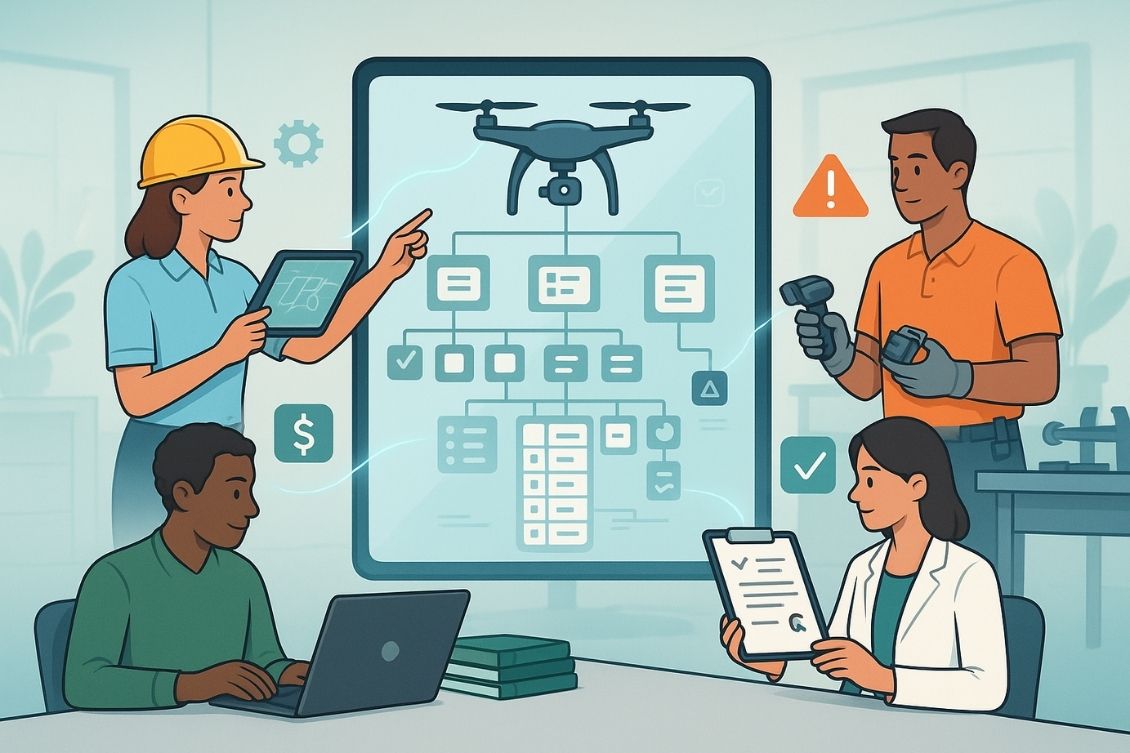
Bill of Materials is a core element of your product development recipe. Like in a kitchen, you want to get it right – accurate and without mistakes, manufacturing is the same. You need a correct prescription about what needs to be included in the product, from whom it will be purchased, how much it is supposed to cost, and many other factors.
And let’s face it — getting a Bill of Materials (BOM) right isn’t easy. It’s not just about listing parts. It’s about making sure the list is complete, accurate, and actually usable by everyone from engineering to manufacturing to purchasing.
From our experience of working with many engineers and teams, that kind of quality doesn’t happen in isolation. It takes collaboration.
The core element of OpenBOM- a Collaborative Workspace brings everyone together to work on the product definition, purchasing, manufacturing plans, and other activities. With a growing complexity of product and supply chain, we can see an increased interest from manufacturers and engineering team, how to organize their work to ensure the BOM is accurate and ready on time.
In this article, we start the discussion about how to organize the work across teams in a way it can help you validate your BOMs more effectively, catch mistakes early, and maintain quality throughout the product lifecycle.
Why BOM Quality Depends on Teamwork
A good BOM is a shared resource. And when it’s wrong, it causes problems for everyone. Think delays, scrap, compliance issues, cost overruns — the list goes on.
This is where things can get wrong if you think about the BOM as a “document”, which is not unusual. After all, Excel (or spreadsheet) remains one of the most frequent tools engineers and manufacturers use to create BOMs.
Engineering might create the BOM (it is easy because in many ways, the CAD system is the main source), but manufacturing, purchasing, and compliance teams are the ones who have to live with it. That’s why collaboration isn’t a “nice to have.” It’s a must-have if you want quality and control.
