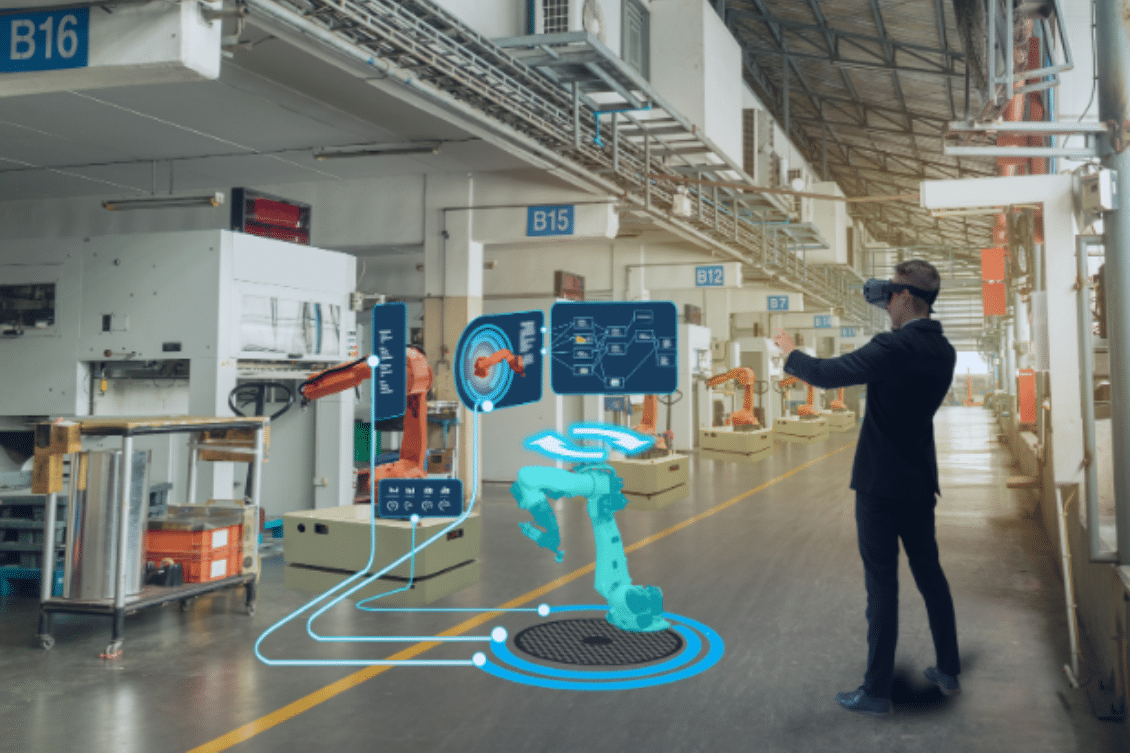
At OpenBOM we help manufacturing companies to organize their data and processes to streamline their engineering and help them to design and manufacture products and provide services. We developed a comprehensive way to help companies to onboard with OpenBOM, learn fundamentals, and start using OpenBOM to manage each company’s processes. There is one topic that no doubt leads in all training and onboarding meetings – part numbers. I always find it fascinating to see how part numbers can lead to so many debates, confusion, and even conflicts in engineering data management systems and product lifecycle management.
In my article today, I want to dig deeper into the details of the intersections between data management systems and part numbers. I will explain why, I think, the topic of Part Numbers sounds very simple and straightforward to some people and, at the same time, can take hours and days of discussions and debates. I will try to explain why some people are blaming product lifecycle management and modern data management systems for introducing the “Part Number Problem”.
This is only the first article about Part Numbers and data organization. Later this week, I will post more about it and will speak about how to deal with part numbers in multiple systems and how to organize and manage multiple part numbers such as Manufacturing Part Numbers, Engineering Part Numbers, Supplier Part Numbers, and others.
The History of the Debates and Why It Is A Complex Topic
In the world of manufacturing and engineering, effective data management is crucial for streamlining processes and ensuring seamless operations. A very basic thing when we communicate is to be able to refer to objects (documents, physical objects, and later more abstract objects) by their names. This is how part numbers first were introduced. Back in the days of paper drawings, the number was first placed by an engineer (or drafter) who created the drawing and released it in the system. It was a very formal process in most large organizations. It was not well organized in smaller companies. I remember how manufacturing people were saying that “the most updated BOM is on the corkboard on the shopfloor” – it was the place where you were able to see the list of all components and production planning.
The evolution of product lifecycle management, enterprise resource planning, and all data management systems and data management platforms created a need to formalize the Part Numbering system. As business processes needed more sophistication and companies were moving to more digital data (first in the way of documents) and later to be used in each data management platform in the organization, the question of what is a Part Number and how to manage it became more important.
