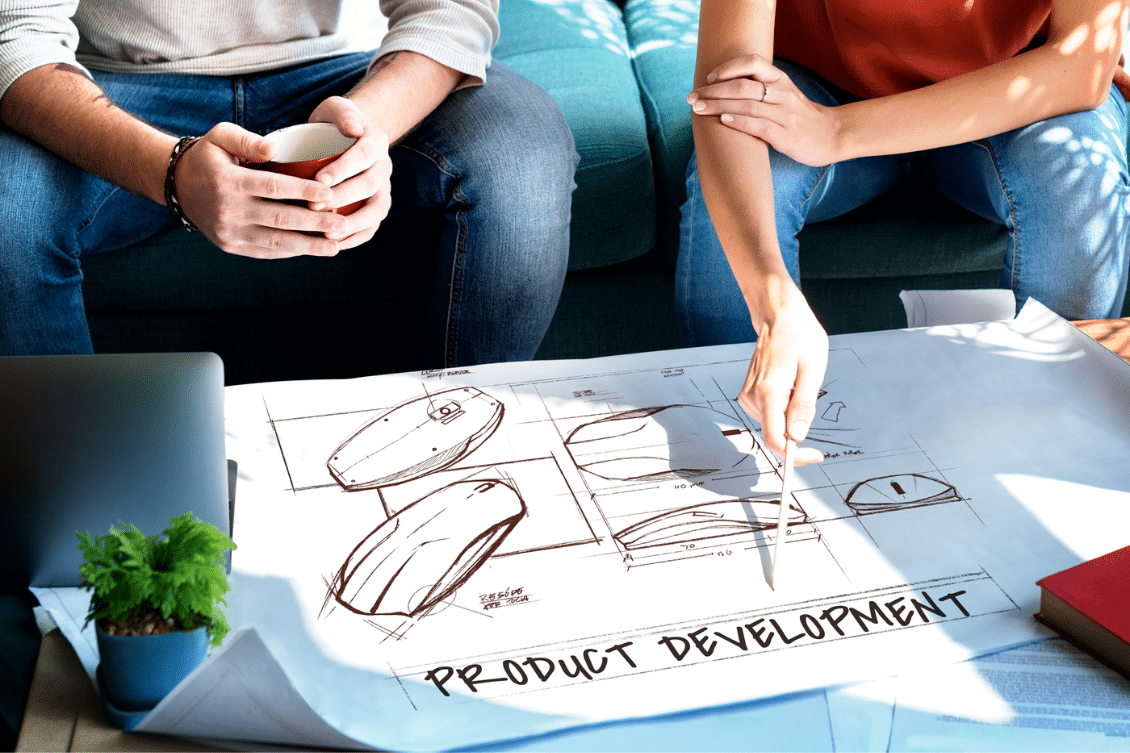
The demand for innovation and speed in manufacturing has never been higher as it is these days. For the last decade, we’ve seen an amazing level of democratization in manufacturing processes allowing small and agile product development teams to build innovative products faster and at a lower cost. Although enterprise manufacturing companies have more resources, they are experiencing organizational complexity in new product development.
New Product Development Challenges
Enterprise manufacturing companies often face challenges when it comes to managing new product development teams. In many cases, these teams require a different management approach compared to other departments within the organization. As a result, many companies choose to manage their new product development team separately to better address the unique challenges and opportunities associated with bringing new products to market. This approach allows for more focused attention and resources to be allocated to the development of new products, resulting in a more efficient and effective product development process. These organizations operate separately (think about internal startups or entirely separate product development units) focusing entirely on how to build new innovative products.
Why Enterprise PLM and ERP Are Not A Good Fit?
New product development is a complex process that involves multiple teams, technologies, and resources. At the same time, it is a very different process from a traditional large-scale enterprise manufacturing process oriented on stable processes, with large-scale facilities, contract manufacturing, and large supply chains.
Here is what is important for agile and fast new product development, which allows to compete with the large and rigid manufacturing process:
- Speed of Innovation, customer focus, and time to market: New product development teams can quickly react to trends and consumer demands, and iterate their designs accordingly. Smaller teams are often more customer-focused and can provide a more personalized experience for their customers with a shorter loop to product development. New product development teams can move faster in the product development process, from design to prototyping to small production batches. This allows them to bring new products in small volumes to test the market or experiment in product development facilities.
