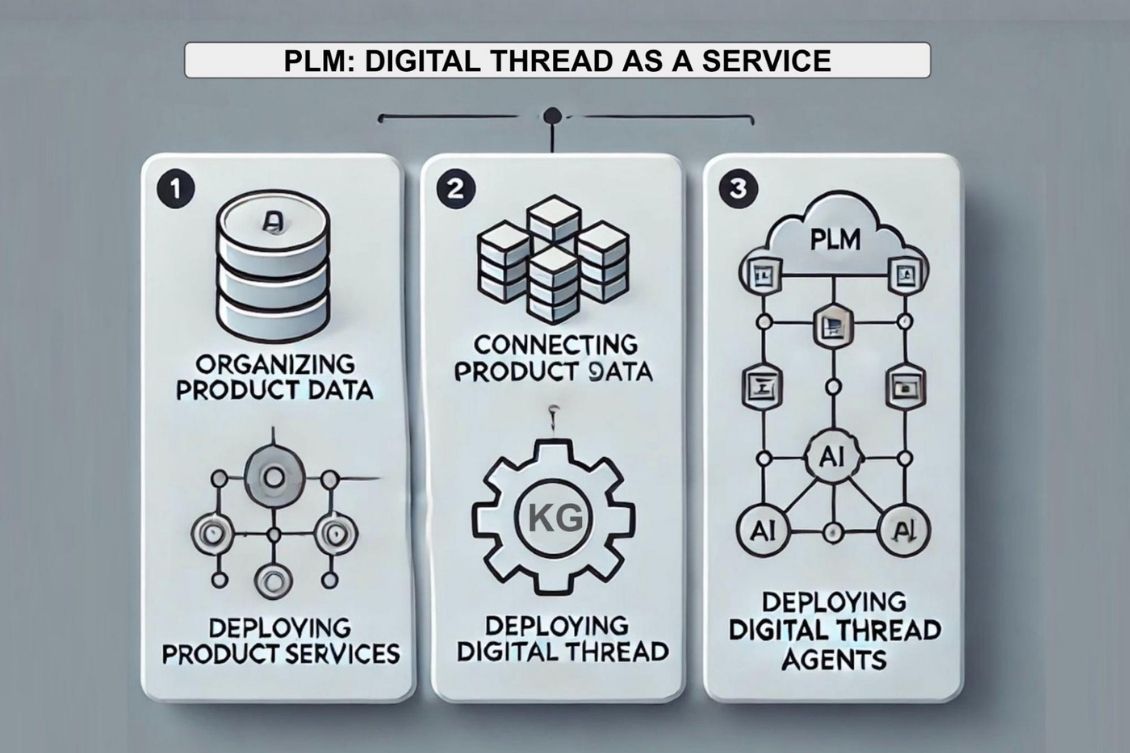
The traditional PLM approach was centered around consolidating all product data into a single, centralized database. This legacy model resulted in massive, monolithic PLM platforms built on SQL databases, attempting to absorb all product-related information into a single source of truth. While this approach was aimed at data centralization, it often led to rigid and complex systems that struggled to adapt to modern engineering and manufacturing needs.
A modern approach to PLM, often referred to as a “single source of change“, rethinks monolithic architectures by identifying various sources of product data and related information and connecting them through a Digital Thread. This method ensures that each piece of data remains in its rightful place, enabling efficient updates while allowing interconnected data to be accessed and utilized for decision-making.
With the increasing complexity of products and supply chains, companies must embrace an agile and scalable approach to PLM. In this article, I will outline three essential steps to planning a modern PLM implementation using Digital Thread as a Service (DTaaS), focusing on data organization, service connectivity, and intelligent process automation.
1. Start with Data: The Foundation of PLM Implementation
The foundation of any PLM implementation lies in data planning. Without a well-structured approach to data management, organizations risk creating information silos, version conflicts, and inefficiencies. To begin, companies must identify and classify data sources, including engineering data such as CAD models, drawings, and design history; manufacturing data such as Bills of Materials (BOM), work instructions, and quality control reports; and supply chain data that includes supplier records, procurement information, and cost structures. Operational data, including maintenance records, field service reports, and IoT sensor information, along with regulatory and compliance data, must also be considered.
Once data sources are identified, a strong data governance framework should be established. This involves defining ownership and responsibility for data management, standardizing data structures, Part Number formats, and naming conventions, implementing access control policies, and ensuring version control mechanisms are in place. Additionally, companies must focus on making data accessible and interoperable by utilizing cloud-based solutions for secure storage, adopting open data standards and APIs for seamless exchange, and ensuring real-time synchronization across departments.
2. Connecting Services: Enabling Seamless Data Integration
After organizing data, the next step is to establish mechanisms for integrating different data sources efficiently. A modern PLM approach leverages connectivity services that enable data exchange across systems, eliminating manual data entry and reducing errors. Engineering data should be automatically captured from CAD systems, both desktop and cloud-based, ensuring design updates are synchronized. Cost management services should pull data from online catalogs, procurement spreadsheets, and contract manufacturing records to provide real-time visibility into product costs.
