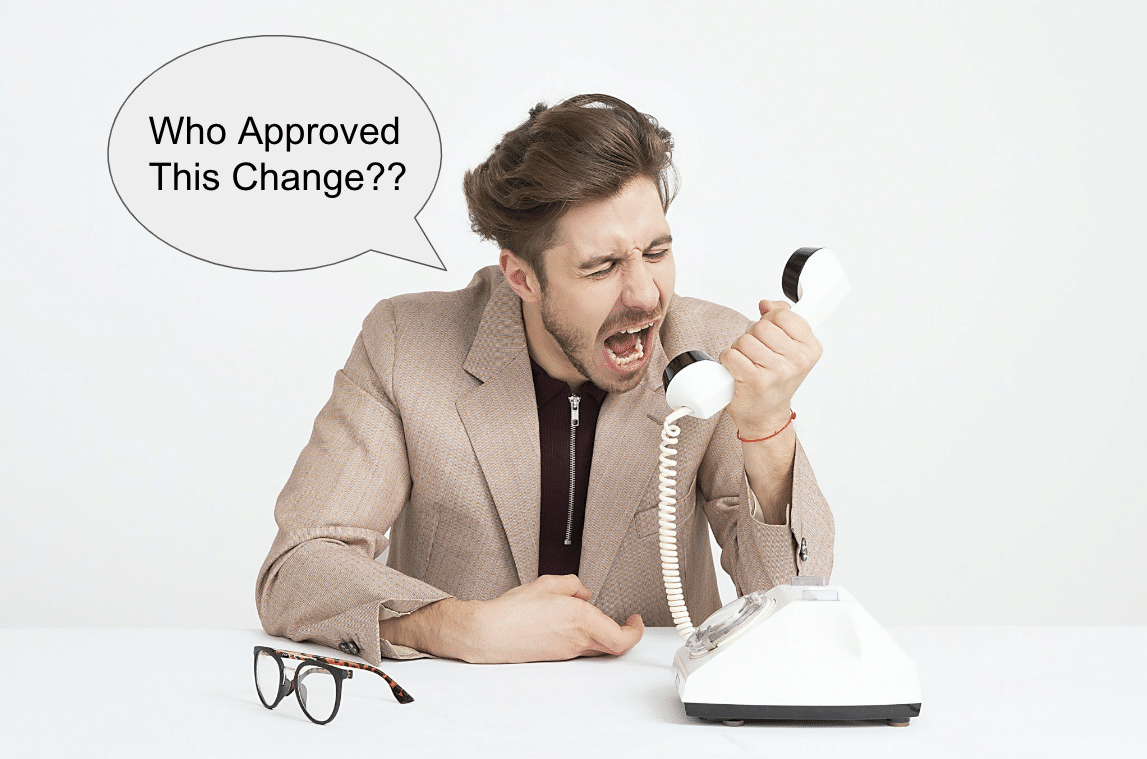
Throughout the life of a product, there will always be changes. These changes might come during development, or they might come during production. At whichever stage, you need to decide whether you will control these changes or your contract manufacturer (CM) or supplier will control these changes.
Changes in Development
During the request for quotation (RFQ) process, the product is most likely not optimized to be manufactured. However, it’s good enough to get a quote. The next step is turning the product the CM quoted into a product that can be made. This is what’s done during the design for manufacturing (DFM) stage.
Usually, during the DFM stage, there are multiple change requests. And, this is where the confusion starts. Who takes responsibility for confirming the change requests? And why do these change requests often become approved without an approval process?
Changes in Production
After the product is in production, there will be modifications made to the product. These modifications happen for a number of reasons, some on the CM side, and some on the client side.
These modifications can come up because of the following:
- Improve quality
- Reduce costs
- End-user feedback
Regardless, oftentimes, the process of change requests is not defined. Not having this process defined will lead to one PO not having the same product as the previous PO.
Who Controls Changes?
No matter if the change request happens in development, or in production, there must be a process for these changes. However, sadly enough, there is no process, there are just assumptions.
The process should also be quite straightforward. Anyone can make a request but only a certain amount of people can approve the change request. These approvers are usually on the client side.
While this is straightforward, why is there a misalignment between manufacturing companies and their CM? Here are three reasons that are the most common:
Mindset
These two parties, the CM and the client, have different mindsets. The mindset of the CM is that they just want to make changes to optimize the parts for production. These changes will make the part cheaper and easier to make. The mindset of the CM is thinking that the client will always accept these changes and why wouldn’t they?
While this mindset is beneficial, it can lead to anger from the client’s side.
Communication
The lack of proper communication is such a problem between a CM and their client. I have heard many manufacturing companies say that they control the changes. They also say that the supplier or CM makes changes without them knowing. So, who really controls the changes? These changes were made because of the mindset of the CM. And the client never communicated their expectations to the CM.
Nothing is common sense in the global world of manufacturing. The best way to create a single mindset is to over-communicate. Don’t ever make assumptions.
Lack of Proper Tools/Technology
If you provide your CM with an excel BOM then it’s easy to manipulate. So, maybe you can provide them with a BOM that can not be manipulated. You can digitalize your BOM. Providing your CM with the right tools will not just organize all of your product data but also put all changes through an approval system that is set by you, the client.
Another trusted tool to improve collaboration with your supplier is Cloud PLM.
What can you do today?
Are you looking to set an approval system for changes that have been requested? Adopting a cloud PLM system is the best way to improve the way you work with your suppliers and contractors.
OpenBOM is a cloud-based PDM & PLM platform to manage your engineering and manufacturing data. Companies from startups to Fortune 500’s use OpenBOM to create a centralized database to bring in, store and manage their manufacturing data. With this infrastructure, users also use OpenBOM to streamline both their change management and PO processes.
If you need to improve the way you manage your data and processes, contact us today for a free consultation.
Regards,
Jared Haw
Join our newsletter to receive a weekly portion of news, articles, and tips about OpenBOM and our community.