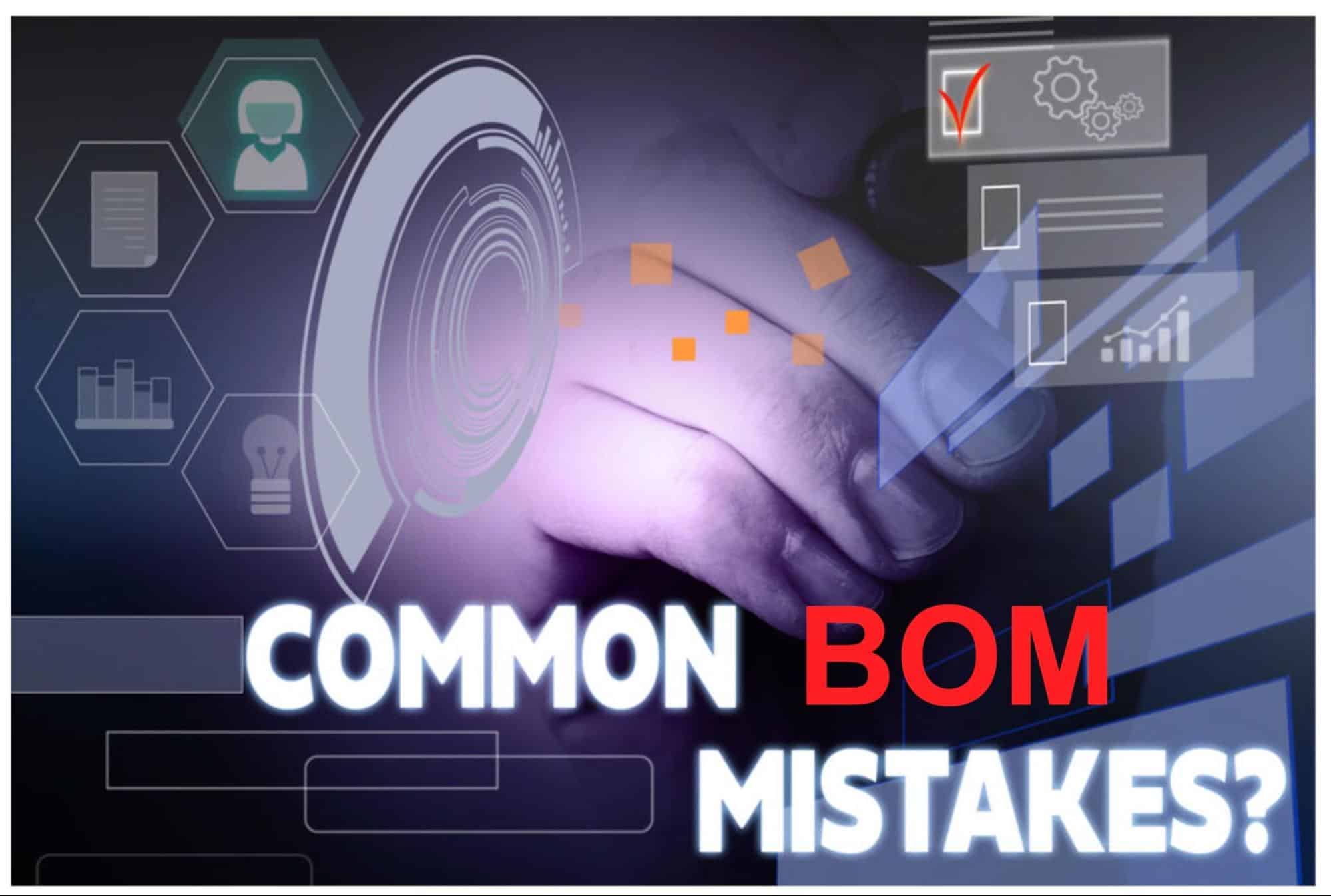
When it comes to manufacturing, the cost of mistakes can be high. This is especially true when it comes to the bill of materials (BOM). A mistake in the BOM can lead to wasted time and money as well as a shortage of essential parts. In this blog post, we’ll explore some of the ways that manufacturers can minimize the impact of a bill of materials mistakes. We’ll also take a look at some tools and technologies that can help you streamline your operations and improve accuracy. We’ll take a closer look at what the cost of BOM mistakes can be. We’ll also explore some ways to prevent these mistakes from happening.
