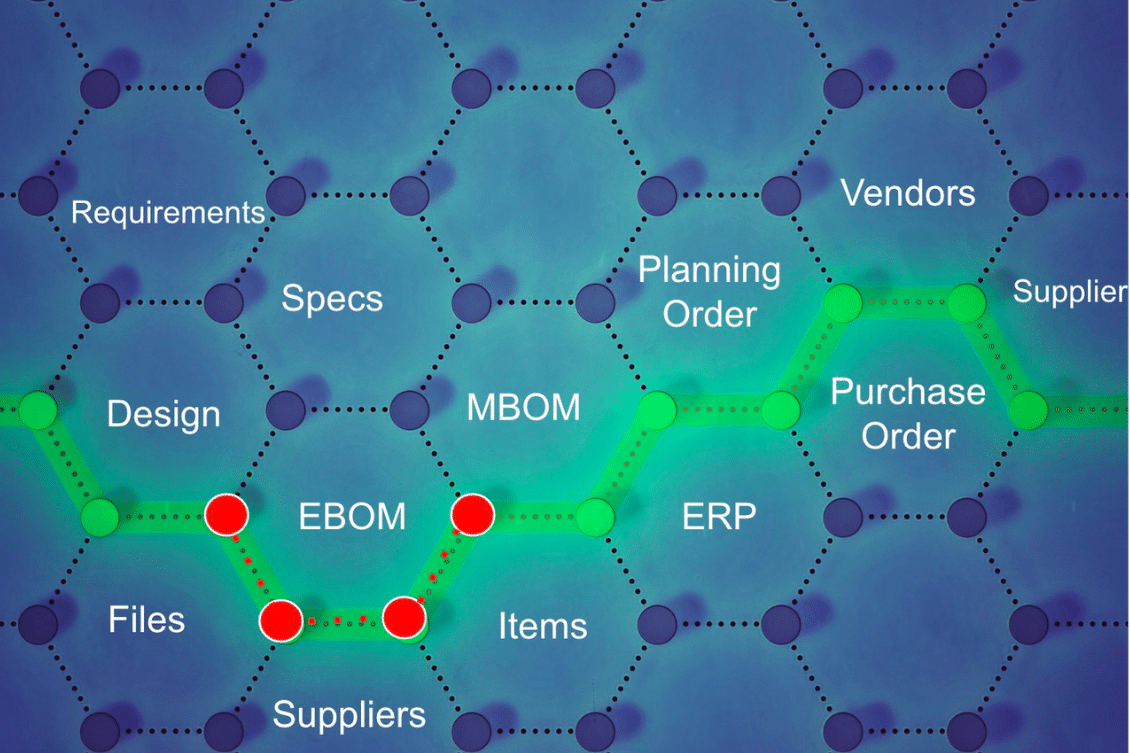
In our modern, interconnected world, communication and collaboration have become essential for the success of engineering and manufacturing organizations. The ability to access information when you need it, collaborate seamlessly with colleagues, and efficiently share data across different applications is no longer a nice-to-have but a fundamental requirement.
In this article, we will explore the challenges and pains of collaboration in engineering and manufacturing organizations, highlighting the importance of staying connected, the complexities of working on up-to-date product information, the need for flexibility, and the demand for automated data extraction.
Talking to many engineering teams and manufacturing companies, we found a typical waterfall process happening during the product development process. It is extremely inefficient and painful. Not only it blocks people from accessing accurate data, but it also slows down the development process.
The Need for Real-Time Information
It is 2024 already, but the reality of many engineering environments is to work with files. This is because design and engineering data are heavily siloed. The reality of the engineering environment is multiple design systems (eg. MCAD, ECAD, etc.) that save their data using files located somewhere on the disc (or network drive). At its best, the design files go to some cloud location (eg. Dropbox, OneDrive, etc.) All these files are not synchronized and it is very hard to bring everyone “on the same page”. Each CAD system has its own revision control (PDM) and, as a result, you’re getting a lot of information saved in different places.
Moving downstream, the information is often extracted from CAD files and saved in Excel (in the best case, using online spreadsheet applications) and files are exported elsewhere. The connection between all these pieces of information is not managed well. The data moves between engineers and later downstream with large delays, which causes huge inefficiency.
Imagine a scenario where you’re working on a tight deadline, and you need specific files or information from a contractor or a colleague in a different location. Waiting for hours, or even days, for these files to be synchronized between databases or servers can be exasperating. Inefficiencies caused by delayed data access can result in wasted time, resources, and, ultimately, money.
