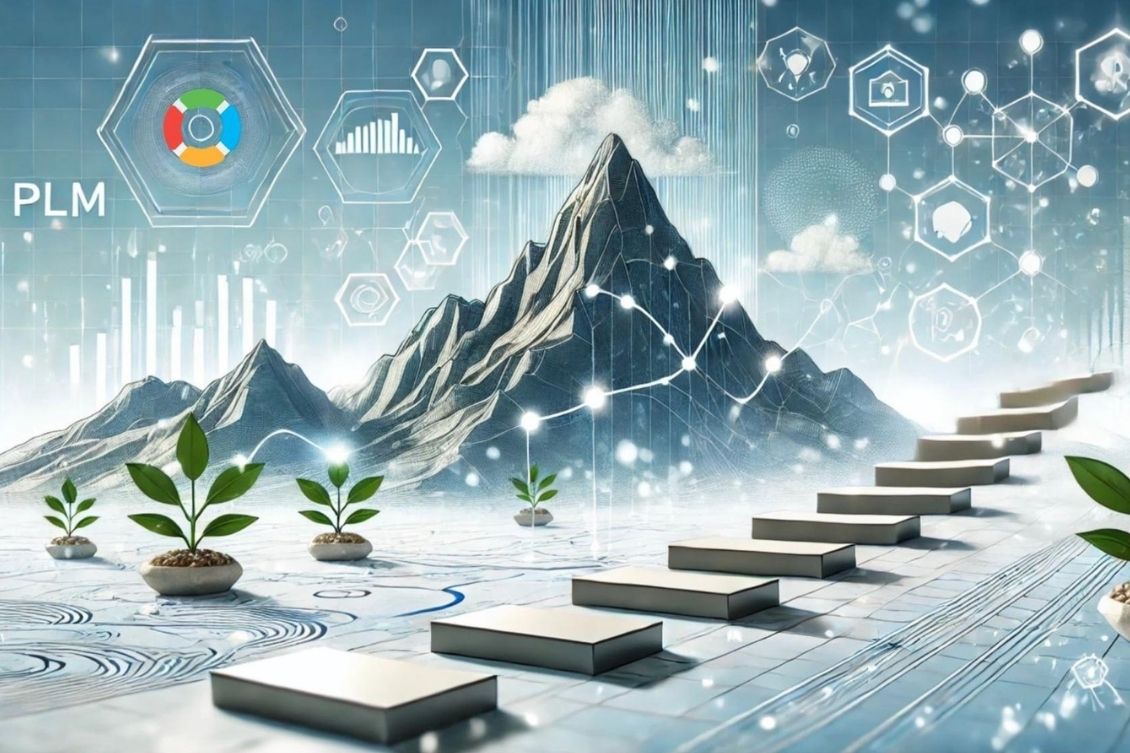
Product Lifecycle Management (PLM) is often described as the backbone of product development and manufacturing. However, if you do some reading, the complexity of PLM implementations in the manufacturing world is overwhelming and when companies try to embark on their PLM journey, they can feel it is actually too much for them. The potential benefits—streamlined processes, improved collaboration, and better data management—can get buried under the weight of complex setups, terminology, and integration challenges.
Therefore, for many years PLM was considered as something that was only needed for large companies and industries focusing on complex products such as aerospace, defense, automotive, and heavy industrial solutions – machinery, equipment, and similar products.
However, things have been changing for the last decade from both sides – the complexity of products has increased significantly. These, even products that for many years were considered simple, are growing in complex systems including mechanical, electronics, and software systems. These companies now demand solutions that go beyond what a bunch of Excels and File Folders can support. Here is only a short list of problems we are finding today in these companies – product complexity growth, cost and competition pressure, supply chain turbulence, traceability and maintenance, regulation and compliance.
