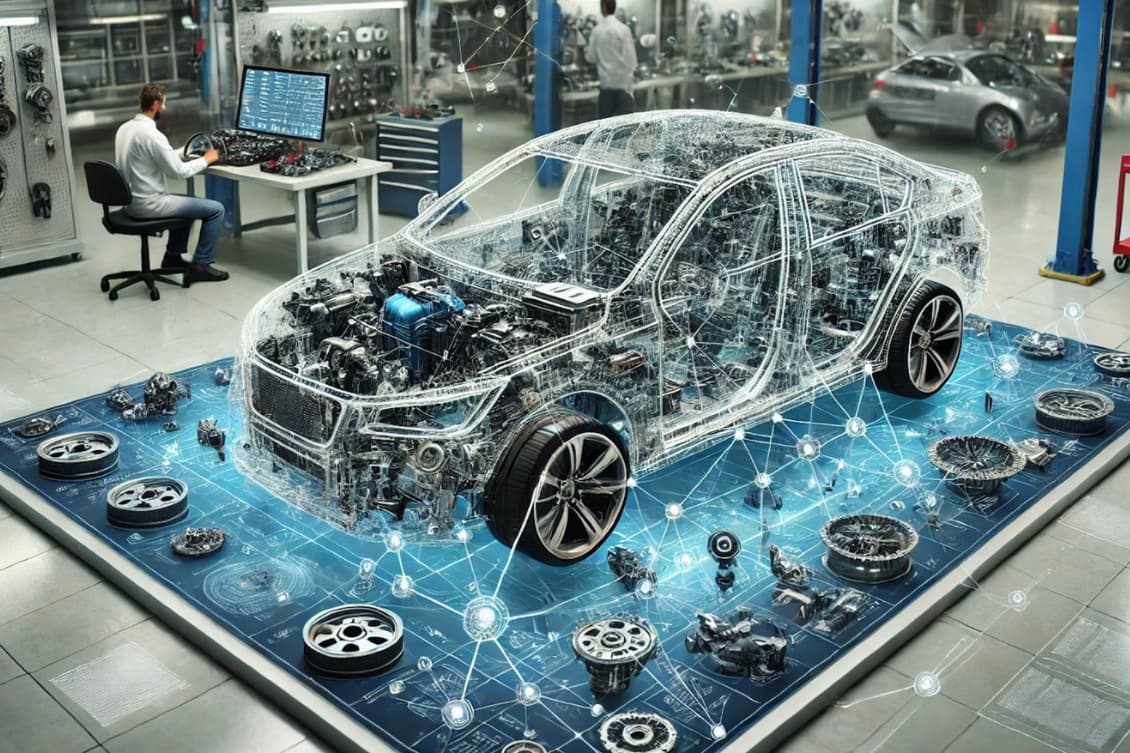
The engineering bill of materials (often called EBOM) includes all information about how a product is designed – components, raw materials, assemblies, etc. It gives you a perspective of the product from a product development side aggregating and accumulating all data defined by engineers.
In the modern manufacturing world, the Engineering Bill of Materials (EBOM) serves as a foundational piece of information within the broader concept of a digital BOM including multi-disciplinary data coming from different design systems (MCAD, ECAD, Software, etc). It is part of a broader concept of multi-view or xBOM. As product complexity increases, the need for specialized BOM structures, such as EBOM, is essential for seamless collaboration between engineering, manufacturing, procurement, and service departments.
Leading analysts in the product lifecycle management space define the future of BOM management related to the so-called multi-view BOM approach that maintains a centrally connected digital graph of information and creates views of specific BOM (EBOM, MBOM, etc.). Let’s talk about it later.
