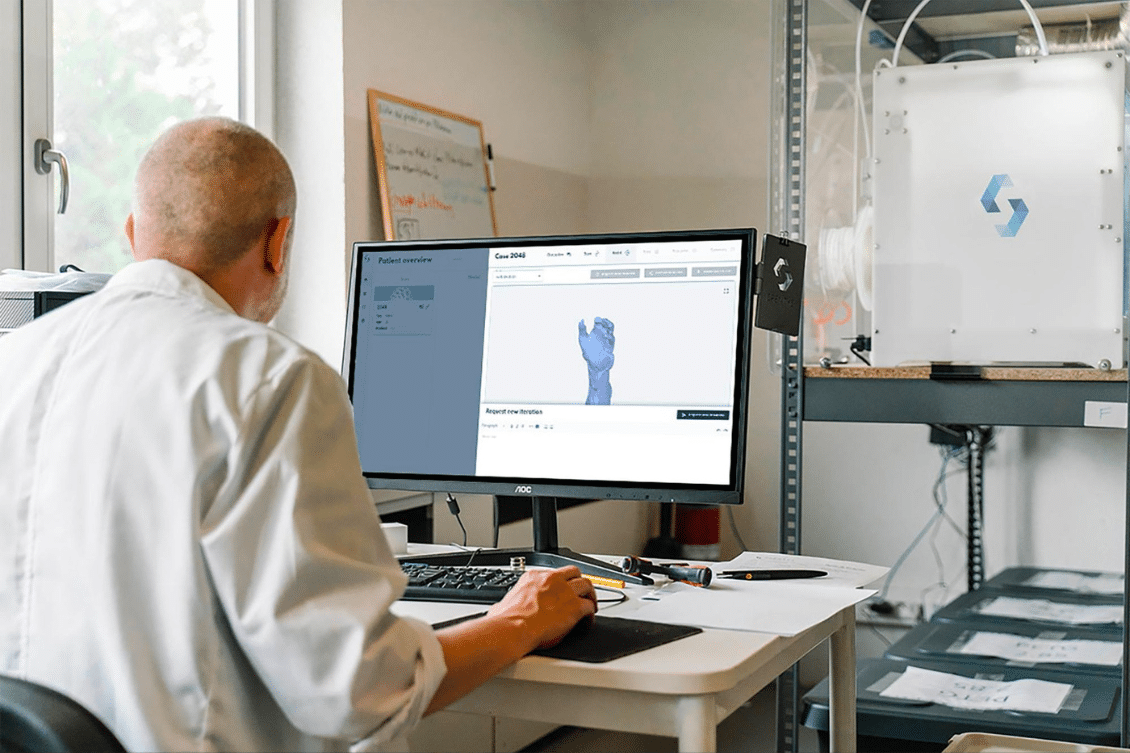
In today’s interconnected business landscape, collaboration between manufacturers and their suppliers is paramount to achieving efficient and successful product development. Sharing data with your supplier during the development process is a crucial aspect of this collaboration, enabling both parties to align their efforts, make informed decisions, and ultimately deliver high-quality products to the market.
Effective data sharing ensures that suppliers have the necessary information to meet your specific requirements and contribute their expertise to the development process. It facilitates seamless communication, minimizes errors and misunderstandings, and promotes transparency and trust between you and your supplier.
However, sharing data with your supplier is not without challenges. Concerns about intellectual property, data security, and confidentiality may arise. It is essential to establish clear guidelines, establish proper protocols, and utilize secure channels to safeguard sensitive information while fostering collaboration.
In this post, we will explore how to best share data with your supplier in modern manufacturing. We will discuss strategies for effective communication, data protection measures, and the tools and technologies that can facilitate smooth data exchange. By following these recommendations, you can foster a productive partnership with your supplier and drive successful product development outcomes.
The Traditional Way of Sharing
The traditional way of sharing product data with suppliers often involved using tools like Excel. Manufacturers would compile product information, specifications, and other relevant data into Excel files and send them to their suppliers via email or file-sharing platforms.
The risk of the traditional way of sharing data through Excel is the creation of data silos. This leads to each department having its own data which might not be consistent with other departments.
Where the Traditional Way of Sharing Fails
The traditional method of sharing data and managing information using Excel files has been widely accepted as the norm. However, despite its advantages, there are several limitations and risks associated with using Excel for data sharing, such as:
- No integrations with CAD systems
- No single source of truth or centralized system
- No automatic sharing
- Create data silos
Modern Way to Share Data During Development
The modern way of sharing data during development leverages digital tools to enable collaboration and efficient information sharing. Manufacturers who embrace digital transformation during development can establish better partnerships with their suppliers, accelerate the development processes and deliver a superior product.