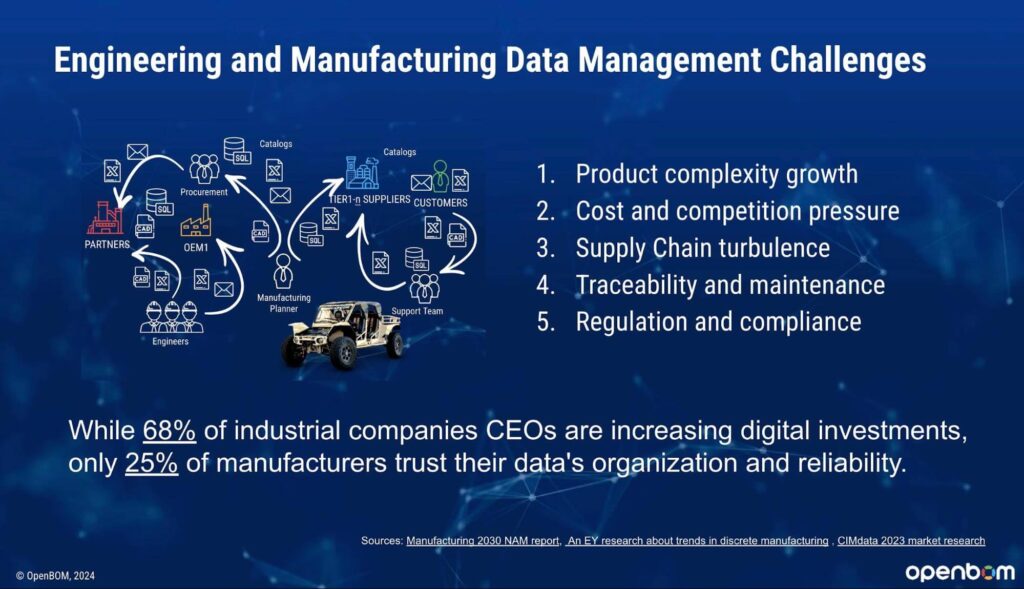
In this article, I want to explore why PLM feels so daunting initially and how you can simplify the process to ensure a successful implementation. As a bonus point, I will also include some very specific characteristics of OpenBOM that help you avoid complexity during implementations.
Why PLM Feels Overwhelming at the Start
Ask every engineering team about PLM and you might see them rolling their eyes saying that PLM is not for them. I can see the reasons for that coming from both sides – customers and software vendors. I cannot blame both- one side (vendors) was trying to provide the most sophisticated software to solve complex problems and another side (customers) was trying to avoid data management by sticking to the simplicity of files and Excel.
From the experience of talking with many industrial companies and engineering teams here are the top reasons why PLM feels overwhelming to touch and avoided by many.
- Unclear Scope and Expectations Many organizations dive into PLM without a clear understanding of their goals. They expect the system to solve all their problems instantly, PLM is not a magic pill that you can swallow with water and get done – it’s a system that requires alignment with specific objectives.
- Complex Terminology and Concepts PLM software and vendors often come with a steep learning curve. Terms like EBOM, MBOM, digital thread, and configuration management can confuse teams who are not familiar with these concepts.
- Data Chaos Before implementing PLM, most companies rely on spreadsheets, shared drives, or legacy tools. Consolidating this scattered data into a structured system feels like trying to untangle a giant knot.
- Integration Challenges PLM rarely exists in isolation. It must integrate with CAD, ERP, CRM, and other enterprise systems. This adds technical complexity that can stall progress.
- Resistance to Change People are often comfortable with their existing processes, even if they are inefficient. Introducing PLM disrupts workflows and requires significant effort to train and adopt new practices.
- Over-engineering the Solution Many companies overcomplicate their PLM system from the beginning. Instead of starting small, they attempt to solve all issues, and deploy every feature and function, leading to bloated configurations that are hard to manage.
Let’s speak about some best practices that help to streamline product lifecycle management, connect product design with manufacturing processes, and help manufacturing companies deal with all the challenges the modern business environment in the manufacturing sector brings to them.
How to Fix It: A Practical Approach
What is the practical approach that can help companies in the manufacturing business to improve engineering and product development processes, organize design projects, CAD files, and product data, connect mechanical engineering with electronics and software, optimize contract manufacturing, optimize production planning, and integrate all other systems to support a consistent change management processes?
