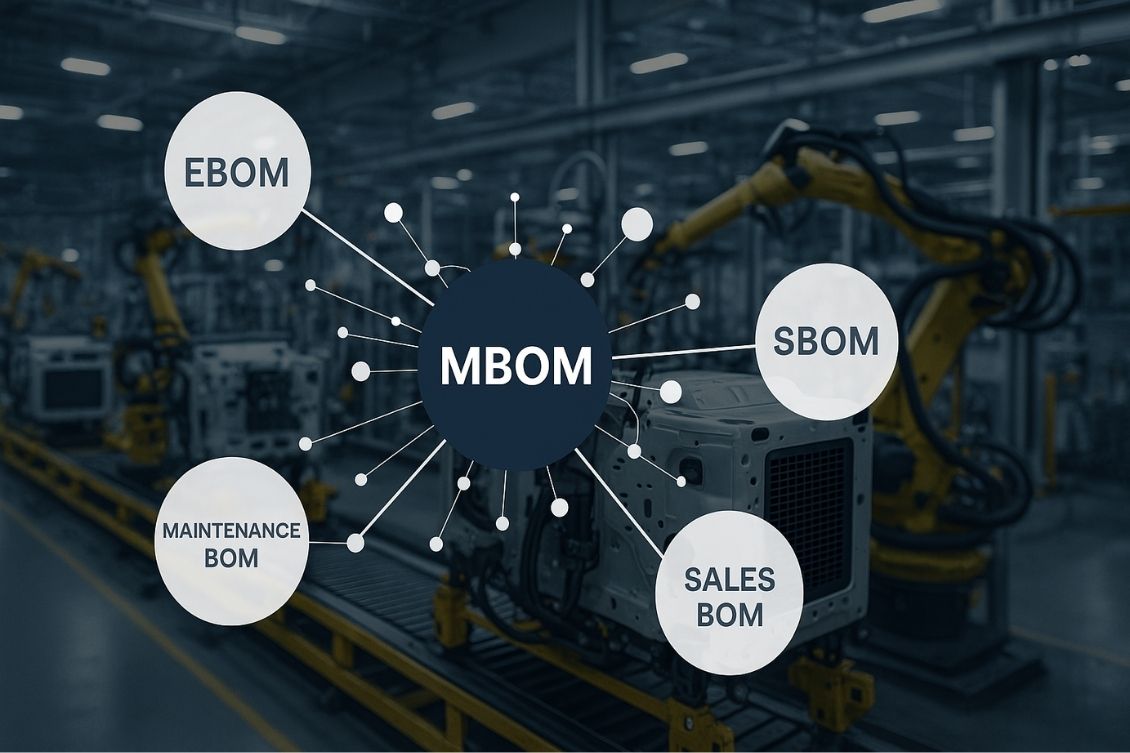
Every product starts with an idea – but to turn that idea into a complete and shippable product, you need structure, coordination, and detail. That’s where the Bill of Materials (BOM) comes in.
In manufacturing, the bill of materials is the foundation for everything: design, production, procurement, assembly, and service. It tells you about all the materials and components of the final product and how they come together. Among the different types of BOMs, the Manufacturing BOM (MBOM) plays a critical role in bridging the gap in the product lifecycle between the design process and execution.
Over the years, manufacturing BOMs have evolved. From static spreadsheets to dynamic, connected product structures, they’ve become a central tool for driving efficient, scalable, and resilient operations. Let’s unpack what Manufacturing BOM really means, how it’s different from other BOMs, and why it’s now considered a critical pillar of modern manufacturing and supply chain strategy.
What is a Manufacturing Bill of Materials MBOM- and How is it Different?
An MBOM, or Manufacturing Bill of Materials, is a detailed and structured list of all components, raw materials, operations and assemblies required to build and ship a finished product (a production recipe).
What makes the MBOM unique is that it reflects how the product is manufactured, not just how it’s designed. While an Engineering BOM (EBOM) follows the structure defined by the product’s CAD models and design’s hierarchical structure, the manufacturing BOMs reorganize that data to match the actual production process. It includes packaging, tooling, consumables, and other non-design items needed for assembly.
The MBOM is also tightly connected to other integrated business systems involved – enterprise resource planning (ERP), manufacturing execution system (MES), and supply chain management (SCM). It informs purchasing, drives shop-floor execution, and supports precise tracking of inventory and cost estimation. In short, the manufacturing BOM is where engineering meets reality.
