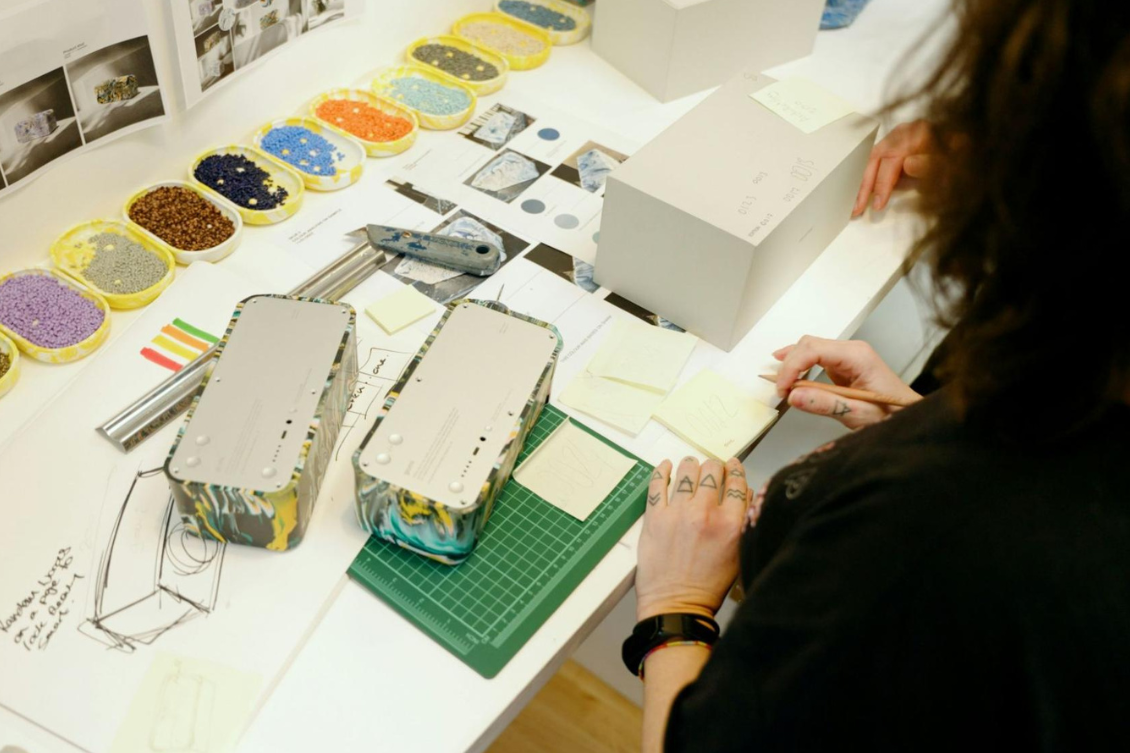
Have you ever wondered why your contract manufacturer (CM) insists on having a detailed Bill of Materials (BOM) before they can provide a quote? While it might seem like just another document in the process, the BOM is actually a crucial part that drives the accuracy of the entire manufacturing journey. Without it, your CM is left to make assumptions about materials, quantities, and even design intent and those assumptions can lead to costly errors, delays, and unexpected outcomes.
In this blog, we’ll explore why your CM needs a BOM for accurate quotation and what can go wrong when this vital piece of information is missing. Whether you’re new to manufacturing or have been in the industry for years, understanding the role of a BOM will help you ensure smooth, efficient, and mistake-free production.
The Risks of Not Providing a BOM
Failing to provide your CM with a detailed BOM opens the door to a host of problems that can derail your project, both financially and logistically. Without a BOM, your CM is left in the dark, relying on assumptions that may not align with your vision or requirements. These assumptions can cause significant risks, from incorrect material choices to unexpected delays and increased costs.
Miscommunication and Wrong Assumptions
Without a BOM, your CM has to guess at critical details—material types, quantities, specific part numbers, and even design intent. These guesses can lead to incorrect decisions that have a ripple effect throughout production. For example, if your product requires a specific grade of steel for durability but this isn’t communicated, the CM might choose a cheaper alternative, leading to a product that doesn’t meet your quality standards.
Inaccurate Quotations
When a BOM is incomplete or missing, any quotation your CM provides is likely to be inaccurate. This could mean either underestimating costs, leading to unpleasant surprises later when real prices surface, or overestimating to cover potential unknowns, which unnecessarily inflates your budget. In both cases, the lack of a BOM prevents your CM from giving a precise cost breakdown and timeline for the project, leaving you in the dark about what to expect.