- Manufacturing flexibility: Smaller teams may be able to manufacture products in smaller quantities, which can be particularly advantageous when introducing a new product to the market. They can test the market with a limited run, assess demand, and then adjust their production accordingly. Large manufacturing companies may not have the same level of manufacturing sophistication, as they often have to produce products in large volumes to make them cost-effective, but they are more flexible and adaptable.
- Flexible supply chain: Fast and agile process allows small teams to find solutions for supply chain and sourcing that is not available for large and complex production processes and large contract manufacturers. Small new product development teams can work with alternative suppliers and limited sources of materials to develop new products that in general can be not approved for a broad scale and are not validated by corporates for general usage.
In other words, small and agile new product development teams can move faster, to “cut corners” and ignore rules. One can think, of a problem being solved. However, this is a place where they face a new challenge. All tools large manufacturing companies have are not fit to operate with the speed and agility needed to support this new product development process.
All enterprise manufacturing companies are relying on complex and rigid product (PLM) development and manufacturing (ERP) tools. Both are represented by well-established large software providers with decades of reputation and history of work. Enterprises validated them and spent literally millions of dollars to make them fit their large-scale product development process.
However, all these tools fall short to deliver and support new product lifecycle management inventory management, and supply chain management with their need for speed, innovation, flexibility, and agility. When large systems cannot solve the problem, teams are moving into Excel and spreadsheets to solve their problem, which causes them a lot of pain, complexity and inefficiency.
3 Limitations Of Enterprise PLM and ERP For New Product Development
Traditional PLM and ERP tools are not fit for agile and fast new product development processes. Let me explain why. We identified these three barriers:
Lack of Integrated Data, Process Management, and Inventory Management
Traditional PLM and ERP systems usually separate product design, engineering, and manufacturing processes into separate well-defined processes. They manage engineering BOMs separately from their inventory management and ordering systems. While it is absolutely needed for large-scale manufacturing, it is like a hammer to fast-moving teams. Enterprise PLMs don’t have inventory management and ordering functions. Enterprise EPR doesn’t have efficient CAD integrations, engineering BOM support, and collaborative functions. Siloed data models and prohibitively expensive integrations won’t allow making them work to support NPD.
To overcome this limitation, businesses should look for modern SaaS-based systems integrating PLM and ERP capabilities together providing integrated data management, business process management, and inventory management. These systems should provide a centralized repository for all NPD-related data, allowing teams to track inventory management levels, monitor ordering processes, and manage data effectively.
Lack of Collaboration and Flexibility
NPD is a highly collaborative process that requires flexibility to adapt to changing market needs and customer demands. However, traditional product lifecycle management (PLM) and ERP systems often lack the collaboration features and flexibility required for effective teamwork. These systems are designed for a well-established rigid process and they slow down team progress. As I heard many times, there is no better way to stop the project than to load it in the enterprise PLM tool.
To address this limitation, businesses should look for integrated SaaS-based tools that provide robust real-time data collaboration features and flexibility. These systems should allow teams to easily share data and collaborate in real-time, no matter where they’re located. Additionally, businesses should consider adopting a data management system that provides a centralized data repository for all NPD-related data and facilitates collaboration between teams.
Overall Complexity and Need for Speed
NPD is a complex process that requires speed and agility to keep pace with rapidly changing market demands. Traditional PLM and ERP systems can’t always keep up with the need for speed and may create unnecessary complexity in the process. Formal approval processes, data management limitations, complex user interface – this is only a short list of what slows down teams when they try to use existing legacy tools
To overcome this limitation, businesses should look for modern SaaS-based tools that provide a streamlined, user-friendly interface and fast data processing capabilities. These systems should be designed to minimize complexity and enable teams to focus on innovation and speed to market.
Conclusion:
Traditional PLM and ERP systems can fall short of addressing the complexities of NPD. Businesses need to look beyond these systems to find innovative solutions that can integrate data, business processes, and inventory control, facilitate collaboration and flexibility, and enable speed and agility. By adopting modern SaaS-based, integrated services providing both PLM and ERP capabilities, enterprises can speed up the innovation process and optimize their new product development process. As a result, enterprises can improve their NPD outcomes and gain a competitive advantage in the market.
Interested in how OpenBOM can help you? Contact us at oleg@openbom.com to discuss more.
Best, Oleg
Join our newsletter to receive a weekly portion of news, articles, and tips about OpenBOM and our community.