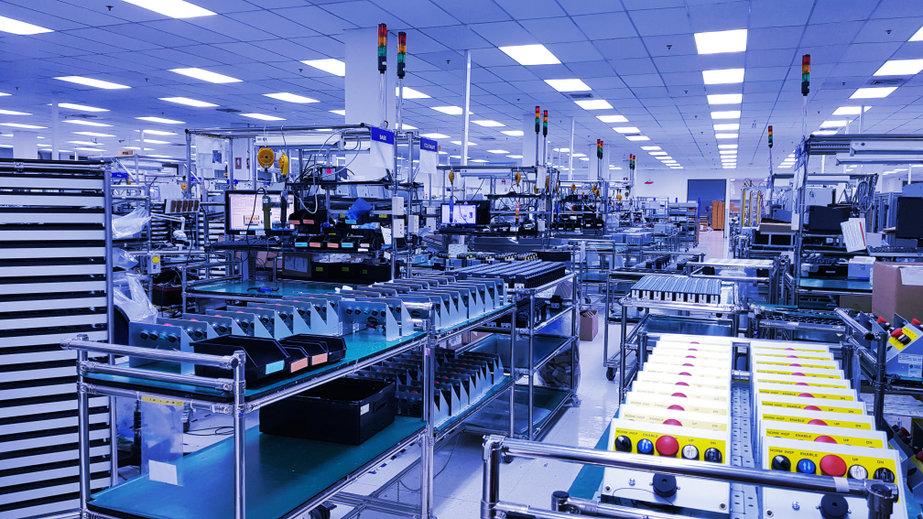
You have just completed a successful product launch and now you are planning to scale up production. Just one thing, we are in the middle of a supply chain crisis and chip shortage. So, how are we expected to make more products during this ongoing crisis? One important part is to find ways to maximize your production capacity.
First, what is production capacity? Jacob Lauzier from MachineMetrics explains that “Production capacity is the maximum output that can be achieved in the production of manufactured goods. It is generally a part-based metric that identifies the most goods that can be created given a set amount of resources (time, labor, materials).”
Overall Equipment Effectiveness
To measure your production capacity, you will need to understand your overall equipment effectiveness (OEE) score. Basically, OEE measures how efficient the manufacturing process is.
OEE was created to support total productive maintenance (TPM) which calls out everyone in the organization to participate in maintenance, rather than just the maintenance team.
OEE looks at 3 parts, Availability, Performance, and Quality.
Availability: Takes into account both planned and unplanned stops. If your score is 100% then this means your production is always running.
Performance: Looks at slower cycle times and shortstops. A score of 100% means your processes are running as quickly as possible.
Quality: Looks at the number of defects your product has that need to be reworked. A score of 100% means all your parts are defect-free.
If your OEE score is 100% then that means your availability, performance, and quality all scored 100%. Highly unlikely. According to Vorne this is what the numbers usually look like.
- An OEE score of 100% is perfect production.
- An OEE score of 85% is world class for discrete manufacturers.
- An OEE score of 60% is fairly typical for discrete manufacturers.
- An OEE score of 40% is not uncommon for manufacturers without TPM and/or lean programs.
The big goal of TPM and OEE is to eliminate what they refer to as the Six Big Losses. If you understand these, you will be able to create actions in order to improve your overall production capacity.
Equipment Failure
If a machine is scheduled to run but it’s not running due to it being broken then you have equipment failure. The most common examples of this will include maintenance that was not planned, a tool that broke, and more.
Setup & Adjustments
This is the amount of time lost when a piece of equipment is scheduled for production but is not running because of either adjustments or machine setups.
The most common example is putting a plastic injection molding tool into a machine. If you have not adopted a single-minute exchange of die methodology then this can take hours to accomplish.
Idling & Minor Stops
Throughout the day, the machine will stop for a couple of minutes. Usually, these occur because of material jams, incorrect settings, cleaning, etc… Most of these will be solved by the operator.
Other issues can result in the operator directly, such as unplanned chats with his/her supervisor or a quick bathroom break.
Regardless of the reason, idling & minor stops are usually less than 5 minutes
Reduced Speed
This is when the equipment runs slower than what it was planned for. Common examples of why a machine will run slower are because it’s dirty, just started the machine, an inexperienced operator, etc…
Process Defects
If production is running as normal, but there is a defective part then this is a process defect. This includes both scrapped parts and parts that can be re-worked.
Reduced Yield
Whenever you start a machine, the output will most likely be lower. This reduced output is known as reduced yield.
If you need to improve your overall capacity then you can start by looking at these 6 losses. Understanding why you are underperforming will help you target where you need to start to improve your overall capacity.
What can you do today?
During the manufacturing process, there will be constant changes and you will need to capture all of these changes. You will also need to share all of these changes with your team, suppliers, and contractors. So, your solution is a centralized platform that connects your team, contractors, and suppliers. This creates a single source of truth and eliminates mistakes.
OpenBOM is a cloud-based platform to manage your engineering and manufacturing data. Companies from startups to Fortune 500’s use OpenBOM to create a centralized database to bring in, store and manage their manufacturing data. With this infrastructure, users also use OpenBOM to streamline both their change management and PO processes.
If you need to improve the way you manage your data and processes, contact us today for a free consultation.
Regards,
Jared Haw
Join our newsletter to receive a weekly portion of news, articles, and tips about OpenBOM and our community.