During the development process, digital transformation can help you with the following:
Transitions you to RFQ
Utilizing digital transformation will create a single source of truth for all of your product and manufacturing data. As a result, it will simplify the request for quotation (RFQ) process.
Excel lacks the capability to capture and organize all the intricate details associated with your product. This limitation hampers the RFQ process, leading to delays and inefficiencies in sourcing suppliers and obtaining accurate quotes.
In contrast, moving to the digital thread serves as a centralized repository that stores all the data generated throughout the product development process. This comprehensive and structured collection of information can be easily shared with suppliers to request quotes for specific parts or products. By leveraging this, manufacturers can provide suppliers with a holistic view of the product, ensuring that all necessary information is readily available for quoting purposes.
Tracks History
During the lifecycle of your product, tracking historical data is crucial for effective management. It is essential to have a record of important milestones, such as shipment dates and revisions, to ensure transparency and facilitate decision-making.
Relying solely on spreadsheets for tracking this information presents significant limitations. Spreadsheets lack visibility into the changes and milestones associated with your product. As a result, you may find yourself spending hours sifting through emails and various documents in search of critical data.
To streamline the development process and achieve a successful product launch, it becomes imperative to keep your product information up-to-date. This includes maintaining accurate records of revisions, shipping dates, and other pertinent details. By doing so, you gain better visibility, improve collaboration, and ensure that all stakeholders are working with the most current and relevant information.
To overcome these challenges and ensure efficient data management, adopting specialized software solutions and digital platforms can greatly enhance your ability to track and update product information. These tools provide a centralized repository where you can easily access, update, and retrieve historical data, allowing for streamlined collaboration and informed decision-making throughout the product lifecycle.
Enables Collaboration
In the development steps, a frequent concern arises: Are we working on the same data? Unfortunately, it is not uncommon for teams to discover that they have been working with incorrect or outdated product data, leading to wasted time and extensive rework.
Effective collaboration becomes nearly impossible when different teams are operating on different sets of data. The absence of a unified platform for storing and accessing the latest product information hinders communication and coordination among team members.
To enable seamless collaboration, it is crucial to establish a shared platform that can be utilized by everyone involved. This doesn’t necessarily mean that all team members need to use the same CAD system or business tools. However, they should have access to a common repository where the most up-to-date product information is stored.
By implementing such a platform, teams can ensure that they are working with synchronized data, eliminating the risk of discrepancies and enabling effective collaboration. It provides a central source of truth for product information, facilitating streamlined communication, reducing errors, and ultimately driving efficiency and productivity throughout the development and production processes.
ECO Process
A significant problem during development with your supplier is that your supplier releases a change for production or tooling assuming their change request was correct. This is common without a clear process of how to approve a change request.
By utilizing digital transformation, manufacturers can create a structured process for evaluating and approving change requests. Each proposed change can be systematically reviewed, considering factors such as cost implications, quality enhancements, and overall impact on the product.
Implementing an approval system for change management not only promotes governance and control but also helps prevent unnecessary delays and financial burdens. It enables manufacturers to maintain a streamlined product development process while ensuring that each modification aligns with the desired objectives and brings value to the final product.
By leveraging digital tools and utilizing a structured approval process, manufacturers can effectively manage changes, minimize risks, and optimize the product development journey.
What to do Today
Companies are looking at ways to improve their overall competitiveness. Which is great. However, the tools companies use need to also support your goals. You can’t continue to use Excel and expect to improve your speed from development to production.
Digital transformation will help you to transform your processes and help you share data with your supplier during development. To have a centralized platform that connects your team with your contractors is extremely important to set up modern digital processes to save time and money.
OpenBOM is a cloud-based PDM & PLM platform to manage your engineering and manufacturing data. Companies from startups to Fortune 500s use OpenBOM to create a centralized database to bring in, store, and manage their manufacturing data. With this infrastructure, users also use OpenBOM to streamline both their change management and PO processes.
If you need to improve the way you manage your data and processes, share data instantly, or collaborate with contractors and suppliers, Contact us today for a free consultation.
Regards,
Jared Haw
Join our newsletter to receive a weekly portion of news, articles, and tips about OpenBOM and our community.