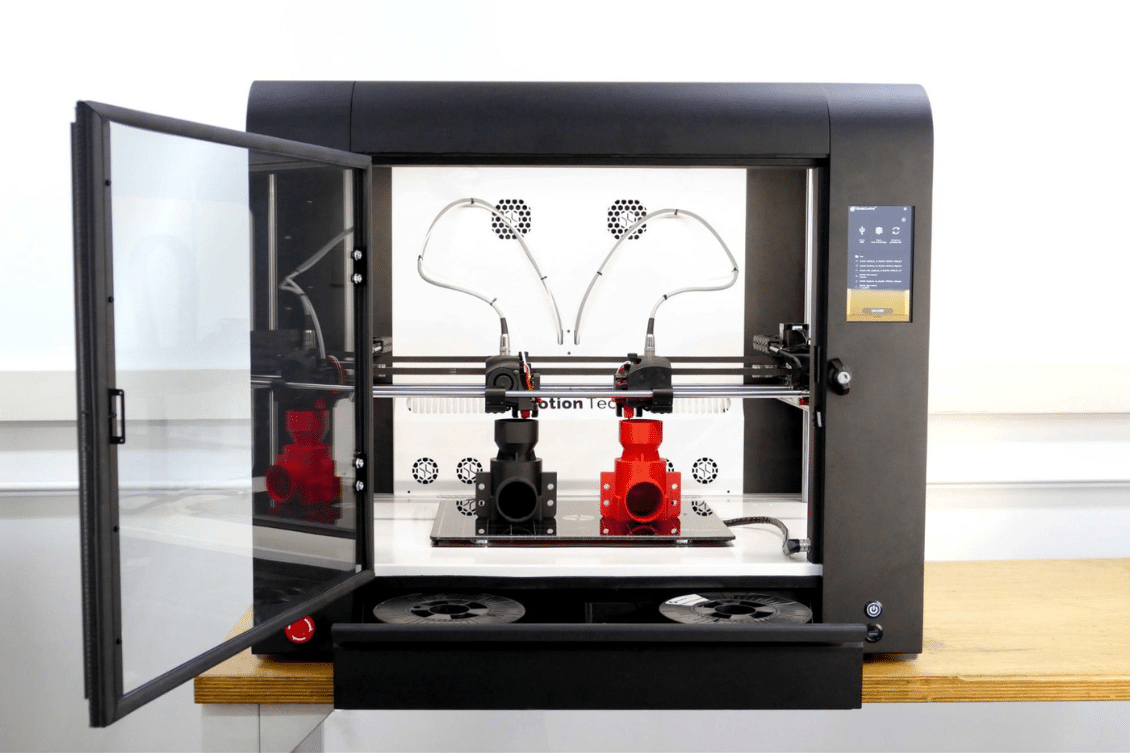
During the product development steps, a few milestones take time to accomplish. One of these milestones is receiving an acceptable prototype. However, once you are able to create an acceptable prototype, you know that you are taking strides forward.
There are multiple different kinds of prototypes. You can have a prototype of the entire product or you can have a prototype of an individual part. It also depends on whether or not you are working with a contract manufacturing partner or if you are working with a prototype shop. Depending on who you are working with will dictate how you proceed. This article will discuss how to go from an acceptable prototype to mass production.
Can I Launch Production Right Away?
A common misconception is that you can launch production after your prototype. The main reason you can’t launch production is that your prototype was made for a prototype, and not made for production. In other words, you can’t replicate prototypes at high volume, and with a good price.
Here are some other reasons why prototypes can not be replicated:
- You can’t scale the prototype processes (such as 3D printing).
- You can’t cost-effectively scale 3D printing processes. The cost to CNC rather than die-cast is significantly higher, same with 3D printing & plastic injection molding).
- You can’t take a design of a prototype part (assuming it’s 3D printed or CNC) and open a tool for it right away. You need to design that part for tooling, this is called design for manufacturing (DFM).
