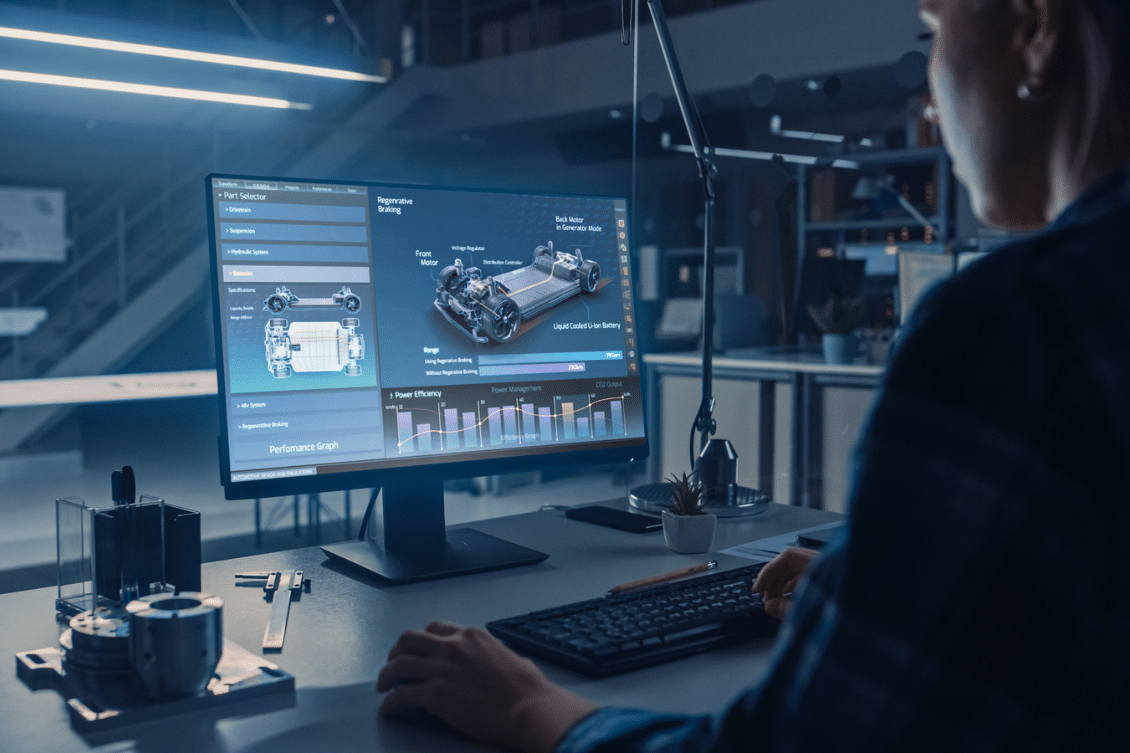
In today’s manufacturing, product data management has become increasingly complex due to the great amount of data and dependencies. Products are becoming complex and include mechanical, electronic, and software components. People are working in different places and companies. Product is often built by different companies located in various places in the world.
The complexity of this data can create significant challenges for manufacturers, including data duplication, errors, and inconsistencies, leading to production delays and quality issues.
In this blog post, we will explore the complexities of product data in manufacturing organizations and the challenges they face in managing this data. I will speak about the limits of traditional data management and document lifecycle. Also, I will talk about best practices for managing data and moving from documents to data, which can change the way information is managed.
Why Document Management Over The Wall Manufacturing Has Its Limits
Life was simple back 20+ years ago when everything company was managing its files from one of the design systems (CAD). Those potentially were files coming from the CAD systems used by the company (eg. MCAD or ECAD). The need to manage CAD files created a foundation of engineering data management (earlier called EDM) and the growing capabilities of PDM systems to manage documents (CAD), share CAD files between multiple engineers, and release them once the desired level of maturity was achieved.