Here is an example of how OpenBOM connects multiple engineering sources of information together.
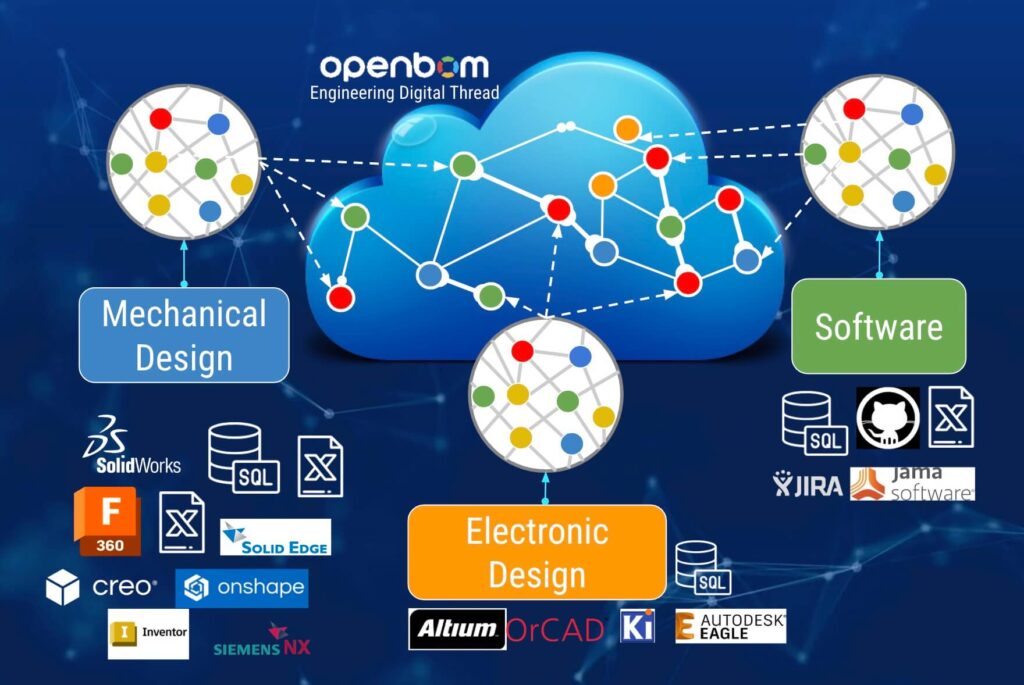
Integration with ERP and Manufacturing Execution Systems (MES) streamlines production planning and execution, while data from IoT-enabled devices, customer feedback, and service reports help capture real-world product performance insights. Compliance updates should be automated to ensure adherence to industry regulations. By connecting these services, companies create a dynamic and interoperable PLM ecosystem that enhances collaboration, enables faster decision-making, reduces errors, and provides the scalability and flexibility needed to adapt to changing business demands.
3. Deploying Digital Thread Agents: Automating Intelligent Processes
To optimize PLM processes, companies should implement Digital Thread Agents—intelligent services that perform specific tasks within the PLM ecosystem. These agents automate various functions, such as design reviews, cost calculations, supplier selection, impact analysis, and predictive maintenance. Design review agents validate engineering data, flag inconsistencies, and ensure compliance with standards. Cost calculation agents analyze materials, supplier costs, and manufacturing estimates, providing real-time insights into expenses. Supplier selection agents automate vendor comparisons based on quality, cost, and delivery timelines, improving procurement decisions.
Impact analysis and change control agents assess how modifications in one area affect the entire product lifecycle, helping organizations reduce risks and delays. Predictive maintenance agents leverage IoT data and AI to foresee potential failures and optimize maintenance schedules. These digital thread agents automate repetitive tasks, enhance data-driven decision-making, and introduce AI-driven automation to streamline workflows and improve efficiency. Their modular nature allows companies to deploy specific agents as needed without overhauling the entire PLM system, ensuring enhanced traceability and compliance tracking.
Conclusion
Modern PLM implementation follows DTaaS principles, allowing companies to build PLM solutions in an agile and scalable manner. Instead of relying on monolithic, legacy PLM platforms, organizations can achieve greater flexibility and efficiency by adopting a modular, service-based approach. The key to successful implementation lies in structuring product data, integrating multiple systems and services, and deploying digital thread agents to automate and optimize processes.
By embracing these modern PLM strategies, companies can create a flexible, collaborative, and intelligent PLM environment. This approach not only enhances operational efficiency but also enables organizations to respond quickly to market changes, drive innovation, and maintain a competitive edge in the digital era.
REGISTER FOR FREE and check how OpenBOM can help.
Best, Oleg
Join our newsletter to receive a weekly portion of news, articles, and tips about OpenBOM and our community.