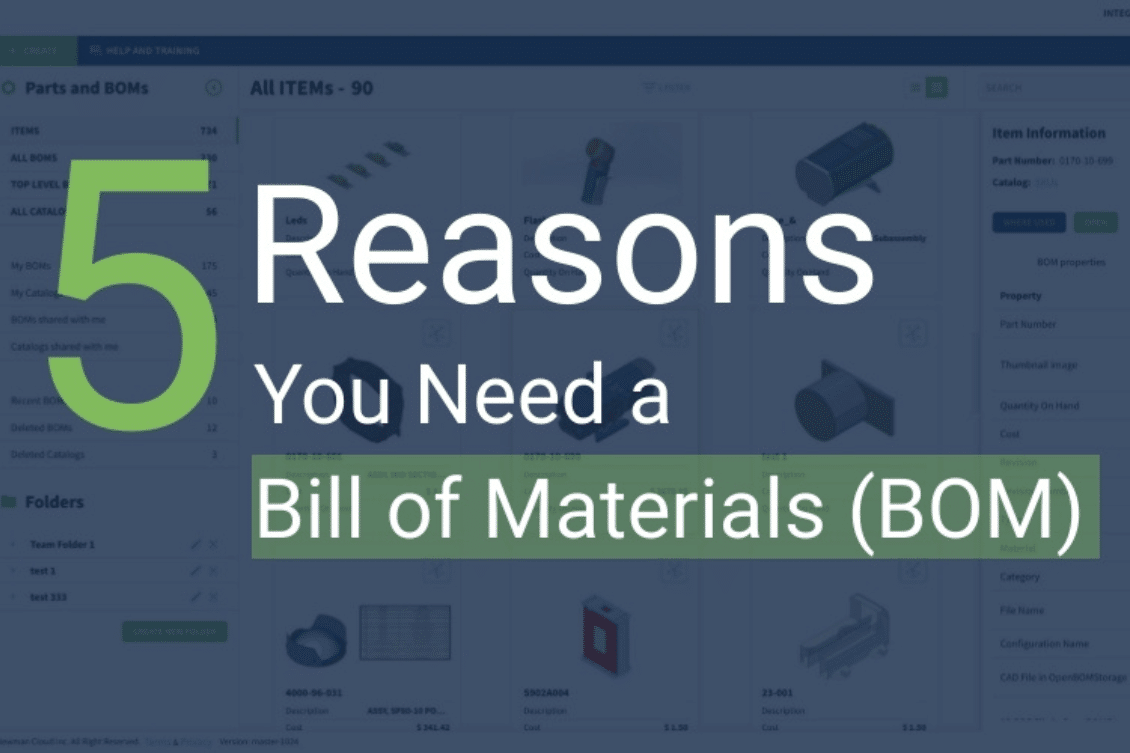
In manufacturing, companies demand precision, accuracy, and speed in both product development and production. This becomes difficult as manufacturers seek to cut costs and build a more complex product. Therefore, the way companies manage their product data becomes crucial to the success of their product. The document used as the central part of development and production is known as the Bill of Materials (BOM).
The BOM is the heart of any product that’s being manufactured. And while the BOM is essential, it is often misunderstood. With this misunderstanding, it’s often not shared correctly and not updated which leads to incorrect purchases and delays in production.
You can look at the BOM as the document to ensure consistency in your manufacturing processes. Yet, all too often, companies rely on Excel, Spreadsheets, Airtable, and other systems that aren’t built to manage sensitive product information that needs to be kept up to date.
In this blog, we’ll go over the 5 reasons you need a BOM and the risks of managing your BOM in a system similar to Excel.
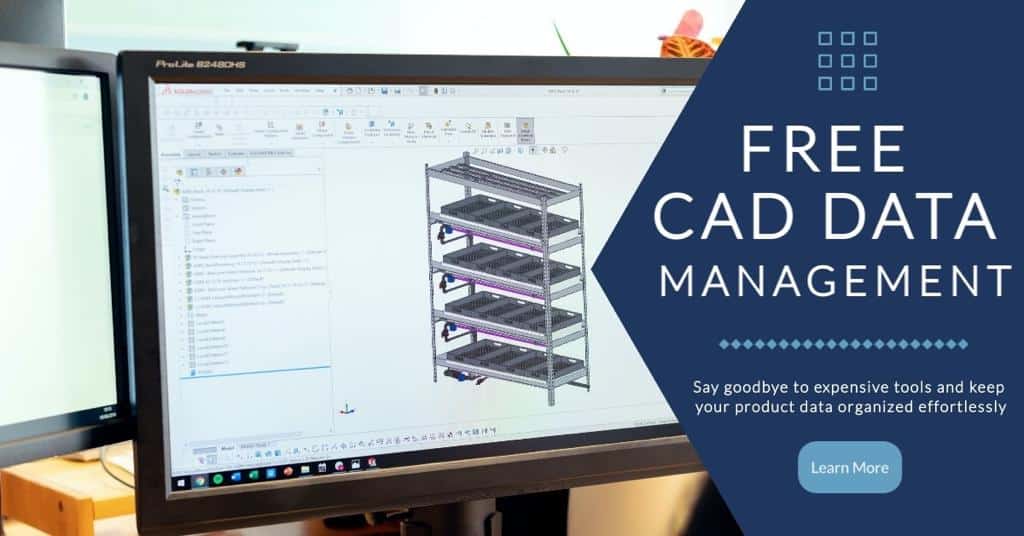
Reason 1: Total Component Visibility
A well-structured BOM provides you with a view of all the components needed for your product (both items modeled in CAD and non-CAD items). This also ensures that nothing is overlooked and every part, no matter how small, is accounted for.
