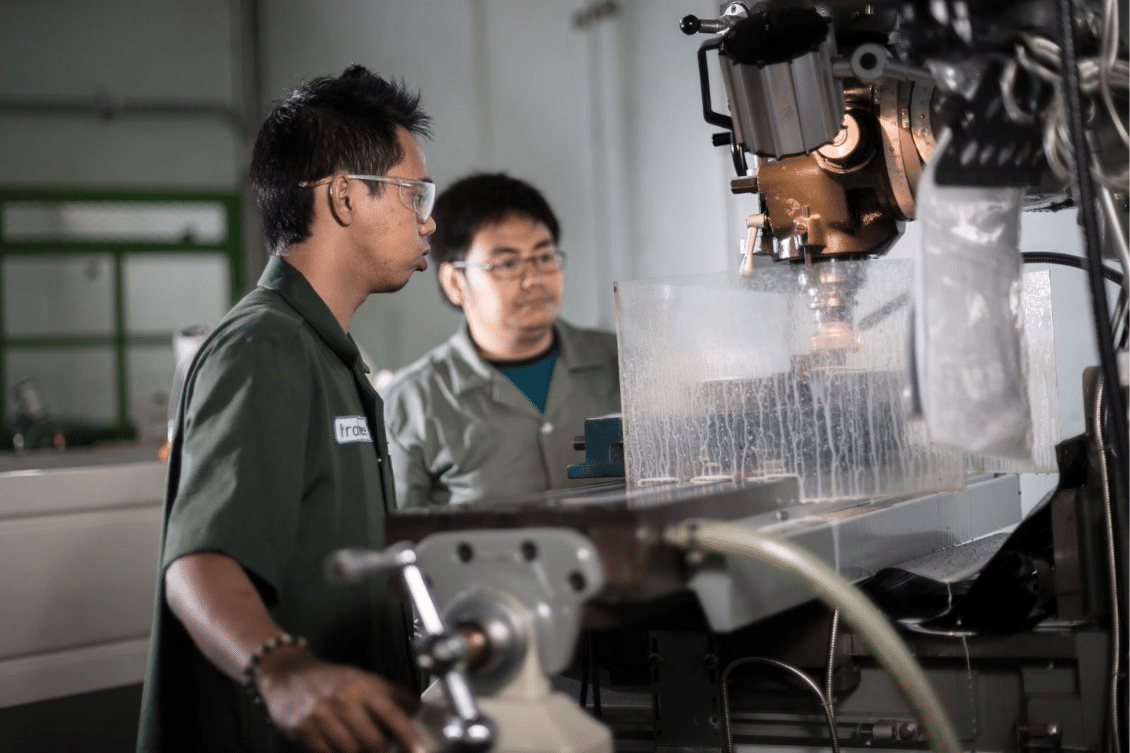
With technologies shaping industries, companies are forced to adopt new technologies in order to keep up with their competitors. One industry that is vulnerable to these digital changes is machine shops.
COVID has introduced a number of additional challenges that have been piling on these shops. These include added complexities to the supply chain, part inflation, parts going obsolete, employee turnover, and more. To cope with these additional challenges, machine shops have had to adopt new technologies and automation.
This is where the concept of digital transformation starts to take shape. Digital transformation, which is often issued for larger companies is just as relevant, for smaller machine shops. In order for machine shops to continue to stay competitive, they need to find out ways to stay competitive.
In this blog, we are going to cover how machine shops will benefit from digital transformation. We will go over digital transformation, the challenges faced by these machine shops and how digitizing their processes can give them the support they need.
Understanding Digital Transformation
While the tools of digital transformation seem complex and a buzzword followed by larger companies, the goal of digital transformation should be simple to understand. The goal of digital transformation is to help you to make smarter better decisions with accurate data.
As a result, the customer experience will be improved by reducing barriers through the development, purchasing, and production processes.
Challenges Faced by Machine Shops
Machine shops, like any other business, face various challenges that can impact their operations and success. Here are five top issues that machine shops commonly encounter:
Skilled Labor Shortage
Finding and retaining skilled machinists, technicians, and operators can be a significant challenge. The manufacturing industry as a whole has been experiencing a shortage of skilled workers, and machine shops are no exception. As older workers retire, there’s a gap in expertise that needs to be filled with new talent. This shortage can lead to increased labor costs, longer lead times, and potential quality issues.
A lot of machine shops also depend on tribal knowledge which is unwritten and informal knowledge that employees accumulate through their experience on the job. It’s a valuable resource, but it can also pose challenges, especially when it’s not documented.
