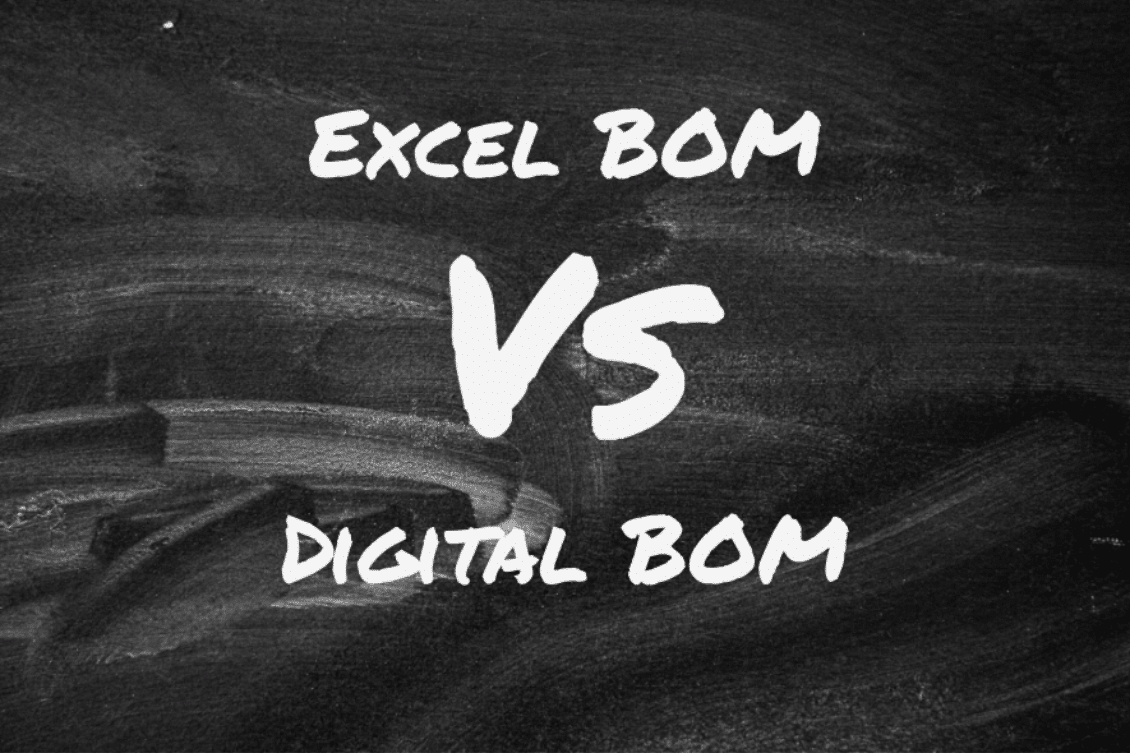
In the fast-paced world of manufacturing, precision and efficiency are key. Manufacturers understand the critical role that accurate and well-organized product data plays in the success of any product. Central to this process is the Bill of Materials (BOM), the key document that holds the manufacturing knowledge of your product.
For decades, the go-to tool for managing BOMs has been Excel or Spreadsheets due to its popularity and ease of use. However, as products grow in complexity and timelines become tighter, relying solely on Excel BOMs can pose significant risks and challenges.
While Excel served its purpose, manufacturers have acknowledged the importance of moving their processes to a digital platform. Thus, companies have moved to use a digital BOM instead of Excel.
Join us as we go over why manufacturers use Excel to manage their BOMs, the limitations of Excel BOM, and explore the transformative benefits of embracing a digital BOM system.
Why Use Excel?
With all of the digital tools that we have now, why do manufacturers and engineers continue to use Excel to manage their manufacturing data? In a previous blog, The secret of why engineers are using Excel instead of PLM was finally revealed we outlined 5 reasons why engineers continue to use Excel:
- Simple
- Flexible
- Absorb any type of data
- Physical ownership
- Transferable
Why Not Replace Excel?
Replacing Excel seems to be easier said than done. PLM systems have been advocating switching from Excels for years. However, most companies have not made the transition. But why?
In a previous post, we looked at the reasons why manufacturers decided to not replace Excel. Here are the top 5 reasons:
- Engineers are afraid of complex PLM systems
- It’s difficult to import data
- PLM systems don’t have good reporting mechanisms
- Many PLMs don’t include a flexible data model
- PLMs are expensive and manufacturers don’t have the budget
Manufacturers have realized that they need to transform their processes. However, a large number of engineers are still using Excel to manage their design and product data.
In a LinkedIn Poll, we published last week, we received feedback from 932 respondents. Of these 932 people, 35% said they still use Excel to manage their design and production data. 47% said they use a PDM and PLM system.
While the majority of the respondents use a PDM and PLM system, a good percentage are still stuck using Excel to manage their design and production data.
What is a Digital BOM?
Manufacturers are looking to bring products to market faster. To support this, companies need to implement agile product development, enable collaboration, make decisions faster, and more. Manufacturers have realized that in order to do this, they need to use tools that support their goal. One tool that is upgraded would be going from an Excel BOM to a digital BOM.
The digital BOM is a dynamic way to communicate and work with your team members and contractors.
Why Use a Digital BOM?
The goal of the digital BOM is to start to digitalize your processes and to make sure that everyone who is working on your product has the most up-to-date BOM. This is also a step towards digital transformation.
Here are four reasons why you should use a digital BOM:
Real-time Collaboration and Accessibility
Digital BOMs provide a centralized platform that allows engineering, procurement, operations, and other teams to collaborate in real-time from anywhere in the world. Unlike Excel BOMs that require manual updates and emails back and forth, a digital BOM ensures that everyone works on the same BOM and has the most updated and accurate data.
Enhanced Data Accuracy and Integrity
Excel BOMs are prone to human errors, such as purchasing incorrect parts, incorrect formulas, data entry mistakes, etc… Digital BOMs significantly reduce the risks of costly BOM errors caused by incorrect data.
Efficient Change Management
As your product design evolves, you might have the introduction of additional processes to offer additional control. One process is change management. Digital BOMs are an efficient way to track these changes, update parts, and keep your procurement and other teams up-to-date with the most updated BOM.
Integration with Other Systems
A digital BOM is a step into the world of digital transformation. These tools were created for seamless integration with all your business tools, Product Lifecycle Management (PLM) software, Enterprise Resource Planning (ERP) systems, and Computer-Aided Design (CAD) tools.
Are Manufacturers Resistant to Using a Digital BOM?
While processes are becoming digitalized, there are some manufacturers who do not wish to move with this trend. Some of these reasons depend on their connectivity while others depend to keep using familiar documents.
Here are three reasons why companies decide to not use a digital BOM:
- Familiarity and Ease of Use
- Cost Considerations
- Offline Accessibility
Conclusion
Excel is a powerful and versatile tool that has many advantages but they also have drawbacks. For manufacturing companies, these drawbacks are starting to outweigh the advantages. For this reason, you have seen the emergence of the digital BOM.
If you are looking to digitalize your process then OpenBOM has a product for you.
OpenBOM is a cloud-based platform to manage your engineering and manufacturing data. Companies from startups to Fortune 500’s use OpenBOM to create a centralized database to bring in, store, and manage their manufacturing data. With this infrastructure, users also use OpenBOM to streamline both their change management and PO processes.
If you need to improve the way you manage your data and processes, contact us today for a free consultation.
Regards,
Jared Haw
Join our newsletter to receive a weekly portion of news, articles, and tips about OpenBOM and our community.