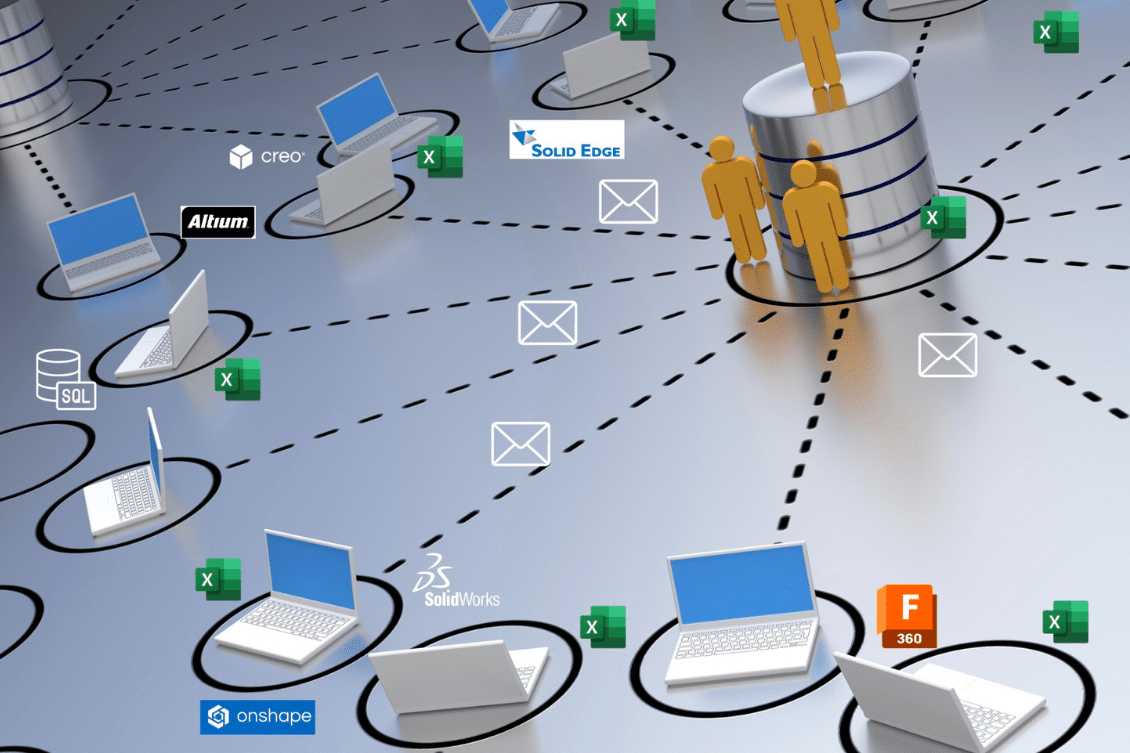
Engineering and manufacturing industries are becoming increasingly reliant on data-driven processes to streamline operations and enhance productivity. At the same time, if you ask engineers, production planning, and operation managers they are heavily unaware of what can be done to improve data management. Many companies and engineering teams I have spoken with are relying on rudimentary data management ideas and systems such as Folder/Files, Cloud File Storages, Spreadsheets with formulas, and some additional ‘homegrown solutions’.
I appreciate the creativity of engineers trying to solve these problems alone. However, with the vast amount of engineering data generated throughout the product lifecycle and business systems, managing engineering and manufacturing data can be a daunting task.
Earlier this week, I shared a series of articles where I was speaking about what I learned from talking to engineering teams and manufacturing companies with regard to their data management tasks and problems. I’ve heard a lot of really painful stories. Check out my articles below:
- The pain of engineering data management
- The Pains of Collaboration in Engineering and Manufacturing Organizations
- OpenBOM Engineering and Manufacturing Data Painkillers Series
- Addressing Painful Siloed Data and Information Flows in Engineering and Manufacturing Processes
In this blog, I’d like to summarize everything we learned and share my take on the top 7 pains of engineering and manufacturing data management. I also want to discuss how organizations can address these challenges.
Data Organization and Silos:
One of the most common challenges in data management is the existence of data silos. Different departments within an organization often store data in isolated systems, making it difficult to access and share critical information. This lack of integration can lead to inefficiencies, miscommunication, and delays in decision-making.
Bluntly put, files are everywhere. Engineering data (e.g. CAD files) are not managed well. Engineers place them on their local computers and shared drives (both network and cloud). The data is copied between projects, so you can easily find multiple records about the same resistor in multiple Excel or multiple Solidworks part files with the same screw or some other OTS component.
Complexity and Scalability:
Modern products are complex. You have mechanical, electrical, PCB, software components. To organize this information together you need to apply some methodology and tools. Multiple CAD systems and other design tools are used by engineers. The traceability of revisions is becoming a nightmare. Production is outsourced, so CMs can potentially get the wrong data. Companies need to track customer data for maintenance purposes, which brings another dimension of complexity.