Having this visibility in parts will help your team purchase components, find alternative suppliers, and keep a record of all changes that have occurred to the product. Therefore, you can see the price of a certain component during a specific time and compare that to the price at another date.
The BOM will provide info on each component, such as:
- Quantity
- Material
- Color
- Fabrication Process
- Cost
- Total Cost
Reason 2: Transparent Pricing
Managing costs is important in any project. A BOM should provide transparent pricing for you to know exactly what you are spending money on.
If you have a product that consists of 100 components then you should have 100 items on the BOM. If you have 100 items on the BOM then you should also have 100 quotes. A quote for each item.
By having this price transparency, you can execute certain cost-down initiates to drive the price down. Without this price transparency, how do you see the value of the product?
During the development process, all changes to the product will have an effect on the costs. These changes along with the new price need to be documented. You can quickly compare prices for each change so make sure you manage costs during the development process.
Reason 3: Version Control
Through agile product development, iterations and changes are common. You need to be able to adapt quickly to changes in the market and pivot based on customer feedback. Long gone are the days when you develop the product fully and pass it to the next step. Keeping an up-to-date BOM allows for quick design iterations
A BOM will provide you with a way to manage multiple versions and ensure that everyone is working on the most up-to-date BOM and product data.
Reason 4: Collaboration and Accessibility
Working with teams across the world is not a new concept. Manufacturers are working with teams across the world to ensure the highest quality of work can be delivered. Oftentimes this means a manufacturer working with a contract manufacturer in China to leverage their design for manufacturing (DFM) capabilities.
While a BOM is an important document, it’s not just meant for one person, it’s for the entire manufacturing organization. But why do companies still use software that can’t be shared, such as Excel to manage their BOMs?
Digitalization of the BOM is a dynamic way to communicate and work with your team members and contractors. It’s also being more widely used in the industry with companies like OpenBOM offering manufacturers a way to digitalize their processes.
However, still, 35% of manufacturers continue to use Files and Excel to manage their production data.
Reason 5: Integration and Data Flow
A modern BOM system seamlessly integrates with other business tools and systems, such as CAD and ERP systems, to ensure a smooth data flow from the creation of an item in CAD all the way through to purchasing.
By offering the integration into other systems, you are creating a single source of truth by removing all data silos. These data silos were often created through the creation of a part that was exported to Excel. That Excel was then exported to another team member, updated, and passed on. But then, who knows what the most up-to-date version is and who has it?
This integration also removes tedious tasks, such as manual entry which is often error-prone.
Why Not Use Excel?
Excel, with its rows and columns, seems like an intuitive choice, especially for those already familiar with its interface. It’s versatile and it’s seemingly straightforward. However, beneath this familiar face lays a liability. But change is difficult.
Here are the top reasons why manufacturers decide to not replace Excel.
- Engineers are afraid of complex PLM systems
- It’s difficult to import data
- PLM systems don’t have good reporting mechanisms
- Many PLMs don’t include a flexible data model
- PLMs are expensive and manufacturers don’t have the budget
While legacy PLM systems are different there is a new wave of companies who can simplify the process for you and also have an intuitive interface.
How to Move Forward?
If you are looking to bring visibility of your product data to the rest of your team and supply chain then implementing digital processes is for you. While transforming your company to a new system can take a while, there are some quick fixes that you can make. The first would be to Trade Excel Files for a Data-Centric Strategy.
OpenBOM is a cloud-based PDM & PLM platform to manage your engineering and manufacturing data. Companies from startups to Fortune 500s use OpenBOM to create a centralized database to bring in, store, and manage their manufacturing data. With this infrastructure, users also use OpenBOM to streamline both their change management and PO processes.
If you need to improve the way you manage your data and processes, share data instantly, or collaborate with contractors and suppliers. contact us today for a free consultation.
Regards,
Jared HW
Join our newsletter to receive a weekly portion of news, articles, and tips about OpenBOM and our community.