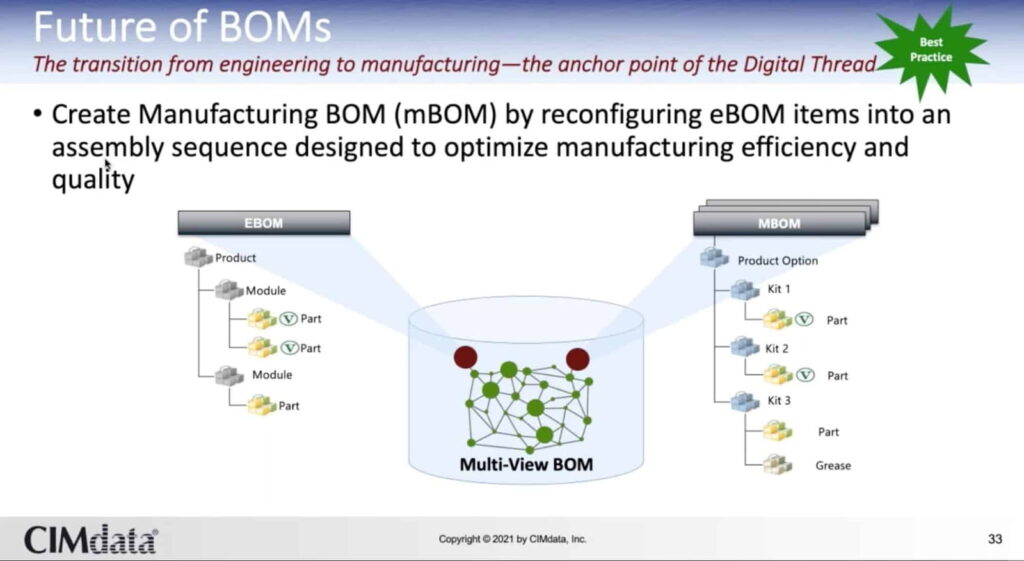
In my article today, I want to talk about what is EBOM, its critical role in the manufacturing process, and the role EBOM plays within overall xBOM. I will also touch on how OpenBOM’s flexible data model optimizes its management across a product lifecycle and how OpenBOM immersive CAD integrations ensure creating and maintaining an accurate engineering bill of materials across multiple disciplines and teams.
What is an Engineering Bill of Materials (EBOM)?
The EBOM is the blueprint for any manufactured product, developed by engineering teams to represent the product’s designed structure, materials, and components. It includes all the parts and subassemblies as defined by CAD models (so-called items). It connects those items to appropriate engineering drawings, and specifications, capturing the technical data needed to build a product. It includes all engineering file derivatives (STEP, PDF, STL, DWG, etc) connected to appropriate EBOM Items. EBOM typically contains component-level data, item numbers, quantities, material types, and design-specific attributes that provide precise instructions on how each part is expected to function.
The importance of the EBOM lies in its focus on the design perspective rather than the production view. It is created to ensure that the product meets engineering and quality standards and supports decision-making around components and subsystem design. The completeness of EBOM ensures that engineers provide all information about the product that is needed to build a product in the correct way and ensure the completeness of the engineering process.
CAD and EBOM – Are They the Same or Different?
This is a question that is often asked by engineers and manufacturing teams. While CAD (Computer-Aided Design) and EBOM (Engineering Bill of Materials) are closely related, they serve distinct roles in the product development process. CAD models are the foundation for creating an EBOM; they visually and geometrically define each part and component within a design. However, the EBOM takes this a step further by translating the design structure into a comprehensive digital data set including all materials, quantities, and part relationships needed for downstream processes.
CAD data alone is insufficient for manufacturing or procurement because it primarily focuses on the geometry and design data relationships, whereas the EBOM includes essential details, such as material specifications, item numbers, and other attributes that CAD software doesn’t track. It also includes all needed derivatives that are typically created from CAD data (eg. STEP, STL, PDF, etc.) This distinction is essential for effective collaboration between engineering and manufacturing teams, as the EBOM bridges the gap between the digital design in CAD and the physical requirements for production, procurement, and beyond.
Why Is It Important to Create EBOM Early in the Product Development Process?
An important element of modern product development is related to the timely management of data related to the product design in the way it is becoming available to all people involved in the process product development – including engineering perspective, manufacturing teamwork, and others.
Therefore, creating the EBOM early in the product development process is crucial. Here are a few reasons why to create EBOM early in the process of product development.
- It establishes a detailed blueprint of the product’s structure and materials, setting a solid foundation for all downstream activities, including procurement, production planning, and inventory management.
- An early EBOM allows cross-functional teams, such as engineering, manufacturing, and procurement, to align on component requirements, identify potential supply chain constraints, and address design or material conflicts before they escalate.
