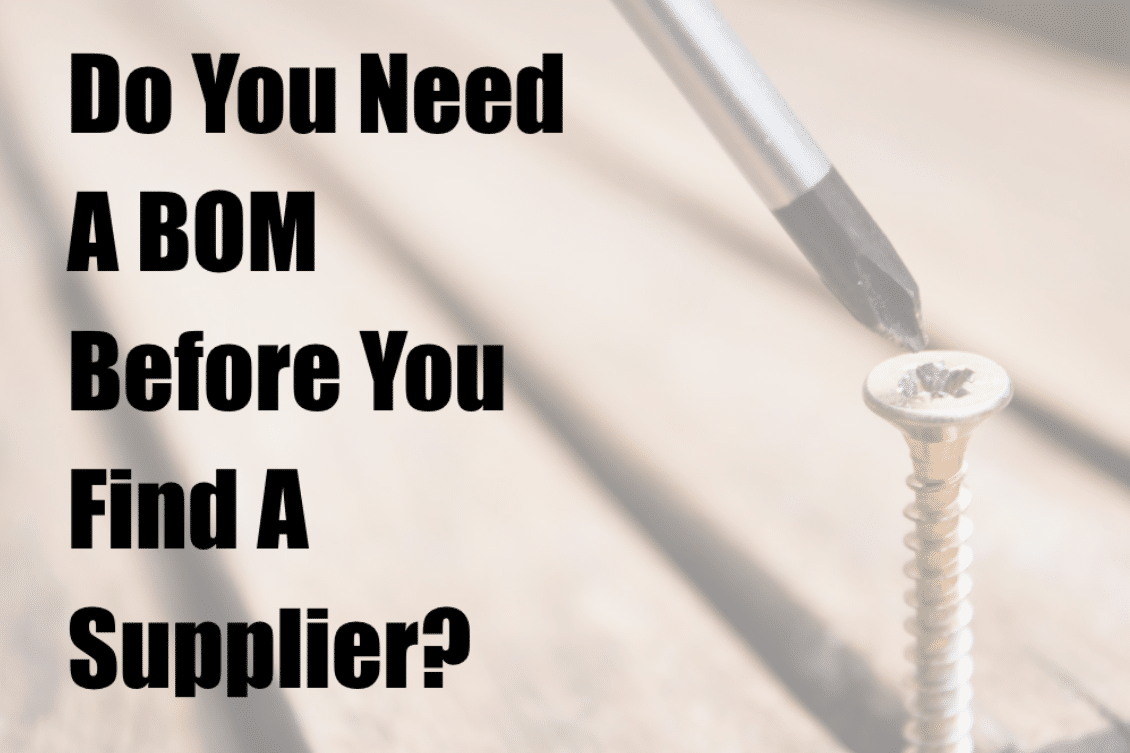
During the final stages of development, manufacturers need to figure out when to start evaluating suppliers. The question always comes up of when should I approach a supplier and what I need to provide them.
For companies looking to turn their innovative ideas into physical products, there are a few things that you need before you start talking with a supplier, one is your Bill of Materials (BOM). The importance of a BOM during production is the same as having a recipe when cooking. If you are not using a recipe then how are you going to confirm the quality of what you just made?
In this blog, we will explore why having a BOM is an important part of your journey with evaluating suppliers and why it becomes an important tool when collaborating with your CM. We will go into the advantages of having the BOM as well as the risks of trying to find CMs without having a BOM.
Approaching a CM
When a manufacturer evaluates a CM, they typically have several key goals in mind. These goals are crucial for ensuring a successful partnership. These goals also help the manufacturer to decide who they would prefer to work with.
So, it’s important when you are discussing your project with them that you are able to provide as much info as possible. To support efficient communication, you can hand over multiple documents, one of them being the BOM.
Here are some of the goals of approaching CMs.
Assessment of Capabilities
One of the foremost goals is to assess the CM’s capabilities. Manufacturers want to understand if the CM has the necessary infrastructure, equipment, and expertise to produce their product efficiently and to the required quality standards. This evaluation helps in determining if the CM is a suitable fit for the manufacturing needs. If the CM is able to view the BOM then they will know based on the materials and processes whether they can support you.
Cost Estimation
Manufacturers seek to obtain a clear and accurate cost estimate for the production of their products. This includes not only the per-unit manufacturing cost but also any additional costs such as tooling, setup, and non-recurring engineering fees (NREs). A transparent cost breakdown is essential for budgeting and decision-making.
Quality Assurance
Ensuring the product meets quality standards is a top priority. Manufacturers aim to evaluate the CM’s quality control processes, certifications, and track record. They want to be confident that the CM can deliver products that meet or exceed their quality requirements.
Communication and Collaboration
Effective communication and collaboration are key goals. Manufacturers aim to establish clear lines of communication with the CM, ensuring that both parties can collaborate efficiently throughout the manufacturing process. This includes discussing project milestones, reporting, and issue resolution.
By approaching a CM with these goals in mind, manufacturers can make informed decisions about supplier selection and establish a productive and successful partnership for their manufacturing needs.