Here is the list of guidance that can help you connect engineering and manufacturing processes, optimize data management, and ensure the company creates a solid foundation for the business to survive the next industrial revolution.
1. Define Clear Objectives Business comes first. Remember Albert Einstein recommended spending 50 minutes of an hour to understand what is the problem and 10 min to find a solution. Start by asking, What problems are we solving? Focus on specific pain points like improving design collaboration, managing BOMs, or ensuring traceability, management of cost, and support regulation. Clear goals help prioritize features and avoid unnecessary complexity.
2. Adopt an Agile Implementation Instead of a big-bang approach, implement PLM in phases. Begin with a minimally viable solution that addresses immediate needs, then expand functionality as your team becomes comfortable.
3. Simplify the Data Migration Process Use the 80/20 rule for data migration. Focus on the most critical data first—like active projects, current BOMs, and supplier information. Modern PLM systems, like OpenBOM, offer flexible data models that simplify this step. You can start with a very simple data model created automatically and then expand.
4. Leverage SaaS and cloud-based PLM Even if you think that you’re afraid of taking your data to the cloud, you need to be aware that SaaS and cloud-based PLM solutions made huge progress over the last decade improving security, reliability, and performance to support very complex use cases. Cloud-based systems can reduce the burden of infrastructure setup and provide out-of-the-box integrations. They also offer scalability and faster deployment times, making them ideal for companies that want to start a PLM journey. A free trial of fully functional systems like OpenBOM can give you a touch of what you can get in an instant way.
5. Provide Proper Training and Support A lack of training is one of the biggest reasons for poor PLM adoption. Invest in user-friendly onboarding, regular training sessions, and a support structure to address issues quickly.
6. Start with the Basics Focus on fundamental PLM capabilities before diving into advanced features. For example:
- Centralized file and data storage
- Centralize data access
- Focus on how to manage the history of changes and revision control
- Basic BOM management to combine mechanical, electronics, and software data
7. Once your team masters these, you can layer on additional capabilities like digital threads or advanced analytics.
8. Encourage Collaboration Across Departments PLM is not just for engineering. Engage teams from manufacturing, procurement, and even sales during the implementation to ensure the system meets cross-functional needs. The simpler will be data sharing, the more value your company will get from PLM
9. Partner with an Expert Working with an experienced PLM consultant or vendor can make all the difference. They can help you avoid common pitfalls, set realistic expectations, and tailor the system to your specific needs.
The OpenBOM Approach: A Smarter Start for Digital Transformation
At OpenBOM, we understand that the initial stages of PLM can be intimidating. Therefore, we developed a 3 3-point strategy for your PLM implementations. Here they are (1) digital BOM, (2) seamless design integration with multi-CAD, and (3) integrated production management, RFQ/PO, and ERP integration. OpenBOM brings 2 dimensions of transformation to your company: data and process transformation.
In data transformation, OpenBOM ensures you move from the chaos of disconnected documents to organized product data.
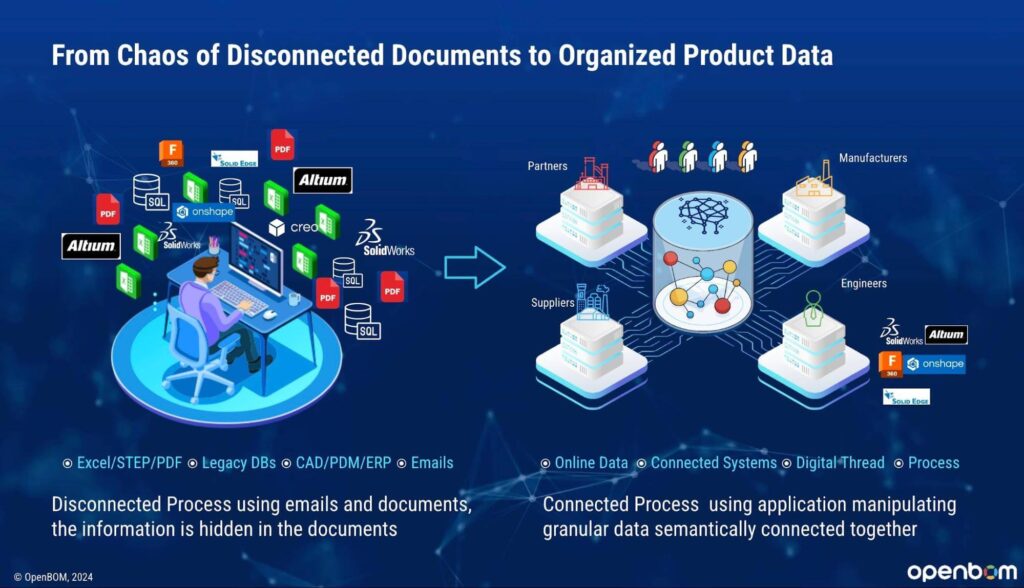
From the process transformation, OpenBOM allows you to move from complex email and document flow to connected data-driven processes.
