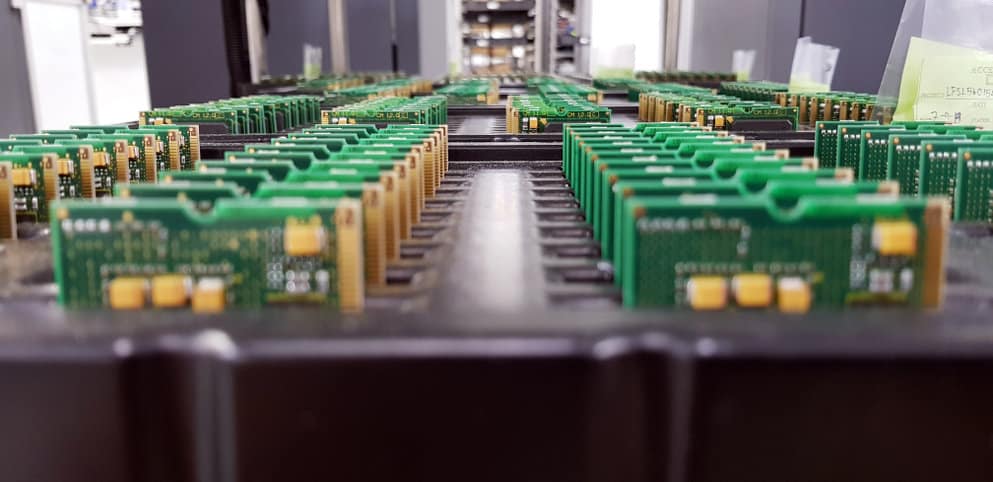
In order to have a successful manufacturing process, it is important to have a design that takes into account the constraints and goals of manufacturing. There are three main goals of Design for Manufacturing (DFM): reducing waste, reducing cost, and improving quality. In this blog post, we will discuss each goal in more detail and give examples of how DFM can be used to achieve them.
If you are developing a product, there are some steps you need to take before you create a prototype and hand it over to your contract manufacturer (CM) to build it. One important step is design for manufacturing (DFM).
According to Quality-One, DFM “enables a product design to be efficiently manufactured and easily assembled with minimum labor cost. Through the use of DFM/A, a company can prevent, detect, quantify and eliminate waste and manufacturing inefficiency within a product design.”
By this definition, DFM looks to accomplish three things:
- Improve the manufacturing feasibility of a product.
- Reduce the overall costs of the product.
- Improve the overall quality of the product.
Let’s further break these down and look into the goals of each part.
Improve the Manufacturing Feasibility
The goal of this part seems quite simple and straightforward. Look into each part and optimize it to be fabricated or assembled.
For each type of component, you will need to look at different aspects. For example, if you are designing a plastic part, you will need to keep in mind the importance of the tool design. Meaning if your tool is not properly designed then the part that comes from the tool will have a number of problems. For the manufacturing feasibility of a plastics part, you need to review the following parts:
- Draft: Mold drafts are needed for part removal. DRMPro suggests 1.5 degrees for a depth of 0.25mm.
- Ribs: If not designed correctly, you will have manufacturing and quality-related problems.
- Shrinkage: Different plastics have different shrinkage rates. The cooling design in the tool also affects shrinkage and warp. When designing the part, take into account the type of plastic you will use during production.
- Wall thickness: Look for consistency in wall thickness
- Gates: The rule of thumb is to have the gates at the thicker parts and have the material run off into the thinner areas. These also affect the appearance of the product.
For other processes, you can look at the following:
- What kind of screws will be used? Using magnetic screws during assembly will improve the assembly speed.
- Analyze the different types of adhesion. For plastics, would ultrasonic welding be the preferred option?
- To reduce overall assembly, can you combine parts or sub-assemblies?
Reduce the Overall Costs
Odds are, when you hand over your manufacturing data to your CM, you will request them to look at initiating a cost-down project. Your CM will look into each individual part or purchased sub-assembly and look into ways to make the part cheaper to fabricate, procure or assemble. To see an overall plan of a cost-down project, I would recommend this article.
To accomplish reducing your price during DFM, you can look at the following:
- Material: Can you use a more cost-effective material for your product. Over-engineering a product will drive up the cost.
- Assembly: For assembly, you will look at the types of adhesives that are used, the types of screws (again, magnetic screws will speed up assembly), etc…
- Process: Some manufacturing processes are geared towards smaller production runs, while others are more favorable for larger production runs. Maybe you started off with lower volumes and then when you scale up production, you need to analyze your fabrication processes.
Improve the Quality of the Product
The last goal of DFM is to improve the overall quality of the product. Each part, whether it’s fabricated in-house or procured from a supplier, has a certain level of risk associated with it. The goal is to identify the risk and design the part to minimize any potential risk of having quality-related issues.
Some parts to look out for to achieve a high-quality product that is repeatable during the manufacturing process are the following:
- Assembly: Are there any parts that can not be assembled?
- Structure Weaknesses: This will need to be addressed for both the part and tooling.
- Material Specification: Are all the materials specified the ideal choice for the environment and application of the product?
- Repeatability: The goal of manufacturing is to have consistent output. If there is a part of the manufacturing process that can lead to an inconsistent product then you will have quality, pricing, and lead time issues.
What Can You Do Today?
During the DFM process, there will be multiple revisions and change requests that must be managed. It is easy to lose historical data or fail to share changes with the correct team members. A centralized platform that connects your team, contractors, and suppliers is your solution.
OpenBOM is a cloud-based platform to manage your engineering and manufacturing data. Companies from startups to Fortune 500’s use OpenBOM to create a centralized database to bring in, store and manage their manufacturing data. With this infrastructure, users also use OpenBOM to streamline both their change management and PO processes.
If you need to improve the way you manage your data and processes, contact us today for a free consultation.
Regards,
Jared Haw
Join our newsletter to receive a weekly portion of news, articles, and tips about OpenBOM and our community.