And this is why it drives so many debates. My Beyond PLM article last week – Why intelligent part numbers must die in the future of PLM and ERP was generating tens of thousands of views and hundreds of comments – something that I totally didn’t expect and it was a great indication that data management is still not simple and enterprise data and product data management requires more education and discussion.
So, let’s move forward and understand the three levels of Part Number management complexity and why it is something that confuses many people when they manage data using PDM, PLM, ERP, and other systems.
Identification and Classification
At the core of this data management foundation lies the proper data identification. Everything should have a name (or ID). It will be very hard to manage information and physical objects without being able to refer to them by some name. We refer to people by names and sometimes by last names. However, organizations create internal numbers and so does the government when giving us different IDs (Driver’s license #, Passport #, and other identifications). The core element of part number complexity is to be able to perform 2 functions:
- Identify any specific part (it can be an abstract part that is still designed by an engineer, but it can also be a specific physical part that is installed in a product used by a specific customer)
- Describe a part from a different perspective (usually called classification, which can be a very complex process of defining all parameters that needed to be defined)
The two functions (identification and descriptions) are not as simple as you can think because they have multiple touchpoints in any organization (and in modern days also outside of the organization with contractors, suppliers, and customers). And it leads to complexity. Very often it starts with the attempt to “kill all birds with a single shot” by trying to figure out how to manage data using multiple systems and also how to make data easy to understand without any system just by looking at the Part Number.
A methodology that will allow you to create both data management systems and provide an ability to understand any item (part, assembly, material) without touching the data management system would be ideal. But, unfortunately, it doesn’t exist (yet). And this is where your team will have to figure out a compromise between how to manage data in all data management systems – PDM, PLM, ERP, MES, CRM, etc and at the same time to satisfy the needs of people that would like to understand that S9A-00445-A0 is actually a “special assembly” with a product group “9”, part number – “00445” and it is revision “A0”. Speaking from experience, the simpler you go, the better and simpler will be to organize the data and processes in a company and also to organize processes with contractors and suppliers.
Legacy Data and Part Numbers
When you start a new company, you have a few minutes before some kind of data will be created. You still have some time before you make a product and ship it to your first customer or send your drawings to contractors or suppliers. But, very fast, whatever you do is quickly becoming a legacy you need to deal with.
Once created, Part Numbers and associated information live years and decades within the organization. Legacy data introduce a very complex problem because every change you like to do will demand you to comply with the legacy, existing customer information, regulatory requirements, old data capture, support issues, and other product-related data.
Therefore data management is hard and requires you to organize a balancing act and compromise between “old ways” and “new ways”. The best way is to put an old part numbering system at rest and start from scratch, but it is not always possible. I wish I’d have magic glasses that will allow me to see all data I want to know just by looking at a part, drawing, manufactured objects, and products that have already shipped to customers. But this ideal world is not built yet.
Therefore, you will need to agree on how to deal with all legacy numbers and identification mechanisms available in the company. The goal is to build a simpler and more scalable identification system that will help you to simplify the processes. In some cases, I’d recommend the process of data migration. cleaning data and transforming it into a new system. We will talk about it later.
References in External Systems and Processes
The days when everything was done in a single place are gone forever. No one is even trying to make all parts and assemblies in a single place. Manufacturing space is a global network or suppliers and their relationships, which brings a question of how to manage information “across the boundary” or supply chain. Nowadays, it also includes the ability to manage information about specific products used by a specific customer (eg. a car and soon all smart devices we put in our houses).
Fundamentally, this process must address the issue of how to reference data in external systems such as manufacturer number, supplier number, etc. It is a way to go to an outside system and find information in a unique and reliable form.
A typical way to resolve this problem is to be able to extend each item identification with some additional – numbers, names, and parameters that will help to maintain the link and to refer information in a consistent way. Establishing clear protocols for translating and mapping external references to internal part numbers becomes crucial to maintain consistency and data integrity across different entities.
Conclusion
Part numbers serve as a fundamental element in the data management foundation of manufacturing and engineering organizations. They enable proper identification, classification, and data exchange, making them essential for streamlined processes and accurate data management. These three elements of part number management complexity—identification systems, legacy data, and external references—highlight the challenges industrial companies are facing to manage data in an accurate and consistent way. Addressing these complexities requires careful planning, analysis, and collaboration to ensure that part numbers are effectively managed and aligned with the organization’s data management goals.
Getting part numbers right is of the utmost importance in managing data and organizing processes. It minimizes errors, improves efficiency, and enhances data exchange within the organization and with external stakeholders. By recognizing the significance of part number management and investing efforts into its proper implementation, manufacturing, and engineering organizations can lay a strong foundation for effective data management, leading to improved productivity and streamlined operations.
REGISTER FOR FREE to learn more about how OpenBOM can help
Best, Oleg
Join our newsletter to receive a weekly portion of news, articles, and tips about OpenBOM and our community.