Manufacturing BOM: All the Components and Structure
An effective manufacturing BOM isn’t just a list of different components. It’s a structured, hierarchical model of how a finished product is built. It typically includes:
- All the parts and subassemblies, including manufactured, purchased, and outsourced components required to create a product.
- Manufacturing process steps and operations, such as welding, painting, or firmware loading.
- Consumables and packaging, like adhesives, tapes, fasteners, and labels.
- Metadata such as supplier names, part numbers, cost, lead time, revision, and compliance requirements.
- Alternate or substitute components, where applicable.
- Routing and production sequencing, which align with the bill of process (BOP) or manufacturing workflows.
Unlike the engineering bill of materials, which follows design logic (like functional grouping), the manufacturing BOM is organized according to how the product is assembled, often based on workstations, kits, or production phases.
Why Manufacturing Bill of Materials Matters: Beyond the Assembly Order List
While an oversimplified approach presents MBOM as a list of components needed and the way the assembly process is organized, the MBOM is much more – it delivers real, measurable benefits.
- Production Efficiency: By reflecting the actual assembly process, the MBOM helps streamline work instructions and minimize errors on the shop floor.
- Cost Control: With accurate materials and operations listed, cost roll-ups can be calculated more reliably and early in the process.
- Procurement Specification: The MBOM informs ERP systems on what to buy, when, and from whom. This reduces inventory mismatches and late orders.
- Compliance and Traceability: Especially in regulated industries (medical, aerospace, automotive), the MBOM helps document what was built, when, and with which components.
- Cross-Functional Collaboration: When done right, the MBOM becomes a shared asset between engineering, manufacturing, and supply chain teams.
Process and Best Practices: From Engineering BOMs to Supply Chain Intelligence
Over the years, the way companies approach manufacturing bill of materials has evolved dramatically. What started as a simple parts list has become a dynamic model that connects design, production, and supply chain. Let’s explore three common approaches to MBOM and one key trend that’s transforming all of them.
MBOM Phase 1: The Single BOM Era (ERP-Centric Approach)
Let’s start with the most traditional model – the one that’s been in use for more than 20 years. In this approach, the MBOM is the only BOM. It lives in the ERP or MRP system and serves as the master source for everything manufacturing needs.
Back in the day, CAD tools were mostly used to produce 2D drawings. Once those drawings were finalized and released, manufacturing or ERP teams would manually create the BOM from them. It was often a painstaking process – transcribing parts, quantities, and notes from engineering documentation into the ERP system. The MBOM was flat, static, and often built with little to no input from engineering.
Characteristics:
- MBOM is authored and maintained manually in ERP.
- Design and manufacturing teams operate in separate silos.
- Drawing releases trigger BOM creation—no data until design is “done.”
- No structured hand-off from CAD to manufacturing.
Use Case Fit:
- Companies with simple products or limited product variation.
- Organizations heavily invested in legacy ERP systems.
- Environments where product changes are infrequent and tightly controlled.
Challenges:
- Late discovery of manufacturability or sourcing issues.
- No traceability between design revisions and BOM structure.
- Manual data entry errors are common.
- BOM change processes are slow and costly.
MBOM Phase 2: The Restructured EBOM (PLM-Centric View)
As product lifecycle management (PLM) and product data management (PDM) systems became more prevalent, companies began to see the value of building MBOMs from structured engineering data. In this model, the Engineering BOM (EBOM) is the starting point, and the MBOM is derived by reorganizing or enriching it to match manufacturing needs.
This approach allows manufacturing engineers to reshape the product structure to reflect how the product is actually built, reordering operations, introducing phantom assemblies and subassemblies needed, or grouping components by production steps. The MBOM becomes a more accurate representation of assembly sequences and production flows.
Characteristics:
- PLM/PDM holds the EBOM; MBOM is created by transformation or restructuring.
- Manufacturing input is added for routing, tooling, and operations.
- Tighter integration between engineering and manufacturing teams.
- BOM revisions are managed via formal PLM workflows.
Use Case Fit:
- Mid-sized to large organizations with cross-functional product teams.
- Companies that require traceability between design and production structures.
- Environments with frequent design changes or multiple variants.
Challenges:
- PLM systems may not integrate easily with ERP or MES.
- Restructuring can be time-consuming and prone to errors if not automated.
- Engineering teams may resist releasing design data early enough.
- BOM alignment between EBOM and MBOM can drift over time.
