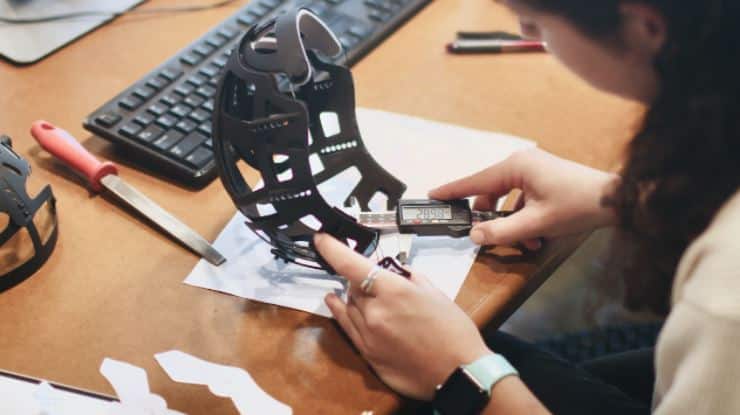
The steps to verify and choose your contract manufacturer (CM) are very important to lay the foundation of your relationship. However, selecting the right contract-manufacturing partner is only an intermediary step in building long-term success. The proceeding steps and results are what build the long-term relationship.
Just like any business or personal relationship, you must first understand the goals of the other person or company. You need to make sure that you will be able to support them to achieve their goal. And for different companies, this means different things.
CM’s come in all different sizes, structures, and business models. You need to find the CM that can support you to achieve your product and manufacturing goals. To achieve these goals, there are a few different processes to think about.
Handoff: Providing the necessary manufacturing documents
The handover process should really have started in the previous stage. This is when you provide your CM with the RFQ package which contains the knowledge of your product. This includes the BOM, drawings, quantity, specifications and the assembly and quality requirements. Your CM will take this information and provide you with a quote.
When we quote projects (and when most CM’s quote projects), we often find certain in-efficiencies and problems with the current design. When we provide a quote, we also provide feedback on how certain parts of the overall product can be improved. These usually consist of:
- Optimizing parts for tooling
- Altering processes or materials to reduce scrap rate
- Suggesting alternative components to improve parts with longer lead times.
- Proposing changes to keep desired tolerances.
As you can see, there can be multiple issues that come out after the handoff period. The next steps of how you solve these problems depend on the capabilities of the CM and of your in-house engineering and manufacturing teams.
ECO Process: Design & DFM Changes
Many of the problems listed above have to do with design and engineering. However, you and your company do not need to be experts with everything. When issues, like the bullet points above, come up, clear communication between you and your CM will be necessary.
Remember, this is your product but you welcome suggestions of how to improve it. This is how you should work with your CM. If they have an idea of how to decrease your price, optimize the part for tooling, or anything else, you should listen to them. But again, this is your product so you will need to provide the final OK and agree to the changes.
When we suggest how to optimize a part, it’s just that, it is a suggestion. However, if the client accepts this proposed change, we carry out the change in-house and provide the client with the most updated drawing and BOM. A prototype can be made to confirm the validity of the design, as well.
I would always recommend this approach. Let your CM make suggestions and ask for them to carry out any changes once approved. But how about managing this info and data that has been suggested and carried out?
Managing the BOM and Data
After the changes are made and confirmed, organizing the data is another chore. The goal is to have your team, contractors, and CM all on the same BOM and with the most updated part spec and drawings. Managing and distributing this info is what leads to communication breakdowns and confusion of who has the most updated BOMs. This is when we get into constantly resending emails and files.
Deciding who is responsible for managing this data depends on the trust you have with your CM and how large your team and outside support is. Some CMs are fantastic, they have great project management teams or software which support them to manage this. While others prefer not to take on this responsibility.
On the CM side, I have always preferred to take responsibility for managing the manufacturing data. My logic was that since we are making it, we should manage it.
However, sometimes, our client is working with outside contractors and needs to manage the files themselves. In this scenario, we input files onto their platform, if they have one, or just send updated files via email. The responsibility of managing the data is passed onto you, the client.
Supervising your Supplier
Any amateur can tell you to judge your supplier based on price, quality, and lead time. Unfortunately, the price, lead time, and quality are usually built into the design of the product. Meaning that if your design is not optimized, your end product will be made poorly. Of course, we have suppliers that just fail to make a good part but that’s why we have backup suppliers.
We should look deeper into the relationship between you and your CM. When you are launching your product, the most important part is the support you receive from your CM. If they help you to navigate from later stage development to tooling and product launch, they will most likely be a value-added CM.
Communication during the process is also extremely important. If your supplier agrees to everything you have to say, you might wind up with a sub-par product. A vocal CM that can communicate with you in order to improve your overall design is critical for a smooth transition into production and scale.
Overall, the relationship between you and your CM should be very tight. If you choose the right one, you can leverage them and they will support your overall processes. My next blog will look at how to take further steps and turn your CM into a partner for future growth.
Conclusion and How Can OpenBOM Help?
OpenBOM improves the process of how you work with your CM, contractors, colleagues, and other team members. We provide you with the capabilities to seamlessly manage your parts, vendors, bill of materials, purchase orders, and change orders. All BOM, engineering, and manufacturing information are stored in the cloud which you can share with anyone.
Register for FREE to create your OpenBOM account and reach out to us via support @ openbom dot com if you have any questions.
Regards,
Jared Haw
Join our newsletter to receive a weekly portion of news, articles, and tips about OpenBOM and our community.