- Additionally, an early EBOM enables smoother integration with other BOM types, such as the Manufacturing BOM (MBOM) and Service BOM (SBOM), fostering a seamless flow of information throughout the product lifecycle.
By identifying the key elements early, teams can iterate more effectively, catch costly errors in the design stage, and ensure the design is production-ready, ultimately speeding up time to market and reducing development costs.
5 Challenges of EBOM Management
While creating an EBOM should be simple, your team can face challenges because it introduces a separate step in the product development process. While your engineers might be dumping CAD data to Excel and transforming it into other data sets used by the procurement and planning team, setting up EBOM will create a new product data quality.
Here are a few challenges typically experienced by teams stepping into a process of EBOM creation from just Excel dumping from CAD systems.
- Maintaining Consistency with multiple CAD data: Ensuring CAD and EBOM are in sync is an important goal and also a big challenge as it requires multiple engineers and systems (MCAD, ECAD, Software, etc) to work together.
- Handling Multi-CAD Data: Modern products are often designed using multiple CAD systems, which means EBOMs need to accommodate multi-CAD data and ensure compatibility. Therefore handling CAD data and transforming it in a cohesive data set representing EBOM can be a challenging task that will force you to change the way you work and sometimes even design product. But it will pay off later.
- Tracking Design and Engineering Revisions: Changes are happening in both design documents (CAD) and Bill of Materials (EBOM). As products evolve, tracking changes and revisions in real-time is critical. To keep EBOM revisions connected to CAD file revisions/ versions and also keep a consistent EBOM connected to other BOMs across the lifecycle is critical. Seamless integration with other BOMs (within the xBOM) needs to ensure seamless integration across the product lifecycle.
- Maintaining Consistency Across BOM Types: Ensuring that the EBOM aligns with the MBOM, SBOM, and other BOM types to maintain data consistency across departments.
- Managing Complex Configurations: Many products today come in multiple variants, requiring an EBOM that can handle configurable and variant-rich designs without adding complexity to the data management process.
How OpenBOM xBOM Service Enhances EBOM Management
At OpenBOM, we put an EBOM process ahead of other priorities. The foundation of OpenBOM digital BOM solution and technology is a data management architecture allowing to support an instance-reference model for product data. It is flexible and powerful.
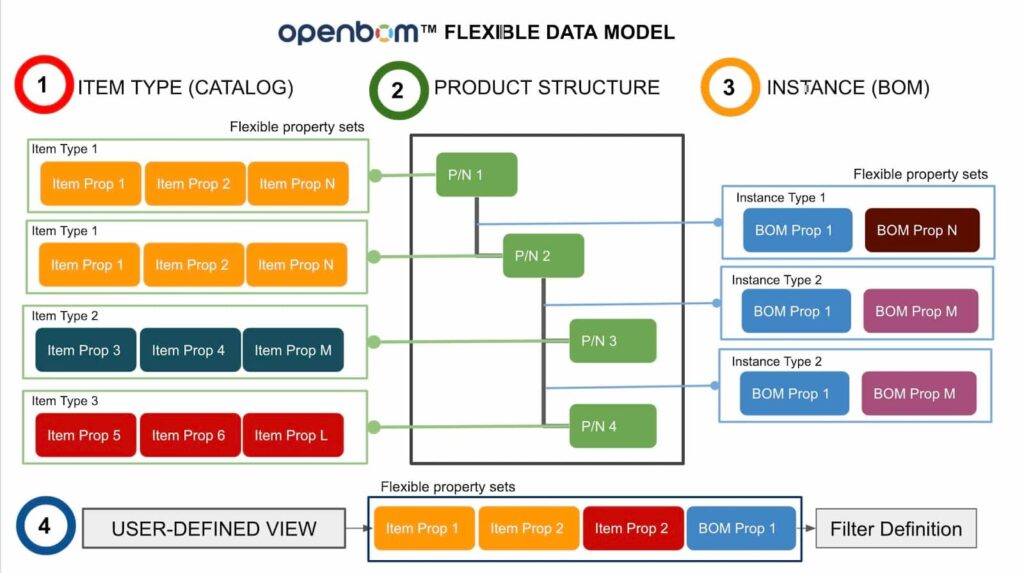
But this is not everything. We’ve been watching ahead some strategic developments such as OpenBOM’s xBOM service, with its flexible data model and multi-view BOM architecture, which addresses the needs of companies to manage multiple BOM types.