MBOM Phase 3: Foundation of Production and Supply Chain Optimization (Data-Centric Model)
This is the most modern and forward-looking approach. Here, the MBOM is not just a transformation of design data – it’s a rich, structured model that connects all the dots: from CAD to suppliers, from cost estimates to production workflows.
The manufacturing bill of materials is created early in the product development cycle and evolves continuously. It includes supplier-specific components, cost roll-ups, lead times, sourcing alternatives, and availability constraints. This allows companies to assess manufacturing feasibility, cost, and supply risk in real time, well before design is finalized.
Characteristics:
- MBOM is built as a flexible, multi-view structure with links to design, sourcing, and production systems.
- Supports alternate parts, make/buy decisions, and supplier-specific configurations.
- Includes metadata like cost, lead time, scrap rates, and compliance flags.
- Functions as a digital thread element across departments and systems.
Use Case Fit:
- Companies working with complex products or high-mix, low-volume production.
- Organizations with distributed teams, contract manufacturers, or multi-site operations.
- Environments that need agility in response to supply chain or design changes.
Challenges:
- Requires strong integration between PLM, ERP, MES, and sourcing tools.
- Demands flexible, often graph-based data models and not just hierarchical structures.
- Cultural shifts are needed to support cross-functional ownership of BOMs.
- Investment in modern platforms and scalable data infrastructure is essential.
Early MBOM Visibility
Regardless of which approach a company takes, there’s a clear and universal trend emerging: waiting until the design is finalized to create an MBOM is no longer acceptable.
Modern manufacturing requires early and incremental visibility into manufacturing data. This means creating and refining the MBOM in parallel with design, so that potential issues related to cost, sourcing, and manufacturability are identified long before they become expensive problems.
With early MBOM visibility:
- Engineers can get feedback on part availability and cost implications while still designing.
- Buyers can flag long lead-time components before they affect delivery.
- Manufacturing teams can provide input on assembly constraints during early prototyping.
This trend is reshaping not only how BOMs are built, but also how organizations collaborate. The MBOM becomes a living product model – one that grows, adapts, and ultimately drives better decisions from concept to production.
Integration: MBOM Meets Digital Systems
The MBOM doesn’t live in a vacuum. It’s part of a broader digital ecosystem that includes PLM, ERP, MES, and SCM platforms. To be truly effective, the MBOM must be deeply integrated with these systems. The tighter the integration, the greater the impact on operational efficiency, cost control, and supply chain agility.
The MBOM typically connects to:
- PLM systems to receive design intent, EBOMs, and engineering change data.
- ERP systems to support procurement, inventory planning, cost rollups, and materials management.
- MES systems to deliver shop-floor instructions and manage routing and production steps.
- BOP (Bill of Process) to align materials with the actual manufacturing process, including steps, tools, and work centers.
However, the critical point is that the MBOM can reside in different systems, depending on your company’s IT architecture, process ownership, and legacy system landscape.
- In engineering-driven organizations, the MBOM often originates or resides in the PLM system, where the EBOM-to-MBOM transformation occurs, and engineering maintains control over the product structure.
- In manufacturing- or supply chain–driven organizations, the MBOM may be created or maintained in the ERP system, where procurement, planning, and production teams take ownership.
- In some cases, companies implement hybrid approaches, with MBOM data synchronized or federated between PLM and ERP systems or even maintained in a specialized MBOM system that bridges both domains.
This architectural choice influences everything from how changes are managed to where master data resides and how workflows are automated.
A key principle remains: the MBOM must be dynamic, version-controlled, queryable, and extensible. Static spreadsheets or document-based BOMs can’t support today’s pace of change or manufacturing complexity. Modern architectures, especially those leveraging graph-based or composable data models, enable a more fluid, real-time MBOM that:
- reflects actual product configurations,
- supports alternates and substitutes,
- can respond quickly to disruptions in design or supply.
Ultimately, integration is not just about syncing data. It’s about aligning ownership, processes, and responsibilities across systems to ensure a consistent, actionable view of how your product gets built.
MBOM in OpenBOM
As companies look to modernize their MBOM strategy, tools like OpenBOM provide a significant advantage. OpenBOM goes beyond traditional BOM software by offering a flexible xBOM model that supports multiple BOM views, including EBOM, MBOM, and service BOMs, all connected through a single data infrastructure.
