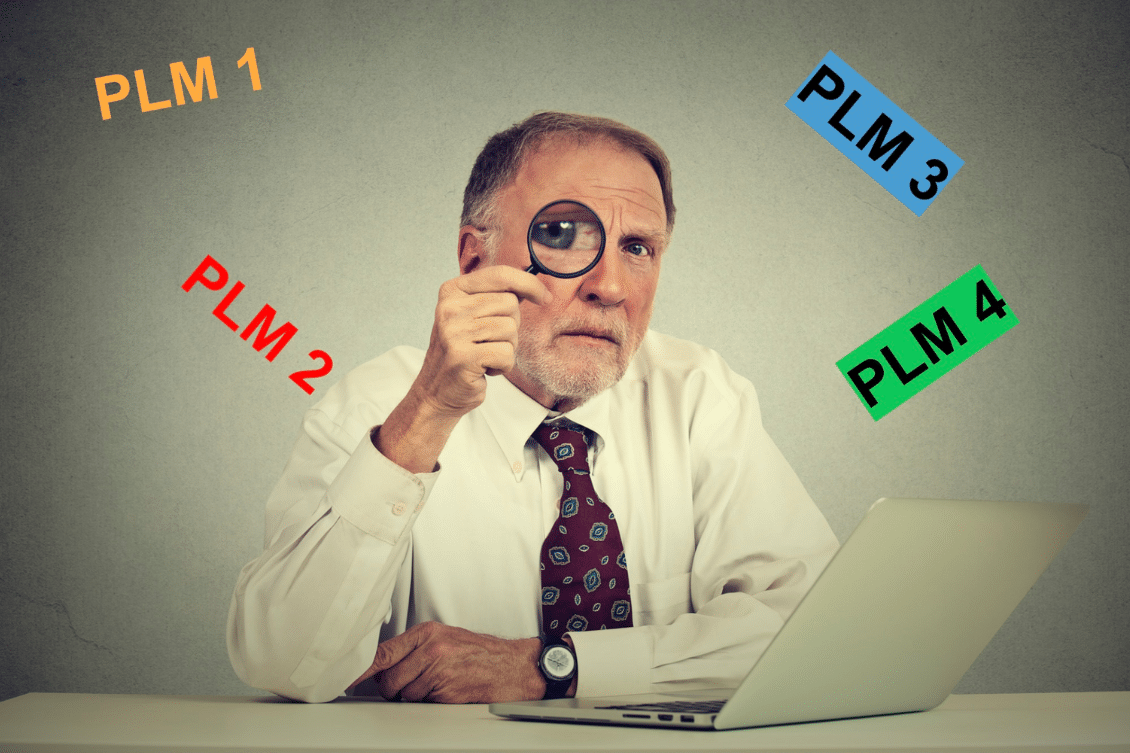
For a very long time, Product Lifecycle Management (PLM) was recognized as a solution for large companies. This is where PLM was born, with companies building aircrafts, cars, and satellites. Things are changing and PLM is becoming more popular and not only among large enterprise companies. You can ask, what changed? The answer to this question goes back to three main factors – (1) an increased complexity of products; (2) the distributed nature of work; and (3) unprecedented demand for speed.
How to build complex products faster with an optimal cost? I think many engineering and operational managers are asking the same questions while trying to organize the product development process in a way that allows them to manage product information and connect people to optimize their tasks.
The level of complexity that exists today in medical, biotech, robotics, automation equipment, high-tech, medical and complex machinery is unprecedented. All these companies are building complex products that have lifecycle spans in both development timelines and organizational distribution multiplied with supply chain management complexity. Therefore, PLM software and PLM systems are an integral part of many industries, helping businesses manage product data, processes, and the entirety of a product’s lifecycle.
PLM Selection Strategy
Having a strategy when selecting a PLM system is important. Although you might find many options to select PLM system, when it comes to the real selection, companies are selecting from a dozen products and after additional slice and dice, focus on 3-4 systems that fit their needs. In my work with many customers, we found that elements of an unstoppable PLM playbook can be used to go from an abstract set of requirements to specific needs your company has.
People
Starting from people is always the right way to do anything, The same is true during PLM selection. Don’t run any “garage projects” to select PLM software. You need to come to the users (they are your customers) and check all their needs about document management, process management, production process, document control, and others.
Process
There are so many ways to do the same tasks. Working with manufacturing companies, I found “process” thinking to be easy to explain. However, you need to have your process drawn on paper (electronic or physical) to make an assessment of how your company is actually supposed to work during the product development process and manufacturing. Have your team to agree on how to work is extremely important..
Technology
It comes last, but important. I suggest companies look at how these goals and processes can be implemented, the technology might be different. Keep in mind that simplicity works and whatever technological solution you choose, simplest will be the best.
Shortlisting
Once you analyze the requirements, technology, and process, you should be able to perform a list of candidates that match your needs and give you an option to start the evaluation process. Here are three criteria to put PLM software vendors to the shortlist:
- Look for PLM providers with a good reputation in your industry.
- Read reviews, ask for recommendations, and attend industry events or webinars.
- Shortlist options based on the fit with your requirements and budget.
- Check the availability of the trial
The last point is really important. In 99% of situations, I’d be really uncomfortable if the PLM software is not available for trial. You should get a 2-4 weeks trial from any vendor these days, to get the “feeling” of the product and support process.
Are you selecting PLM software that will be used for decades?
Although long vision is really important, the reality of system selection will eventually put a question in front of you – what period of time this PLM software should serve us?
Here is my take. Between selecting (1) the right solution for the current stage of the company and choosing (2) a dream for the bright PLM future, I prefer the first option. I prefer PLM strategy be built before the vendor comes and pulls you into long discussions about PLM implementation. A phased approach is the best and to have a strategy for 2-3 years is the ideal time horizon for the current industry situation. Start from small and build a roadmap for success.
Other Elements of the PLM Selection Process
There are several elements of the selection process that must be taken into account after you solve the first three – (1) selecting a strategy; (2) shortlisting; and (3) implementation. Here is a list of topics that eventually will come during your decision process and some of my comments on that.
Consider Scalability
Although, thinking “long term” can lead you to an endless number of options and solutions, the system you select should support it for a few years. Scalability should include elements of multi-user support, cloud technologies, capacity, and user operation.
Prioritize User Experience
Check user experience multiple times, show it to your internal customers, and you will need to perform user experience trials. A user-friendly interface can speed up adoption rates and reduce training time. Consider systems that are intuitive, have an easy learning curve, and offer effective support and training resources.
Flexibility
Can the PLM system be customized to suit your unique processes? A one-size-fits-all solution might not be the best for complex or specialized operations. Ensure there’s flexibility to adapt as your business evolves.
Assess Implementation and Support
Although many large implementations even today are done by service teams the implementation process can be long. How long will the implementation process take? The quicker you can integrate the PLM, the faster you can start reaping its benefits. Ensure the PLM provider offers robust support – both during and post-implementation.
Extra Cost and Issues
Beyond the initial purchase or subscription price, consider costs associated with training, support, customization, and potential future upgrades. You should end up with the right TCO in your hands.
Conclusion
Selecting a PLM system is a significant decision that can influence your company’s operations for the next few years and help you to achieve strategic company goals.
By being thorough in your research, involving relevant stakeholders, and prioritizing your specific needs, you can choose a PLM that minimizes stress and maximizes your organization’s success.
REGISTER FOR FREE and start a 14-day trial to evaluate how OpenBOM can help you.
Best, Oleg
Join our newsletter to receive a weekly portion of news, articles, and tips about OpenBOM and our community.