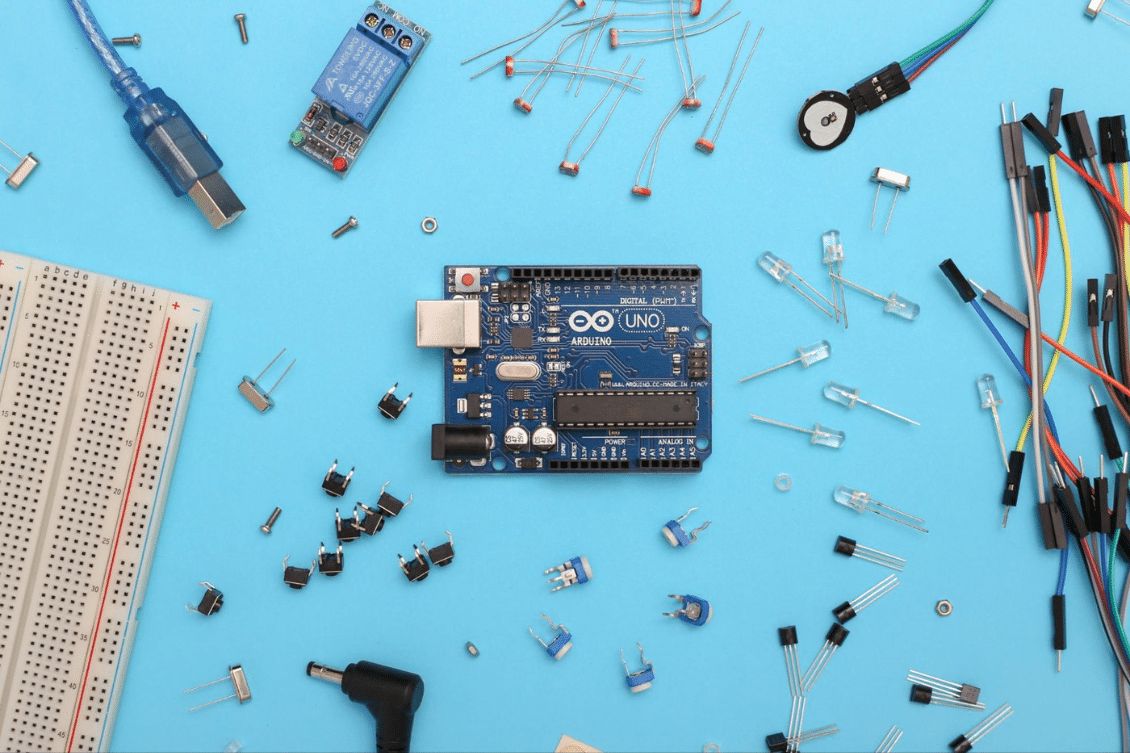
In the complex world of manufacturing, encountering a supply chain challenge is not uncommon. One of these hurdles is when a manufacturer places a purchase order (PO) to either their contract manufacturer (CM) or supplier only to discover the component is no longer available in the market or has a lead time that no longer makes it an option.
While this situation is far from ideal, a reliable supplier can play a pivotal role in assisting you in finding a suitable replacement. In this blog, we will explore the steps involved in the process of sourcing a new part, ensuring it meets requirements, and maintaining quality while managing costs.
Communicate With Your Supplier
Before anything, you will need to speak with your supplier to find out whether or not the part is obsolete in the market or if the supplier ran out of inventory. If the supplier just ran out of inventory then the solution is simple, find another supplier for that same part. However, let’s assume the part is obsolete.
When a manufacturer realizes that the specified part is no longer available, the first step is to acknowledge the issue. It is crucial not to panic and instead focus on seeking a solution. This situation demands prompt action and close collaboration with a trusted supplier.
During this time, you will need to gather all the information you can about this component. This will be used to find a local alternative, if there are any in the market.
You will also want to talk to your supplier about potential lead time to find an alternative component. This might be quick or it might take time. Depending on the initial feedback, you can start to plan what you need to do with your current inventory and start developing a plan to manage customers.
Identifying Local Suppliers
Whether it will be a team of engineers in your company or your contract manufacturer, the next step will be to identify a list of suppliers and components who can offer a replacement part. These local suppliers will usually have an inventory of these components and you might be able to get a pretty quick turnaround time.
When sending component information to your supplier need to offer the supplier a list of requirements and specifications for the new component. Based on the inputs you provided, they can propose an alternative part. These alternative components might not match perfectly with what you were using before but then it’s your responsibility to define whether or not the component will be acceptable.
Analyzing Compatibility and Requirements
The next step involves evaluating the compatibility of the potential replacements with your product. Your supplier will meticulously compare the technical specifications and functional requirements of the original component with those of the alternatives. This step is vital to ensure that the new part seamlessly integrates into your product.
Obtaining Pricing and Samples
Once the supplier narrows down a list of potential replacement components, you can obtain both prices for the replacement parts along with samples. Manufacturers should thoroughly assess not only the cost but also the quality and reliability of the samples received.
Based on the samples and pricing, the manufacturer will be able to carry out tests to see whether or not any of the components provided can replace the component that is not obsolete.
Confirmation
With the pricing and samples on hand, it is time for the manufacturer and the supplier to engage in collaborative decision-making. The manufacturer will need to weigh the pros and cons of each option while considering factors like quality, compatibility, lead times, and costs.
After a thorough analysis, the manufacturer will provide feedback to the supplier, confirming the best-fit replacement. At this stage, open communication is essential to address any concerns and reach a mutual agreement.
Implementing the New Part
Once the new part is confirmed and tested, it is time to implement it into the manufacturing process. The supplier will support the manufacturer throughout this transition, providing any necessary guidance or assistance.
Conclusion
By following a well-structured process of communication, evaluation, and decision-making, a suitable replacement can be identified and implemented for obsolete parts. Manufacturers should recognize the importance of proactive research in choosing dependable suppliers to mitigate such issues, but in cases where research falls short, a strong partnership with a supplier will undoubtedly help overcome obstacles and ensure smooth production workflows.
The first step is to always manage your data in a way that is accessible to the rest of your team. If you have data that is in different data silos and not available to key stakeholders at certain times then the time to find a new supplier and implement a rolling change will be increased.
Regards,
Jared
Join our newsletter to receive a weekly portion of news, articles, and tips about OpenBOM and our community.