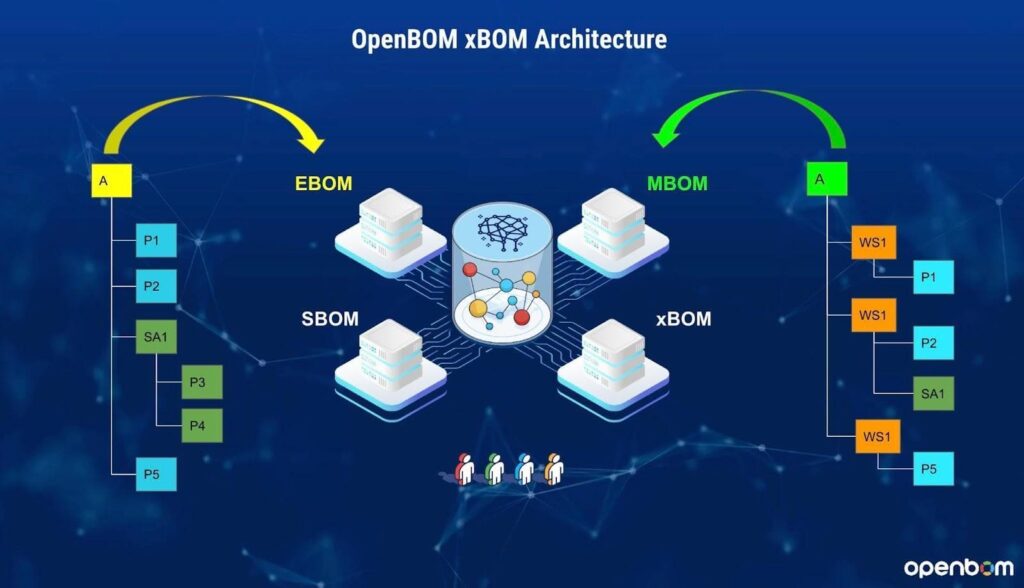
Both mechanisms – digital BOM and xBOM ensure a fully transparent digital data management within the organization. How does OpenBOM do it? Here’s how OpenBOM built an infrastructure to manage information effectively, enabling users to manage EBOMs and other BOM types cohesively.
- Graph-Based Data Model: OpenBOM’s unique graph-based data model allows for an interconnected view of BOMs. The EBOM, MBOM, SBOM, and other BOM types are no longer isolated; they are dynamically linked, creating a single source of truth across engineering and production.
- Real-Time Data Synchronization: OpenBOM enables real-time synchronization between CAD and EBOM and moving to compare and sync process with other BOMs (MBOM, SBOM, etc), ensuring that design changes made by engineering teams instantly reflect in the engineering and manufacturing data. This synchronization eliminates the typical delays and errors seen in traditional EBOM to MBOM handoffs.
- Change and Revision Management: OpenBOM’s built-in change management tools allow users to track revisions and maintain version control across all BOM types within xBOM. Engineering teams can confidently make design updates, knowing the changes will automatically flow through the product lifecycle and inform downstream activities.
- Multi-CAD Integration: OpenBOM supports multi-CAD integration, making it easy to create and manage EBOMs from various CAD environments. So called “One-Click BOM” solution allows you to capture the information painlessly. This ensures that data is accessible and standardized, regardless of the CAD system in use.
- Design Configurations and Variant Management: OpenBOM’s special capability is to capture configurable (design configurations) of the products. It allows you to automatically capture configured data from CAD systems resolving it in appropriate data sets.
The Role of EBOM in the xBOM Structure
EBOM is a part in a bigger picture of xBOM, a complex digital BOM representation covering all aspects of the product lifecycle. In today’s dynamic product development environment, the xBOM approach has become essential. xBOM includes the concept of multi-disciplinary BOMs, representing various product perspectives (Engineering, Manufacturing, Service and Maintenance, and Functional BOMs) to provide a complete picture of a product across its lifecycle.