Production Delays
Inaccurate or missing BOM details can cause delays at various stages of the production process. If your CM selects the wrong components, they might have to reorder the correct ones, extending lead times and pushing back your delivery schedule. A simple misunderstanding can lead to days if not weeks, of lost time—time that could have been avoided with a well-prepared BOM.
Supply Chain Disruptions
A BOM plays a crucial role in ensuring that all components are ordered on time and from the right suppliers. Without it, the CM might order incorrect parts, which can lead to supply chain bottlenecks. If a critical component is not available due to a misunderstanding, your entire project could be delayed while alternative suppliers are sourced or the correct parts are reordered.
Key Reasons a CM Needs a BOM
Providing a detailed BOM to your CM is not just a formality, it’s an essential step that ensures the success of your project. The BOM serves as a blueprint for every aspect of the manufacturing process, helping your CM deliver accurate quotes, streamline production, and maintain quality. Here are some key reasons why your CM needs a BOM:
Accurate Material Selection
A detailed BOM specifies the exact materials, components, and part numbers needed for your product. This prevents your CM from making incorrect assumptions about material choices. Whether it’s the grade of plastic, type of metal, or specific electronic components, the BOM ensures that the CM uses the right materials that meet your product’s performance, durability, and compliance requirements. This reduces the risk of material mismatches that could compromise the quality or functionality of your product.
Streamlined Procurement
One of the key functions of a BOM is to facilitate procurement. When your CM knows exactly which parts and materials are needed, they can source them more efficiently, reducing the risk of delays due to missing or incorrect components. A clear BOM allows your CM to work with their suppliers to ensure that all materials are available when needed, keeping production on schedule and minimizing the risk of supply chain disruptions.
Version Control and Design Consistency
A digital BOM, especially one managed through a tool like OpenBOM, ensures that your CM always has access to the most up-to-date version of your product’s design. If there are any design changes during the production process, a centralized BOM ensures that these updates are communicated instantly, reducing the risk of outdated versions being used. This consistency is crucial for maintaining product quality, especially in larger projects where changes may occur frequently.
Best Practices for Preparing a BOM for Your CM
Creating a well-structured BOM is crucial for ensuring a smooth relationship with your CM. A thorough BOM minimizes the risk of errors, reduces costs, and keeps your production on track. Here are some best practices for preparing a BOM that will help you and your CM stay aligned throughout the manufacturing process:
Ensure Completeness and Accuracy
A BOM must be as detailed and accurate as possible. Include every component, sub-assembly, and material that your product requires, down to the smallest screw or connector. Make sure to include exact quantities, part numbers, material specifications, and any special instructions. Incomplete or vague BOMs create uncertainty for your CM, leading to errors in material selection, assembly, and pricing.
Organize the BOM Hierarchically
Structuring your BOM in a clear and hierarchical manner helps your CM easily understand the relationship between components and sub-assemblies. Group parts into logical categories, such as mechanical components, electronics, and packaging. A hierarchical BOM provides a visual representation of how parts and assemblies fit together, making it easier for your CM to plan the manufacturing process.
Use a Digital Tool for BOM Management
Using a digital tool like OpenBOM to manage and share your BOMs brings several advantages. A digital BOM ensures version control, meaning your CM always has access to the latest updates. It also allows for real-time collaboration between your engineering team and your CM, reducing the chances of miscommunication. Additionally, digital tools often integrate with CAD and PLM systems, making it easier to import and update BOMs directly from your design files.
Conclusion
A detailed and accurate BOM is not just a document, it’s a vital tool that drives the success of your manufacturing project. Providing your CM with a well-prepared BOM ensures that both parties are aligned on every aspect of the production process, from material selection to assembly planning. Without it, you’re risking miscommunication, delays, quality issues, and unexpected costs.
By following best practices, such as ensuring completeness, using a hierarchical structure, and leveraging digital tools like OpenBOM, you can streamline the production process and set your CM up for success. Ultimately, a strong BOM leads to more accurate quotes, smoother procurement, and a final product that meets your expectations.
Don’t leave your manufacturing process to chance, equip your CM with the detailed BOM they need to deliver top-quality results, and see the difference it makes in your project’s efficiency and outcomes.
By: Jared Haw
Join our newsletter to receive a weekly portion of news, articles, and tips about OpenBOM and our community.