Product Development Process and BOM Management
Bringing a product from concept to manufacturing is hard. You’ll face many challenges along the way. It is well known that about 70% of product cost is created during the early development stages. It is often difficult to see the impact and costs of a mistake early in the process. How to do it and how to avoid mistakes is the problem that many product development and manufacturing teams are facing these days. The demand for speed and complexity of the supply chain are just adding to the problem. How can you prevent these problems from happening and how can you ensure that these mistakes won’t happen again?
Data is the foundation of every process. Therefore, accurate data is the foundation of your successful product development process including data about engineering bill of materials, manufacturing bill of materials, product process, inventory management, and coordination of these activities. Having a Bill of Materials for the finished products including data about the assembly process, and production process allow you to expose hidden costs early in the process and eliminate mistakes before they happen. Using wrong components, human error during copy/pasting of data, and the absence of a complex bill of materials are very typical elements of BOM mistakes.
CAD Design and BOM system
The foundation of product data is initially created during the CAD design phase. This process is very complex and requires many steps. One of the most typical problems that happen at the stage of design is a full disconnect between design data and the engineering bill of materials including later connection to ERP and procurement processes.
The data disconnects and complexity of data handover create tons of problems when both design and procurement teams are working in parallel but don’t have access to the accurate data set as well as not capable of merging and synchronizing data between them. The seamless data handover and digital data thread are the foundation of a successful solution to eliminate BOM and related mistakes. An ability to expose data downstream early in the process is key, but to have this data in sync multiple ways is also super important.
5 Typical BOM Mistakes
Working with thousands of manufacturing companies, I’ve learned about what are the most typical mistakes that can happen in Bill of Materials that can cost the manufacturing process a fortune and can easily kill the company at the early stage or leads to substantial economical disadvantages for a large manufacturing company.
- Quantity mistakes. These problems are happening because of missing parts required and miscalculations of inventory management and procurement processes. Wrong data extraction, wrong rollups, wrong information about stock, and you will be struggling to have the right components at the right time with the right cost.
- Missing components in Bill of Materials. Usually, these types of mistakes are happening because of wrong data exports from design and also from forgetting to add specific items to the BOM system. Manual data entry and absence of collaboration are usually reasons why such mistakes are happening.
- Costing Mistakes. Checking costs at the early stage is hard. Companies have difficulties with cost rollups and push them to a later time. But later discovery won’t help because the design is finished and components are already ordered.
- Missing requirements. One of the roles of the bill of materials is to ensure that the engineering and production process is synchronized with procurement and components specs that will be ordered. The outcome is mistakes related to product functions and costs associated with these mistakes.
- Liability Claims and Regulatory Cost. Missing regulatory requirements is a very typical mistake that happens because of the disconnect between engineering and procurement. It is hard to manage this information in multiple Excels – you will miss something for sure.
Conclusion
BOM mistakes are super costly and can cause major disruption to the manufacturing process and a manufacturing company. It can disrupt your production process, cause additional costs to your product or come later as liability and compliance costs.
To avoid BOM mistakes, you need to invest in BOM data management and systems that can help you extract and manage data automatically, eliminate manual data entry, share BOM early in the process between departments and teams and run the analysis of the data to avoid functional and regulatory mistakes.
PLM and BOM management is a way to eliminate costly mistakes. REGISTER FOR FREE and check out how OpenBOM can help you today.
Best, Oleg
Join our newsletter to receive a weekly portion of news, articles, and tips about OpenBOM and our community.