In today’s fast-paced engineering and manufacturing environments, staying connected is no longer an option; it’s a necessity. People demand instant access to critical information right here, right now. When a team member requires a drawing or a STEP file from the engineering department, waiting is simply not an option. Delays in accessing essential data can lead to project setbacks, missed deadlines, and increased costs.
Collaboration on Complex Products
The nature of engineering and manufacturing often involves collaboration between multiple engineers with different areas of expertise. Complex products, such as electronic assemblies or mechanical systems, require input from various team members, including designers, electrical engineers, and mechanical engineers. Waiting for one team member’s contribution can lead to frustrating delays and increased costs.
The reality of many existing engineering environments is that all these engineers working on different systems, sub-systems, and components have a hard time communicating and collaborating together. To view information in the context of the up-to-date files is a challenge. To have up-to-date information for design review is hard because data is locked in different folders, servers, or systems.
Consider the situation where a printed circuit board (PCB) designer is tasked with providing crucial details about board sizes and shapes. Waiting for this information can cost precious hours, and in some cases, can lead to design errors and rework, further increasing project expenses.
The demand of engineering teams is to have a consolidated view of mechanical, electrical, electronics, and software information aligned with the same revision control and a path to extract and share data in a seamless way. This brings me to the next pain – manual data extraction.
Automated Data Extraction
In the digital age, the sheer volume of data can be overwhelming. Getting the necessary data from multiple applications, be it components for a PCB board or information for a mechanical assembly, can be a time-consuming and error-prone process if done manually. Organizations cannot afford to spend an entire day gathering and inputting data from different sources.
The reality of engineers running scripts using their desktop CAD system overnight to get PDF or STEP files and then storing them in some folders – is a recipe for disaster in the future design review, procurement, production planning, and integration.
Automated data extraction is becoming increasingly important in engineering and manufacturing. Leveraging technology to automatically collect and integrate data from various software applications can significantly improve efficiency and accuracy. By reducing manual data entry and retrieval, organizations can save time and reduce the risk of errors in their projects.
The Importance of Flexibility
Every engineering and manufacturing company operates differently, with unique processes, workflows, and data requirements. Rigid data properties and information fields can hinder collaboration in such diverse environments. This is why flexibility is a key requirement for effective collaboration.
Many professionals in these fields turn to tools like Microsoft Excel because of their adaptability. Excel allows users to create custom templates, manipulate data in various ways, and collaborate with others easily. Its flexibility in handling diverse data types and formats makes it a preferred choice for many engineers and manufacturers.
Once companies start with Excel or any alternative spreadsheets, it is just a matter of time, the data communication and collaboration will become a nightmare. Think about multiple spreadsheets not managing a single record about an item. It means you have a duplicated record and are not able to check what is the real information. Then things get even worse. Files and spreadsheets cannot live together well. So, files and Excels are stored in the same place, but cannot be technically connected in any way.
The demand of engineering teams and manufacturing companies for product lifecycle management systems is to adapt data models for specific product data management requirements. In such a way the PLM environment must be flexible from both data and development process standpoints. Together it must be adjusted to specific business processes that are good for this specific company.
Conclusion
In the modern engineering and manufacturing environment, staying connected, making information immediately available, and automating data extraction from multiple applications are critical factors for success. The pains of collaboration, such as waiting for essential data, dealing with complex product collaborations, struggling with inflexible data structures, and manually extracting information, can be alleviated with the right tools and technologies.
The pains of inefficient communication, segregated engineering and design processes and inability to find the last (or a specific) revision of information are gigantic. Manufacturing businesses cannot communicate effectively and manage product life cycles in a continuous and connected way. To have face-to-face communication is not possible in many situations in the modern world. Therefore having information connecting people is essential.
Engineering and manufacturing organizations must invest in product lifecycle management solutions and software tools that enable flexible data management and real-time access to data, promote seamless collaboration among team members, provide flexibility in data handling, and offer automation capabilities. Embracing these principles will not only reduce the pains of collaboration but also improve productivity, improve product quality, reduce costs, and ultimately support business transformation leading to more successful projects in this ever-evolving industry. That’s the PLM software of the future.
REGISTER FOR FREE to check how OpenBOM can help you improve collaboration and communication between engineers, contractors, suppliers, and production teams.
Best, Oleg
Join our newsletter to receive a weekly portion of news, articles, and tips about OpenBOM and our community.