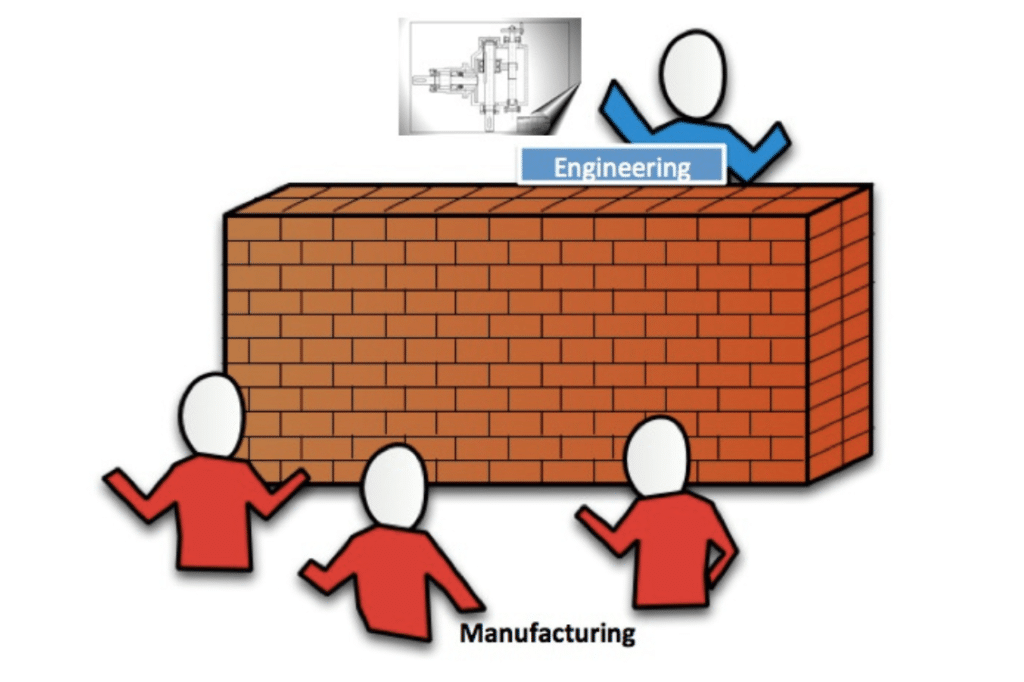
Later, the so-called “over the wall” manufacturing process was happening and companies magically were creating a BOM (typically located and managed by MRPII systems). I described it in my earlier Beyond PLM blog – End of Over The Wall Engineering To Manufacturing Process. The process of such an approach is largely related to the absence of ways to manage information in a granular form to support the growing complexity of design and manufacturing processes.
4 Phases Of Product Lifecycle
Products are getting increasingly more complex these days. The product lifecycle is a model that describes the different stages that a product goes through from its inception to its retirement. The four main stages of the product lifecycle are engineering, production, sales, and maintenance.
- Design and Engineering: The first stage of the product lifecycle is engineering. In this stage, product engineers work to design and develop the product, including researching and testing new technologies, creating prototypes, and refining the product design.
- Manufacturing: The production stage is when the product is manufactured on a larger scale. This stage involves setting up a production line, sourcing materials and equipment, and optimizing the manufacturing process to ensure that the product can be produced efficiently and cost-effectively.
- Sales: The sales stage involves marketing and promoting the product to potential customers. This includes creating advertising campaigns, establishing sales channels, and conducting market research to identify customer needs and preferences.
- Maintenance: The maintenance stage involves providing ongoing support for the product, including fixing any issues that arise, releasing updates and new versions, and providing customer service to address any questions or concerns. This stage is critical for maintaining customer satisfaction and ensuring the long-term success of the product.
As you can see these fundamental elements of product lifecycle management activities must rely on their data representation and support the processes. At the same time, an attempt to serve such a complex process using a single document management process is not realistic.
As a result, companies are struggling to organize documents to support complex activities, scratching their heads and jumping through the hoops of PDM limitations, inventing collaborative workspaces, multiple vaults (engineering and release), and routing documents for approvals and signatures. The document management process was good once it was a simple way to organize CAD documents in a small team, but these days it is simply not enough to manage the complexity of data.
Setting Up A Minimum Viable Product Lifecycle Process
At OpenBOM, we focus on how to provide an easy and flexible data management platform to support a complete product development process. But simplicity is key. The starting product data model is simplified to support the following object types:
- Design Version
- Item and BOM Revision
- Planning & Orders
These three elements of product information provide the desired level of granularity and allow you to escape limitations in CAD document management. Here is how it works.
The design version process (Drive) is focusing on how to manage design data and changes. the foundation is CAD data (files or cloud data). The Drive holds files, allows you to share them for concurrent usage, and manages versions of the design.
Item and BOM revisions are a core of the engineering data model (EBOM) managing a complete product structure with all connected information and managing structures, revisions, and change processes such as ECO.
Planning & Orders support manufacturing activity focused on getting all components and assemblies built and delivered for the assembly line. The focus of this process is to provide minimum MBOM functions (for procurement planning).
OpenBOM’s flexible and customizable data model allows the management of the following 3 object types with all related information, to customize attributes and metadata, and support collaborative activities between multiple teams and individuals. The focus of these 3 elements is to support a granular mechanism to manage product information and remove the limits of CAD documents to manage the product lifecycle.
Conclusion:
Product development is hard. It is impossible to support the development of complex products by using CAD document management systems. The usage of CAD vault is good for the design lifecycle, but not allowing to connect multiple data elements and processes needed to manage the simplest possible product lifecycle management process. In the coming days, we will share more details about each step and demo how to use it for simple product lifecycle activities.
REGISTER FOR FREE and start a trial to check how OpenBOM can help.
Best, Oleg
Join our newsletter to receive a weekly portion of news, articles, and tips about OpenBOM and our community.