- Can’t replicate without a transfer of knowledge. Usually, during prototypes, the engineer handcrafts it. The operators on the line lack the knowledge of how to assemble the product at first.
The goal of mass production is to reproduce a consistent product, at high volumes, and at the cheapest price. Prototypes on the other hand use more expensive processes because they are faster. Therefore, prototypes sacrifice costs for speed.
Optimize Your Product
One of the most important parts to scale production is to optimize your product for production. The best tool to optimize your prototype for mass production is called design for manufacturing (DFM).
According to Quality-One, DFM and DFMA “enables a product design to be efficiently manufactured and easily assembled with minimum labor cost. Through the use of DFM/A, a company can prevent, detect, quantify and eliminate waste and manufacturing inefficiency within a product design.”
During DFM, you and your team will look at a few ways to optimize your product.
Part Optimization for Mass Production
Making prototypes are made differently than in mass production. As a result, during prototypes, engineers are forced to design parts that might be ok for prototypes but might not be ideal for production and final assembly. Since these processes and steps are not scaleable, certain parts need to be re-engineered.
When optimizing parts for production, these common questions are asked:
- Can you combine some parts?
- Does the part design change when the fabrication process changes?
- Are there existing alternative parts?
Tool and Die Design
Another part that is usually not at the top of everyone’s mind during the prototype process is making tools. However, during mass production, tools are very important because they create consistency and uniformity in a part.
For a plastic part, you have to look at multiple parts of the design. These include drafts, sinks, gates, ridges, ejectors, and more. If these exist then they can jeopardize the quality of the part as well as the appearance. During the prototype steps, you might not worry about these since 3D printing does not have these problems.
Quality
Quality is an art that is ingrained in a product and a company before mass production. If a product is not optimized for production then you’ll have quality problems. Also, if a part is designed without quality in mind then you can expect quality issues.
DFM is performed to minimize the risks of defects throughout the manufacturing process by making modifications to the design.
Price
Reducing the price is another common benefit of optimizing your product. DFM will look at reducing the price by changing the design, proposing alternative components, and changing some fabrication processes.
Also, optimizing your part for production and making the proper improvement for tooling will reduce the price of your product.
Do You Have A Supplier?
This part might depend on how you started your supply chain journey. If you chose your manufacturing partner before or during the DFM stage then this process most likely is not relevant. If you completed DFM and still don’t have a supplier then this is more relevant for you.
Regardless, you need to pass your product data to your suppliers for a quotation. This step is referred to as the request for quotation (RFQ) process. Here are some of the data that you need to pass along to your supplier in order to receive a quote:
- Bill of Materials (BOM)
- Assembly Steps
- Quality Instructions
- Business Case
- A Prototype
- Drawings
After you have evaluated and chosen your supplier you can start to prepare for production. During this stage, you will need to develop and make the following:
- Tools and Jigs
- Work Instructions (WIs) or Standard Operating Procedures (SOPs)
- Quality Instructions
- Assembly Layout
- Training
Do You Have Your Golden Sample?
One of the last steps to transition from prototype to production is to create a golden sample. The golden sample represents exactly what the manufacturer wishes to sell. The golden sample usually uses the same material and production tools as in mass production. So, the only real way to get a golden sample is to have production tools opened.
Once you have a golden sample and the golden sample is acceptable then you know that you can launch production.
What can you Do Today?
When you are launching your product, there will be multiple revisions and change requests that must be managed as you go from prototypes to production. It is easy to lose historical data or fail to share changes with the correct team members. A centralized platform that connects your team, contractors, and suppliers is your solution.
OpenBOM is a cloud-based PDM & PLM platform to manage your engineering and manufacturing data. Companies from startups to Fortune 500’s use OpenBOM to create a centralized database to bring in, store and manage their manufacturing data. With this infrastructure, users also use OpenBOM to streamline both their change management and PO processes.
If you need to improve the way you manage your data and processes, contact us today for a free consultation.
Regards,
Jared Haw
Join our newsletter to receive a weekly portion of news, articles, and tips about OpenBOM and our community.