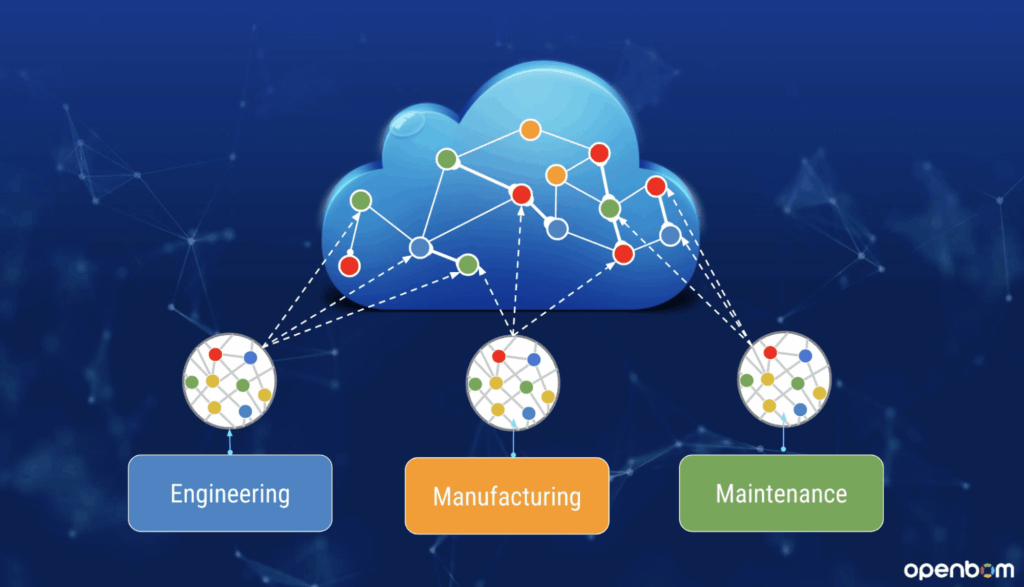
With OpenBOM, manufacturers don’t need to force-fit their BOMs into rigid templates or workflows. Instead, they can create and evolve a dedicated MBOM structure with downstream manufacturing domains and processes that reflects exactly how their products are built and sourced. This MBOM can be linked to specific inventory items, engineering data, supplier information, manufacturing sequences, or even cost breakdowns, creating a rich, connected product model.
OpenBOM’s Item lifecycle and change tracking capabilities ensure that all revisions, updates, and modifications are captured, so teams always know what changed, when, and why. This traceability is critical for compliance, auditability, and quality control, especially in regulated industries.
And perhaps one of the most unique advantages? The OpenBOM Graph Navigator. It allows teams to explore complex product structures visually, navigating through interconnected parts, sub-assemblies, vendors, and configurations in an intuitive, graphical format. It’s not just about seeing the data – it’s about understanding how all parts relate and everything fits together.
Whether you’re creating an MBOM from scratch or restructuring your EBOM for manufacturing, OpenBOM provides the tools and flexibility to do it right and evolve it over time as your processes mature.
Conclusion: Building the Future of MBOM
The MBOM is no longer just a downstream artifact. It’s a strategic structure that helps teams deliver high-quality products, fast and at scale.
Whether your organization still relies on legacy ERP-driven BOMs or is moving toward an integrated, AI-ready product data model, the direction is clear: early collaboration, flexible data structures, and supply chain awareness are becoming the norm.
To succeed, teams must treat the MBOM as a living model, not just an output from design. Build it early. Keep it connected. Let it evolve.
And with platforms like OpenBOM, you have the infrastructure to do exactly that – organize, trace, and navigate your MBOM with confidence.
Interested in discussing how OpenBOM can help you to organize your manufacturing BOM planning process? Talk to us.
REGISTER FOR FREE and check how OpenBOM can help.
Best, Oleg
FAQ
What is a Manufacturing BOM?
An MBOM, or Manufacturing Bill of Materials, is a detailed and structured list of all components, raw materials, operations and assemblies required to build and ship a finished product.
What are the Types of BOMs?
The most common are engineering and manufacturing BOMs. There are also single-level BOM, multi-level BOM, assembly BOM, production BOM, sales BOM, procurement BOM, Configurable BOM, Indented BOM, Phantom BOM, and Abstract BOM.
What are the Benefits of MBOMs?
Implementing an MBOM allows companies to improve production efficiency, inventory management, collaboration between multiple departments, cost and quality control, and reduce the number of errors and mismatches.
Join our newsletter to receive a weekly portion of news, articles, and tips about OpenBOM and our community.