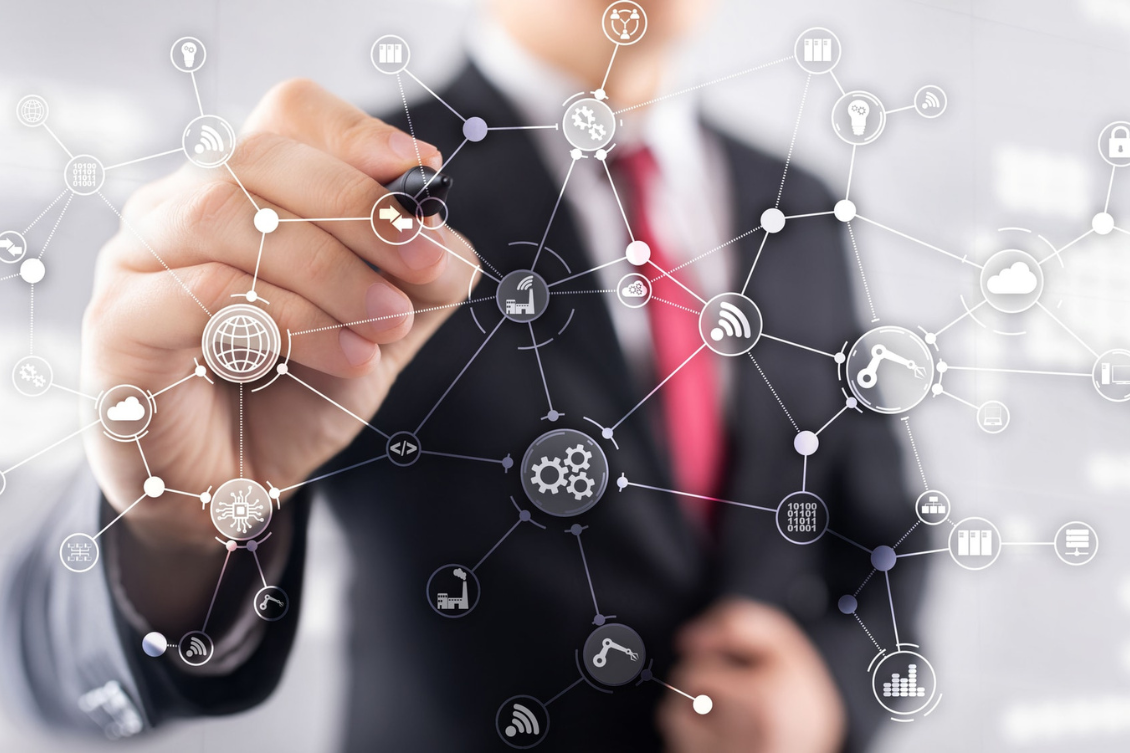
The data is the backbone of every organization. For companies building products, comprehensive information about components, subsystems, suppliers, processes and organizations involved into design and manufacturing processes, forms the digital foundation of a manufacturing company. This foundation is essential for organizing processes that span across design, engineering, production, sales and maintenance. This information allows people to make informed decisions and run businesses.
But here is the thing… The reality many companies face is that their digital foundation is fractured and broken. The siloed data is presented by multiple systems, legacy databases, tons of Excel spreadsheets and email. This disconnection hinders the ability to organize efficient workflows, resulting in delays, errors, and missed opportunities.
In my article today, I will speak about how digital thread systems can help to connect information and help companies establish a digital foundation for their businesses.
The Challenge of Siloed Systems
The adverts of legacy PLM systems, advised for a single source of truth that will build a foundation for product lifecycle. While the idea of a single source of truth (SSOT) is a good one, the approach offered by old PLM systems was far from an ideal. To put all information in a single SQL database combined with document management system and lock data from being effectively exchanged and connected with other pieces of information didn’t work well.
Although, the broken nature of data management is a problem, it arises for understandable reasons. Manufacturing companies frequently rely on a variety of software tools to handle different functions such as design (CAD), release management (PDM), planning (ERP), procurement (MRP), and manufacturing execution (MES). These tools are often specialized to meet the unique needs of each department or process, making it necessary for companies to continue using them. The challenge lies in how to keep these specialized systems while ensuring that information remains connected, traceable, and accessible across the organization.
The Role of the Digital Thread
An evolution of product lifecycle management (PLM) and product data management (PDM) is leading us towards creating an infrastructure and a system that can use modern data management concepts to integrate and connect information. Similar how web technologies for the last 20-30 years created a connected internet environment, modern network based data management systems and PLM software will connect a complex product development process.