The EBOM is the first crucial step in the xBOM structure, acting as the starting point from which other BOM types are derived. As the engineering definition of the product, the EBOM sets the foundation upon which downstream teams can build Manufacturing BOMs (MBOM), Service BOMs (SBOM), and more. Within xBOM, the EBOM plays a vital role in ensuring that product design changes, engineering revisions, and design intent flow seamlessly throughout all phases of production, maintenance, and service. The Benefits of Multi-View BOM Management
The integration of EBOM within an xBOM framework provides numerous advantages for engineering and manufacturing teams:
- Enhanced Collaboration: xBOM enables cross-functional teams to work on different aspects of the BOM without data silos. Engineering teams focus on EBOM, while manufacturing and service teams utilize MBOM and SBOM, all within a connected ecosystem.
- Reduced Errors and Rework: By maintaining a consistent link between EBOM and other BOM types, xBOM helps reduce errors arising from manual data transfers and updates. This leads to fewer production delays and rework incidents.
- Faster Time to Market: With an interconnected xBOM environment, design changes propagate faster to manufacturing and service teams, accelerating the product lifecycle and reducing the time to market.
- Improved Data Accuracy: A single source of truth ensures that every department accesses the most up-to-date information, reducing discrepancies and improving overall data accuracy.
How EBOM, MBOM, SBOM, and Other BOMs Work Together
The Engineering BOM (EBOM), Manufacturing BOM (MBOM), and Service BOM (SBOM) each represent different views of a product but are interconnected within the broader xBOM framework to support its entire lifecycle. The EBOM, created by engineering, defines the design intent, listing components and materials based on the CAD model.
This engineering view then informs the MBOM, which adapts the design for manufacturing by considering production processes, tooling, and assembly requirements. The MBOM often includes additional details, such as bulk materials, consumables, and order-specific configurations that are essential for manufacturing.
Meanwhile, the SBOM serves the needs of service teams, providing a view of components required for maintenance, repair, and part replacements, often including information on replaceable parts or kits not present in the EBOM.
These BOM types, work together to create a cohesive product structure, allowing each team to access and interact with the information relevant to their function. Together all these structures create a product lifecycle digital twin.
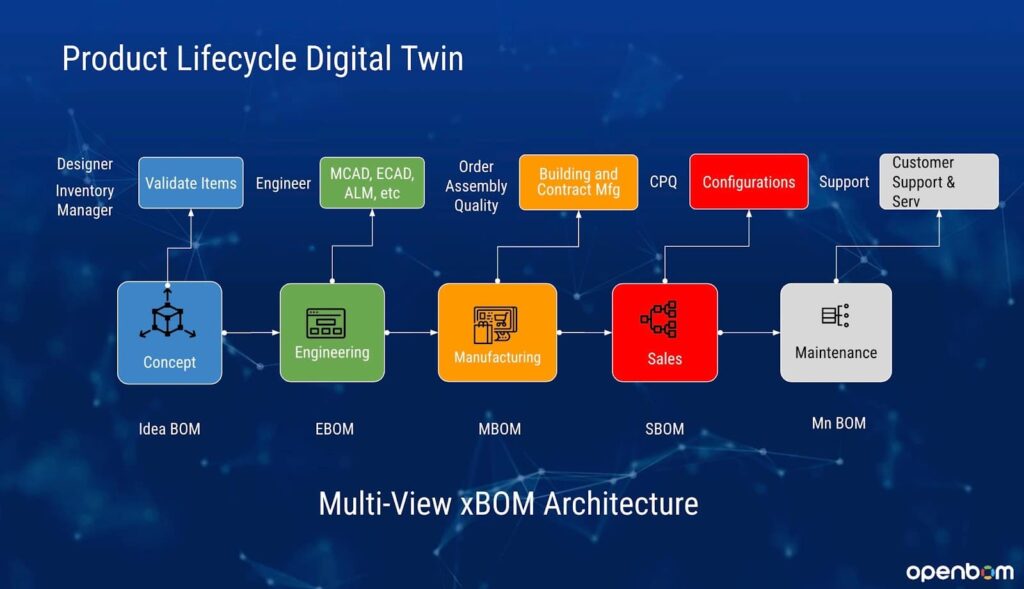
Through xBOM’s integrated approach, companies ensure that design intent, production requirements, and service needs are seamlessly aligned, minimizing errors, reducing lead times, and promoting product quality and consistency across every phase of the product lifecycle.
