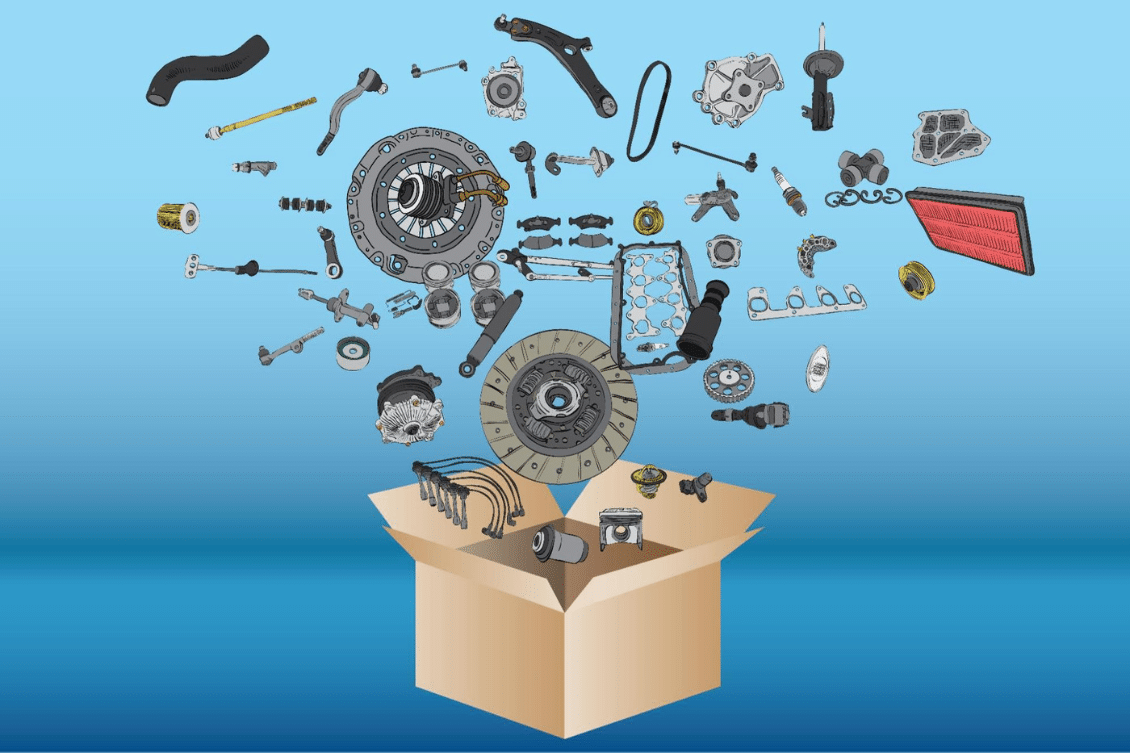
Data organization is key for any successful Product Lifecycle Management (PLM) program. The ability to manage, organize, search, and quickly access product information can make the difference between smooth-running product development processes or inefficient workflow within an engineering team. OpenBOM provides an Item Catalogs mechanism to organize product data. It is a flexible and efficient way to organize product data and manage all attributes, revisions, file attachments, and any linked information.
OpenBOM catalogs are simple, but there are some important steps required in order for them to be done correctly. In this article post, we will look at three best practices when creating item catalogs in your OpenBOM database. Having an organized system will generate fewer errors and create better visibility into product information throughout your manufacturing process.
Catalog Basics
OpenBOM catalog is designed to store information about any item (parts, assemblies, labor, etc.) which may be used later in your products. Think about anything- off-the-shelf parts,c custom parts, fasteners, plastics, electronics, software, and… practically anything else. This is a basic building block for OpenBOM data, components. OpenBOM Catalogs is a centralized location for all your items. Essentially anything in your company that has a part number can be an entry in catalogs.
The picture below shows the basic data model used in OpenBOM to manage data in catalogs and BOMs.
Catalogs can be using multiple attributes. We call them properties in OpenBOM. There are many property types in OpenBOM that can be used to define text, numbers, lists, links, files, images, etc.
3 Best Practices
One of the questions often comes from new OpenBOM users about Catalogs – how many Catalogs should I create? First I want to warn you about the possible mistake of attempting to create a single catalog for everything. I call it a “single spreadsheet syndrome”. It is happening with many organizations that were using Excel (or any other spreadsheets) before switching to OpenBOM. In fact, the granular catalog definition is one of the foundational elements of a successful data management strategy. It will allow you to create a scalable set of catalogs
1- Define Item Types and Catalog Properties
The first step is to make an analysis of all items you want to manage using OpenBOM with all properties. Don’t be afraid to be granular and think about OTS or custom parts, mechanical, electronic, fasteners, plastic, hardware, software, electronics, etc. Once you gathered all these “item types”, you need to make an analysis of attributes. Ideally, you want to have catalogs with a homogeneous set of attributes. No one will like to create an item (screw) and find out that the catalog for screws has a “voltage” attribute that usually belongs to electronics.
Once you classify all your data, then comes the step to define all attributes. You can use public and private attributes in OpenBOM. Our recommendation is to create a set of private properties that can be used in all catalogs. For more information check the article – How many catalogs do I need to create in OpenBOM?
2- Automatic Catalogs Creation Using CAD add-ins
This is the fastest and easiest way to manage catalogs in OpenBOM. When data is extracted from the CAD system, OpenBOM can map each CAD file (or data – eg. Part, Assembly) to a specific catalog. OpenBOM CAD add-ins provide you with settings on how to do so.
If you plan to generate your data from CAD, we recommend a plan to create catalogs using CAD add-ins to avoid future conflicts between data that is defined in CAD files (or data) and any other data you can create later. The main reason for that is that CAD data is much harder to adjust and if you want to avoid editing CAD data, you need to start from CAD.
Check the following two videos for examples of how to do so in SOLIDWORKS and Onshape.
3- Manual Catalog Creation and Data Import
After you established the set of catalogs and imported the initial set of data from CAD systems, it is time to create or import data from other data sources. You can import data from Excel, you can pack your data from legacy databases or ERP systems.
Keep in mind that OpenBOM catalog import works in a way that allows you to make data mergers and only bring the data that will be added to already existing records. Catalog import from spreadsheets doesn’t delete existing items – only adds and updates. Also, item records attributed are merged. So, if you created a catalog from a CAD system, you can easily add vendor, cost, and other business information later. Check more information –An Ultimate Guide How To Import Catalog Data to OpenBOM and this video (although the video is old, the function is operating in the same way).
Conclusion:
Your product database in OpenBOM is as good as the set of catalogs you organized. The classification of data, defining correct attributes, and importing data from existing data sources (CAD, ERP, Excel, etc) is the foundation of your success with data management using OpenBOM.
REGISTER FOR FREE and get access to your 14-day trial and see how OpenBOM can help you today.
Best, Oleg
Join our newsletter to receive a weekly portion of news, articles, and tips about OpenBOM and our community.