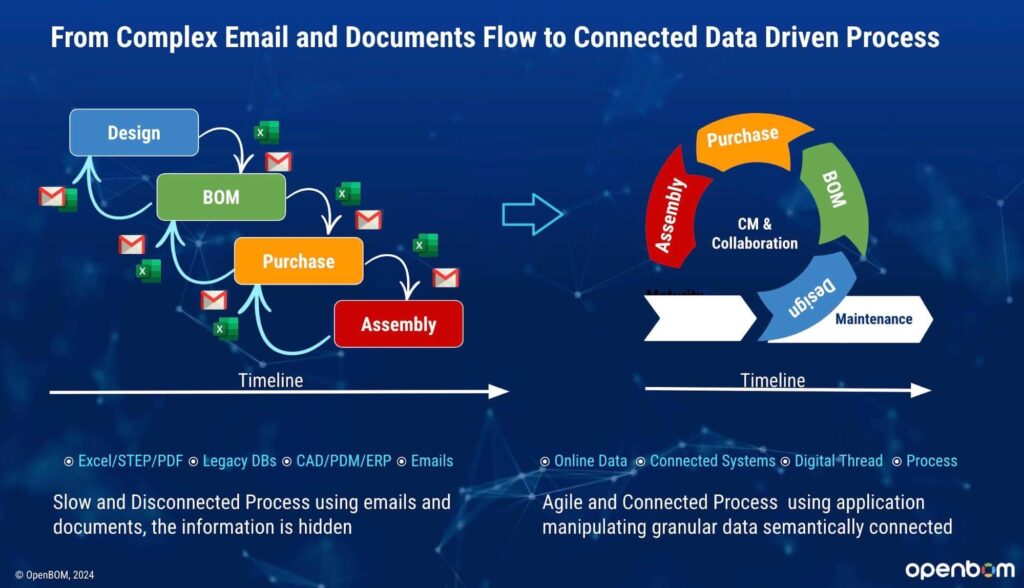
However, in everything OpenBOM does, the main focus is on simplicity, flexibility, and collaboration. OpenBOM cloud-native platform provides a fast, efficient way to get started with PLM without significant preparation. Here they are:
- Flexible Data Models for Digital BOM: Adapt to your processes, not the other way around.
- Out of the box integration capabilities: Deploy rapidly and integrate with systems you’re using on a daily basis (MCAD, ECAD, ERP, and others).
- Simple UX and Real-Time Collaboration: A familiar “spreadsheet-like” user experience and “Google docs like” real-time collaboration allow teams to work together.
On top of all these capabilities seamless export of data to familiar Excel, PDF, and CSV formats ensure portability of data in case you need to communicate with teams that are not ready to adopt the solution yet.
Conclusion
PLM doesn’t have to feel like climbing a mountain. By starting with clear goals, focusing on the basics, and using modern tools like OpenBOM, you can ease the transition and set your team up for long-term success. Remember, PLM is a journey, not a one-time event. Start small, stay focused, and build on your successes over time.
Are you ready to take the first step? Contact OpenBOM today to learn how we can simplify your PLM journey.
Best, Oleg
Join our newsletter to receive a weekly portion of news, articles, and tips about OpenBOM and our community.