The Role of EBOM in the Digital Transformation Process
The evolution of EBOM into an integrated xBOM model is a key enabler for digital transformation in manufacturing. As companies adopt digital threads, the demand for an open, flexible, and graph-based data model, like the one OpenBOM provides, will continue to grow. The ability to seamlessly share, update, and track engineering data across the enterprise paves the way for Industry 4.0 initiatives, including AI-driven insights and IoT connectivity, where every stage of the product lifecycle is interconnected.
Conclusion
The Engineering Bill of Materials is no longer just an isolated piece of information (eg. Excel exported from MCAD system). EBOM is an integral part of the interconnected xBOM ecosystem that fuels cross-functional collaboration, data accuracy, and operational efficiency.
OpenBOM’s xBOM service leverages a unique graph-based data model to integrate EBOM with other BOM types, enabling real-time updates, seamless change management, and variant handling in a multi-CAD environment. As manufacturing complexity rises, the role of EBOM within xBOM will be pivotal in driving digital transformation, empowering organizations to deliver better products faster and with fewer errors.
Want to learn more? REGISTER FOR FREE and check OpenBOM capabilities today.
Best, Oleg
FAQ
Engineering BOM:
An Engineering Bill of Materials (EBOM) is a detailed list of components, assemblies, and subassemblies designed by engineers to define a product’s structure for manufacturing. Typically derived from CAD data, the EBOM includes materials, part numbers, and technical specifications essential to the design, representing the product’s intended form. It serves as a blueprint that communicates precise design intent and requirements to downstream departments, enabling accurate planning, procurement, and production processes
xBOM:
The xBOM (or cross-functional Bill of Materials) is a flexible, multi-view BOM structure that allows organizations to create and manage various BOM configurations tailored to different departments, stages, or use cases within the product lifecycle. Unlike traditional BOMs, xBOM can dynamically represent Engineering BOM (EBOM), Manufacturing BOM (MBOM), Service BOM, and more, all linked by a unified data model. OpenBOM’s xBOM service enables this by leveraging a graph-based data structure that connects all related BOM views, fostering seamless data continuity and traceability across engineering, manufacturing, procurement, and service functions. This adaptability helps streamline complex BOM management and supports a robust digital thread throughout the product lifecycle.
Multi-view BOM:
A Multi-view BOM provides tailored views of a product’s components for different departments, such as Engineering BOM for design specs and Manufacturing BOM for assembly details. This structure ensures data consistency across the product lifecycle, enhancing collaboration and supporting a connected workflow between engineering, manufacturing, and service teams.
Manufacturing BOM:
A Manufacturing BOM (MBOM) details all components, assemblies, and materials required to manufacture a product. Unlike the Engineering BOM, which focuses on design, the MBOM includes specific part numbers, quantities, and assembly instructions necessary for production. It aligns closely with manufacturing processes, helping ensure that procurement, inventory, and production teams have the precise information needed to build the product as designed
Maintenance BOM:
A Maintenance BOM (also known as a Service BOM) lists all parts, assemblies, and materials required to maintain, service, or repair a product. Unlike other BOMs focused on design or manufacturing, the Maintenance BOM emphasizes parts subject to wear, replacement, or servicing needs over the product’s lifecycle. It ensures that maintenance teams and service technicians have a complete, structured view of components needed for repairs, facilitating efficient inventory management, ordering, and servicing operations
CAD to EBOM process
The CAD to EBOM process converts CAD design data into an Engineering BOM (EBOM) for manufacturing use. Engineers begin by creating parts and assemblies in CAD. Then, data from the CAD model is extracted into a list of components, organized hierarchically. Additional attributes, such as material and weight, are added to enrich the BOM. The EBOM undergoes validation to ensure accuracy and completeness, then integrates with PDM or PLM systems for downstream use. This streamlined process ensures the CAD design is production-ready and consistent across systems
Join our newsletter to receive a weekly portion of news, articles, and tips about OpenBOM and our community.