As organizations grow and their data volume increases, scalability becomes a concern. Traditional data management approaches may struggle to handle the expanding data requirements. Relying on files, folders, cloud and network storage and spreadsheets is a bad idea. Relying on multiple PDM systems can solve the problem partially, but won’t provide a solution for a growing digital thread of information.
Data Quality:
The first outcome of data silos is poor data quality. Data defined in multiple places (eg. file, spec, cost, supplier info, revision of changes) cannot be validated, so it resulted in companies’ inability to trust the data. An attempt to figure out what was included in the released materials for rev5 of a specific design and what was sent to a contractor leads to mistakes, increased cost, and frustration.
Inaccurate or incomplete data can lead to costly errors in product design and manufacturing processes. Ensuring data accuracy and completeness is a significant challenge, especially when data is generated from various sources. Companies are not focusing on establishing a single source change to guarantee the data architecture to support distributed engineering teams and trust in data.
Single Source of Changes and Version Control:
Change is the only constant in engineering and manufacturing. Projects often involve multiple iterations and versions of designs and documents. The absence of scalable data management systems allowing to capture revisions and changes leads to a headache, confusion, and potential errors if the wrong version is used. It is a big pain of product data management with poorly organized data.
What is lacking in all modern data management scenarios is the ability to control data records, data ownership, and change management rights. When data is shared, companies lack a mechanism to trust who and when can make a change and how to consolidate these changes together.
Data Access and Collaboration:
A painful outcome of data silos and not organized data is that data cannot be accessed at the time when it is needed by everyone (engineers, procurement planners, production and operation, customers). Users are looking to get access to the right data when they need it. The absence of seamless access to design information (eg. CAD files), bill of materials, order records, and planning can bring the manufacturing process to a full stop. Sending Excel via email leads to bad collaboration capabilities.
Therefore, collaboration is essential in engineering and manufacturing, but facilitating seamless data access and collaboration among teams, including remote workers, is challenging and I can see many companies suffering to establish centralized data access and to provide collaborative tools to all users.
Data Security:
Engineering and manufacturing IP is the most important thing that exists in the manufacturing business. Information about design, production methods, suppliers, and costs is essential for business. Competitors will be looking for how to get this information.
The sensitive nature of engineering and manufacturing data, including proprietary designs and intellectual property, demands robust security measures. Protecting data from unauthorized access, cyberattacks, and data breaches is a constant concern for organizations in these sectors.
Looking at unlocked desktop computers, blueprints, and BOM prints located everywhere and sometimes placed in trash cans, working with computers without antivirus software, use of private email and cloud data sharing accounts. This is just a short list of problems that can lead to data breaches. Companies are still talking about the risks of the cloud software, but using the same simple password on all devices.
Compliance and Regulations:
Engineering and manufacturing industries are subject to numerous regulations and standards, such as ISO, FDA, and environmental compliance. Ensuring that data and processes align with these regulations is a complex task. The risk of not following the regulation and missing some critical aspects of compliance is a big problem for engineering and executive management. Not having historical records of the BOMs and supplier information can bring executives to jail when a product fails and customers’ lives and health are in danger. Very often, companies are struggling to bring a historical record of a BOM that was used for manufacturing a specific product revision.
What is a Possible Solution?
Here are a few ideas to overcome the problems I mentioned above.
- Implement a centralized data and file repository and adopt data integration tools to break down silos and ensure data consistency and accessibility across the organization.
- Adopt version control systems and document management software to track changes, maintain a history of revisions, and ensure that the most current data is always accessible.
- Invest in collaboration tools, cloud-based platforms, and remote access solutions to enable real-time collaboration and data sharing among teams, regardless of their location.
- Employ encryption, access controls, and regular security audits to safeguard critical data assets. Training employees on cybersecurity best practices is also crucial.
OpenBOM is a robust data management and collaboration platform that can be used as PLM software to manage product information, interoperate with enterprise resource planning and computer aid design software to ensure all data is under control, history of changes is managed and everyone has access to the right data at the right time.
Conclusion:
Can you see some of the patterns of pains and challenges described above in your organization? Are you struggling to bridge the gaps in how to organize data management and collaboration? Do you need help to integrate all your existing tools together? OpenBOM can help you. Education is the first step in our journey. Understandng of the problem put you half way towards the solution.
Effective engineering and manufacturing data management are critical for achieving efficiency, innovation, and compliance. By addressing these seven common pains and implementing the suggested solutions, organizations can navigate the challenges of data management in these industries and drive their success in an increasingly data-driven world.
REGISTER FOR FREE and check how OpenBOM can help.
Best, Oleg
Join our newsletter to receive a weekly portion of news, articles, and tips about OpenBOM and our community.