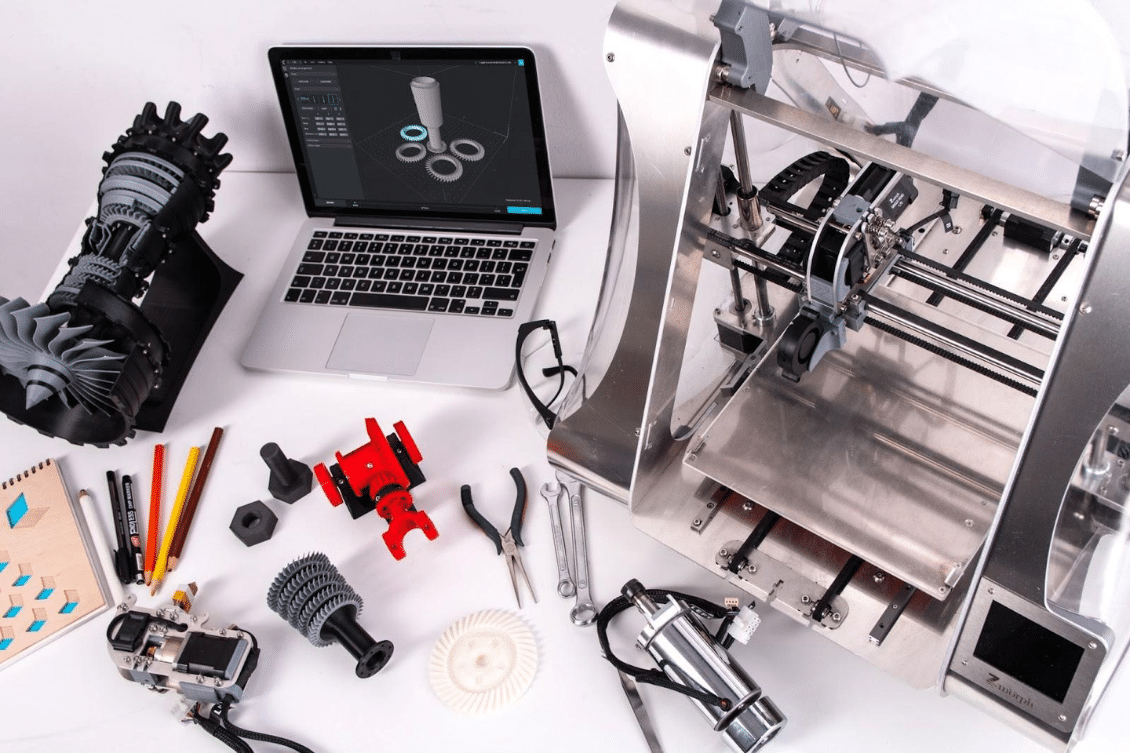
Manufacturers have always been looking for ways to gain a competitive advantage. In the past, they have looked to hire the best talent, develop the best partners, launch a campaign for pre-sales, and more. In recent years, manufacturers are looking at ways to optimize their processes to support all of these relationships they have. The process they look to optimize is how they enable collaboration.
As manufacturers mature, they have noticed the importance of collaboration. You might have the best talent and partners but if there is nothing connecting them then you will still not be able to gain a competitive advantage.
Manufacturers are becoming more aware that enabling collaboration provides them with a competitive advantage. However, collaboration only works if you create a single source of truth. Having everyone use their own systems and share data using spreadsheets will create data silos. Your goal of collaboration should be to eliminate data silos and create a single source of truth.
The best place to start would be to look at the document that holds your product knowledge. This document usually is known as the bill of materials (BOM). In today’s post, we will look at why digitalizing your BOM during development and manufacturing is the best way for you to enable collaboration.
What is a Digital BOM?
As you might know, the BOM is a full list of items required to build your product. Without a detailed BOM, you will have an inconsistent product that can vary with each order.
It is common for manufacturers to manage their BOM using Excel or spreadsheets. This is where you start to make mistakes. Here are common issues manufacturers have noticed with using Excel or spreadsheets to manage their BOM:
- Purchase incorrect parts or quantities
- Not sure of the correct revision
- Not able to automatically share
- No approval process for change requests
- Creates separated data silos
- Can’t roll up costs
- Can’t properly manage your product structure
- No CAD integrations.
The purpose of a digital BOM is to improve the way you communicate and work with other team members and contractors. A digital BOM connects you with your team and contractors while also creating a single source of truth. The digital BOM is also a step towards moving to digital transformation.
A digital BOM will provide the following:
- A centralized source of information for all items
- Managed records of BOMs, revisions, and changes
- Real-time data sharing
Why a Digital BOM Helps During Development and Manufacturing?
When you are developing a product, there are most likely multiple people involved in development. However, it is common for these different people to be working on different sub-assemblies which usually means they work with different systems. Even internal teams can be working with two different CAD systems and manage those CAD files in different ways. Nothing is connected.
During design for manufacturing (DFM) you might be working with a contract manufacturer on the opposite side of the world. Sending CAD files and spreadsheets back and forth is tedious. A digital BOM will keep all of these stakeholders connected.
Creating a digital BOM will improve your efficiency on the product development and manufacturing side in a few ways.
Tracks History
During the lifecycle of your product, it is important to track historical data. You will need to know when a product was shipped, the day a revision was made, and more.
A spreadsheet provides no visibility into these changes or milestones. You are left spending hours going through emails trying to find important data.
If you are developing a product then it’s important to keep that product information up-to-date so you can streamline to a successful product launch.
Change Management
There is nothing like a contractor or team member making an unauthorized change. We have heard countless times of production partners doing this. Usually, it’s with good intentions to either cut costs or improve quality. However, failing to have an approval process extends the product development process and also adds up financially.
If you are developing a product then each change should add value to a component or sub-assembly. Also, each change should be thoroughly analyzed. Having a digital BOM is the first step to creating an approval system for all changes.
Enables Collaboration
A common question asked during development and production is if we are working on the same data. Sadly, all of us have been working on the wrong product data at one time. You spend countless hours with no end result, just re-work.
How can you collaborate when you are working on different data?
You can’t…
If you are looking to enable collaboration then you need a platform everyone can use. It does not mean that everyone needs to use the same CAD system but it should be a common place to store the latest state for all product information.
Transitions you to RFQ
The last reason why it’s important for companies to use a digital BOM is that it’s a great transition to the request for quotation (RFQ) process.
The biggest struggle of the RFQ process is to find all of the product information about the product. You need to find part specifications, CAD models/STEP files, quality requirements, work instructions, and so on. Excel does not have the ability to capture all of this product information.
A digital BOM will be able to store all of the data created during the product development process and easily transfer it to a supplier to quote a specific part or product.
What can you do Today?
If you are looking to improve your development and manufacturing process then you should look into a digital BOM. A digital BOM will keep all of your product data together and manage your revisions and create a change request process. Your solution is a centralized platform that connects your team, contractors, and suppliers.
OpenBOM is a cloud-based PDM & PLM platform to manage your engineering and manufacturing data. Companies from startups to Fortune 500’s use OpenBOM to create a centralized database to bring in, store, and manage their manufacturing data. With this infrastructure, users also use OpenBOM to streamline both their change management and PO processes.
If you need to improve the way you manage your data and processes, contact us today for a free consultation.
Regards,
Jared Haw
Join our newsletter to receive a weekly portion of news, articles, and tips about OpenBOM and our community.