Rapid Technological Advancements
Rapid technological advancements have introduced a new era of possibilities, promising increased efficiency, precision, and innovation. However, this wave of progress comes with its own set of challenges that machine shops must navigate.
Supply Chain Disruptions
Machine shops heavily rely on a complex network of suppliers for raw materials, tooling, and components. Disruptions in the supply chain, such as material shortages, political policies, or transportation issues, can lead to production delays, increased costs, and customer dissatisfaction. The COVID-19 pandemic highlighted the vulnerability of supply chains and emphasized the need for diversification and resilience.
Quality Control and Consistency
Maintaining consistent quality across a range of products can be challenging, especially as customer demands become more complex. Machine shops need detailed quality control processes to ensure that each part meets specifications. Any deviations or defects can lead to rework, scrap, and customer dissatisfaction, ultimately impacting the bottom line.
Cost Management and Pricing Pressure
Cost management is a perpetual concern in the manufacturing industry. Fluctuations in material prices, energy costs, and overhead expenses can strain profitability. Additionally, machine shops often face pricing pressure from customers who are looking for competitive rates. Striking a balance between offering competitive prices and maintaining healthy profit margins can be a delicate task.
Benefits of Digitalizing Your Processes
Digitalizing processes in a machine shop can bring several benefits that can enhance efficiency, productivity, and competitiveness. Here are the top benefits:
Improved Operational Efficiency
By digitalizing processes, machine shops can streamline workflows and reduce manual intervention. Automation of tasks such as data entry, job scheduling, and quality checks can significantly reduce the time and effort required for routine operations. This efficiency boost leads to faster production cycles, reduced lead times, and increased throughput.
Improved Product Quality
Digitalization enables tighter control over processes, leading to improved product quality. With real-time data collection and analysis, machine shops can identify deviations from standards and make necessary adjustments promptly. This minimizes defects, reduces rework, and ensures that each product meets or exceeds specifications.
Data-Driven Decision Making
Digitalized processes generate loads of data that can be leveraged for informed decision-making. Machine shops can gather insights into equipment performance, resource utilization, and production trends. This data-driven approach allows managers to identify bottlenecks, optimize processes, and allocate resources more effectively.
Flexibility and Adaptability
Digitalized processes provide machine shops with the agility to adapt to changing market demands and customer preferences. Rapid adjustments to production schedules, quick customization of products, and the ability to respond swiftly to unforeseen disruptions become possible. This adaptability ensures that machine shops remain competitive in a dynamic market.
Compliance and Documentation:
Digitalized processes can aid in compliance with industry regulations and quality standards. Documentation of processes, data logs, and production history becomes more accurate and accessible, facilitating audits and certifications.
Innovation and Continuous Improvement
The data-driven insights gained from digitalization can spark innovation and continuous improvement efforts. By analyzing trends and performance metrics, machine shops can identify areas for innovation and invest in research and development to stay ahead of market trends.
The First Step to Digitalize Your Processes
Changing the way you manage your data is hard. For machine shops, this usually means moving away from Excel to a new way of managing information. This can not be done overnight.
The first step is always to develop a transition plan. Companies are usually skeptical to change and it’s important that engineers have the aha moment of how the digital processes can improve the business.
A full-blown change to a machine shop might also bring unintended consequences. However, if you bring change gradually by changing existing data management processes then all the teams will start to see the benefits that going digital can bring.
For many machine shops, this means trading Excel files for a data-centric strategy. In a data-centric approach, the focus of the system moves from the organization of documents to the definition of granular data sets describing data and processes, connecting people to the right information, and organization of seamless information flows.
Instead of disparate CAD files and Excel spreadsheets, a data-centric strategy allows manufacturers to create information only once, to share it between multiple people, departments, and organizations.
The goal of this and creating a digital BOM is to replace all the Excel BOMs, break down the different data silos, and get all the tribal knowledge onto a single system.
What can you do Today?
Moving towards digital processes takes time and planning. However, not all of the steps need to be executed at the same time. Starting with a data-centric approach and replacing messy Excel would be the first step.
OpenBOM is a cloud-based PDM & PLM platform to manage your engineering and manufacturing data. Companies from startups to Fortune 500’s use OpenBOM to create a centralized database to bring in, store, and manage their manufacturing data. With this infrastructure, users also use OpenBOM to streamline both their change management and PO processes.
If you need to improve the way you manage your data and processes, share data instantly or collaborate with contractors and suppliers, contact us today for a free consultation.
Regards,
Jared Haw
Join our newsletter to receive a weekly portion of news, articles, and tips about OpenBOM and our community.