Collaborative Workspace Six Best Practices for BOM Validation
OpenBOM brings a collaborative Workspace, which can very much remind you of the beloved “Google Sheet”- it feels and looks the same, but it works with a structured product data, revisions, CAD files, dependencies, and links.
Here is what you can do.
1. Keep Everyone on the Same BOM (Literally)
Start by storing your BOMs in one place where everyone can access them. A cloud-based system like OpenBOM gives you real-time visibility, tracks changes, and ensures everyone’s working with the latest version.
No more guessing which spreadsheet is current. No more hunting through email attachments.
2. Assign Roles for BOM Review
Different teams bring different insights. Make sure you define who checks what.
- Engineering reviews part numbers, CAD links, and reference designators.
- Manufacturing checks quantities, units, and build feasibility.
- Purchasing reviews sourcing, cost, and lead times.
- Quality and compliance look at documentation, certifications, and regulatory alignment.
When everyone knows their role, nothing falls through the cracks.
3. Use Tools to Catch Common BOM Errors
Even with collaboration, mistakes happen. That’s where automation and data management comes in. Here are four important things to validate in BOMs.:
- Duplicate parts
- Outdated or obsolete items
- Missing quantities or incomplete descriptions
- Version mismatches
Some of these tools are available in OpenBOM (e,g. duplicated part check), some of them are integrated with OpenBOM (online catalogs), and some of them we are developing and would be very interested to discuss with you.
4. Run Structured BOM Review Sessions
Humans are in the middle of the development process. And therefore, don’t wait until the end of a project to review the BOM. Set checkpoints during design, before prototype, and before production.
Run OpenBOM tool for the online review, make comments. Then bring the team together. Share your BOM. Walk through the BOM with tools like OpenBOM’s Compare function to highlight changes. Capture comments and decisions in one place so nothing gets lost in an email thread.
Think of it as a quick team huddle to catch problems before they grow.
5. Make Comments and Feedback Part of the BOM
Your BOM isn’t just a list – it should also be a conversation between teams about what to do with that BOM.
Use an OpenBOM Collaborative Workspace to leave comments directly on the BOM (thanks flexible data model). That way, questions and feedback stay tied to the part they’re about. You can tag team members, resolve comments, and build a clear audit trail as you go.
This helps turn your BOM review into a living, collaborative process.
6. Keep the Feedback Loop Going
Just because a BOM is approved doesn’t mean the job is done. Once the product hits the floor, you might discover new issues or improvements. Therefore, use revisions and milestones.
Capture that feedback. Use it to audit BOMs regularly and improve your process over time. Quality isn’t a one-time check – it’s a habit.
The Real Value of Cross-Team Validation
There is nothing you can do to replace the power of the cross-team work. OpenBOM is a big help here because it connects and brings together multi-disciplinary BOMs. Here’s a simple example.
Engineering adds a component that looks great on paper. But then:
- Purchasing flags is discontinued.
- Manufacturing says it won’t fit the existing tooling.
- Compliance notes it fails a regional requirement.
If these teams aren’t involved in the BOM review, that issue could make it all the way to the production floor. If they are, it gets caught early — and you find a better solution without losing time or money.
Graph Data Science and AI-based Validation
We’re super excited to share that automated BOM quality validation is part of our ongoing research. We’re exploring how OpenBOM’s graph database engine and other modern technologies can be used to check BOMs and detect mistakes.
If you’re interested in being at the forefront of this discussion, we’d love to hear from you.
Conclusion: BOM Quality Is a Team Effort
You don’t get a high-quality BOM by accident. It takes clear roles, good tools, and a commitment to working together.
When you centralize your data, involve the right people, and build feedback into your process, you’ll catch more mistakes early and deliver better products faster.
So here’s the bottom line:
- Work together.
- Validate early and often.
- Keep improving.
Because the best BOMs aren’t just checked — they’re shared, discussed, and trusted by the whole team.
Related Reads
- What Is the Cost of BOM Mistakes?
- How to Use BOM Compare in OpenBOM
- Managing Multi-Disciplinary BOMs
REGISTER FOR FREE to check how OpenBOM can help.
Best, Oleg
Join our newsletter to receive a weekly portion of news, articles, and tips about OpenBOM and our community.