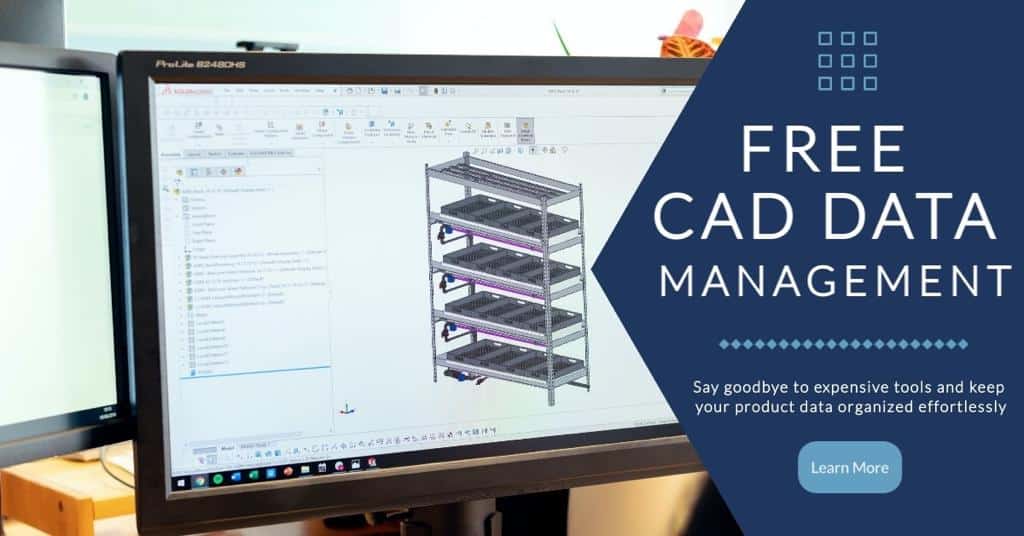
What Does the BOM Provide During the Evaluation Stage?
Approaching a CM without a BOM is generally not recommended, especially for complex or customized products. If you are searching for an original design manufacturer (ODM) supplier then it can be ok. However, if you are looking for an original equipment manufacturer (OEM) or a CM then you’ll need to provide your BOM.
Having a BOM is crucial for several reasons:
Clarity
A BOM provides a clear and detailed list of components and materials required for your product. It serves as a blueprint for your project, ensuring that both you and the CM have a common understanding of what needs to be manufactured.
Accurate Quoting
CMs rely on BOMs to provide accurate quotes for manufacturing your product. Without a BOM, it’s challenging for the CM to estimate costs, leading to potential pricing inaccuracies and budgeting issues.
Efficient Collaboration
A BOM serves as a foundation for effective communication and collaboration with the CM. It minimizes misunderstandings and misinterpretations, helping both parties work together more efficiently.
Risk Assessment
A well-prepared BOM can help identify potential risks related to component availability, sourcing, and quality. Without it, you may be less equipped to assess and mitigate these risks.
However, in some early-stage or less complex projects, you might initially approach a CM without a fully detailed BOM, especially if you’re in the exploratory phase and are seeking preliminary estimates. In such cases, you should at least have a rough list of components and specifications to provide the CM with a basic understanding of your product.
Still, as the project progresses, it’s crucial to develop a comprehensive BOM to ensure the manufacturing process proceeds smoothly, costs are accurately estimated, and quality standards are met. Ultimately, having a well-prepared BOM is a best practice that significantly enhances your chances of a successful partnership with a CM.
Risks Of Approaching A CM Without A BOM
While manufacturers might start the very early stage evaluation process without a BOM, as talks proceed, you’ll need to share additional product data to see whether or not the supplier can support you. The longer you go without proving a CM, the longer you wait to figure out whether the supplier can help with any design for manufacturing (DFM) and production.
Here are some common risks of proceeding without providing a BOM to your CM.
Inaccurate Quoting
Without a BOM, it’s challenging for the CM to provide an accurate quote for your project. This can lead to pricing discrepancies, potentially causing budget overruns or unexpected.
Miscommunication
A lack of a BOM can result in miscommunication between you and the CM. Misunderstandings about component choices, specifications, or quantities can lead to errors in production.
Reduced Negotiating Power
A well-prepared BOM allows you to negotiate with CMs more effectively. Without one, you may have less leverage in price negotiations and contract terms.
Not having a BOM when approaching a CM increases the risk of misunderstandings, delays, budget overruns, and quality issues. It can also hinder effective communication and collaboration between you and the CM. To mitigate these risks and ensure a smoother manufacturing process, you should provide your CM with your BOM.
What Can You Do Today?
As we know, having a BOM is important. However, creating a BOM can be difficult, especially if you have multiple CAD systems and parts have gone through multiple iterations. Manufacturers try to use spreadsheets but quickly find that a lack of traceability and sharing capabilities creates more problems. This has led to the evolution of digital BOMs.
OpenBOM is a cloud-based PDM, PLM, and ERP platform to manage your engineering and manufacturing data. Companies from startups to Fortune 500s use OpenBOM to create a centralized database to bring in, store, and manage their manufacturing data. With this infrastructure, users also use OpenBOM to streamline both their change management and PO processes.
Regards,
Jared Haw
Join our newsletter to receive a weekly portion of news, articles, and tips about OpenBOM and our community.