This is where the concept of a digital thread comes into play. A digital thread refers to the seamless flow of data across the product lifecycle, ensuring traceability and integration across various stages of development and production. It helps to bridge the gap between different systems, enabling the flow of information from one stage of the product lifecycle to the next without the risk of data loss or miscommunication. Digital thread allows to connect supply chain management with multiple contractors and suppliers and to support service lifecycle management for organizations switching their business models from selling products to providing service. Most importantly, it allows all parties (design centers, OEMs, contract manufacturers, and customers) to stay connected with up to date information.
How OpenBOM Supports the Digital Thread
The foundation of OpenBOM is built on the concepts of open multi-tenant data model that allows to data resources to connected and shared across multiple companies. For all people concerned about security, please stay calm. In the same way data can be protected in online environments and global web platforms, OpenBOM provides a mechanism to control who has an access to data. Also, a special enterprise deployment models of OpenBOM allows you to create an instance of OpenBOM that only available for an enterprise company with all contractors and suppliers, but excluding everyone else.
At OpenBOM, the digital thread concept is brought to life through three key elements of its data model, each of which plays a critical role in connecting data across systems:
- Flexible Data Objects: OpenBOM allows for the creation of flexible data objects, such as items, requirements, maintenance BOMs, certifications, and documentation. These data objects can represent various facets of a product or process, making it easier to manage diverse types of information.
- Product Structure and Object References: OpenBOM’s xBOM system supports multiple structures and creates object references that allow different objects to be linked. This approach provides the flexibility to map the complex relationships between components, subsystems, and products, ensuring that every part of the product lifecycle is connected.
- Adaptive User Interface and Graph Navigation: OpenBOM’s user interface is designed for ease of use, with grid views, powerful search capabilities, and graph-like navigation. This makes it easier for users to traverse data, discover relationships between different elements, and maintain a holistic view of the product and its lifecycle.
You can learn more about OpenBOM flexible data model, custom objects and object references as well as real-time collaborative data grid and graph navigation.
Flexible Object Types
OpenBOM allows users to manage various object types, such as items, serial numbers, test documentation, and more, all within a single system. This flexibility ensures that product data remains accessible and traceable, regardless of the source or format. By supporting diverse data objects, OpenBOM enables organizations to connect to different aspects of the product lifecycle, making it easier to explore, manage, and retrieve when needed. A flexibility in data model and granular data sharing allows you to organize role based cross functional teams and organizations to access data without the need to export it or use complex “sync” patterns.
Multiple Product Structures (xBOM)
With OpenBOM’s xBOM capabilities, companies can organize their data into multiple structures that align with their specific needs. These structures can represent anything from simple assemblies to complex multi-level product configurations. By using object references, OpenBOM allows users to link different items, components, and systems together, creating a connected flow of data across the product lifecycle. This capability ensures that information is not isolated within different silos but is accessible and integrated, fostering a more connected and streamlined process.
Object References
Object references are a key feature within OpenBOM’s data model that enables the connection of various data objects. By creating references property, the data from one record (eg. Item) is connected to other objects (eg. design, requirements, order, etc.) OpenBOM allows users to build relationships between different aspects of the product lifecycle. These references create a unified, traceable flow of information, ensuring that data remains connected, regardless of its source. This capability is essential for maintaining traceability, managing changes, and ensuring that all relevant information is available at each stage of the manufacturing process.
User-Friendly Navigation
In addition to its powerful data model, OpenBOM offers a user-friendly interface that simplifies data navigation.
With grid views, advanced search features, and graph-like navigation, users can easily find and interact with the data they need.
This intuitive interface ensures that data remains accessible and easily traversed, allowing users to explore the relationships between different objects and maintain a comprehensive understanding of the product lifecycle.
Conclusion
The ability to maintain flexibility while building a connected, traceable flow of information is what sets OpenBOM apart. By providing tools that foster both adaptability and connection, OpenBOM helps manufacturing organizations build a solid, interconnected digital foundation. This foundation supports the seamless flow of data, from design to production and beyond.
In future articles, we will explore more practical examples of how OpenBOM’s data model can be used to build and enhance the digital thread within manufacturing organizations. Stay tuned for insights into how you can further optimize your digital processes with OpenBOM.
REGISTER FOR FREE and check how OpenBOM can help.
Best, Oleg
Join our newsletter to receive a weekly portion of news, articles, and tips about OpenBOM and our community.