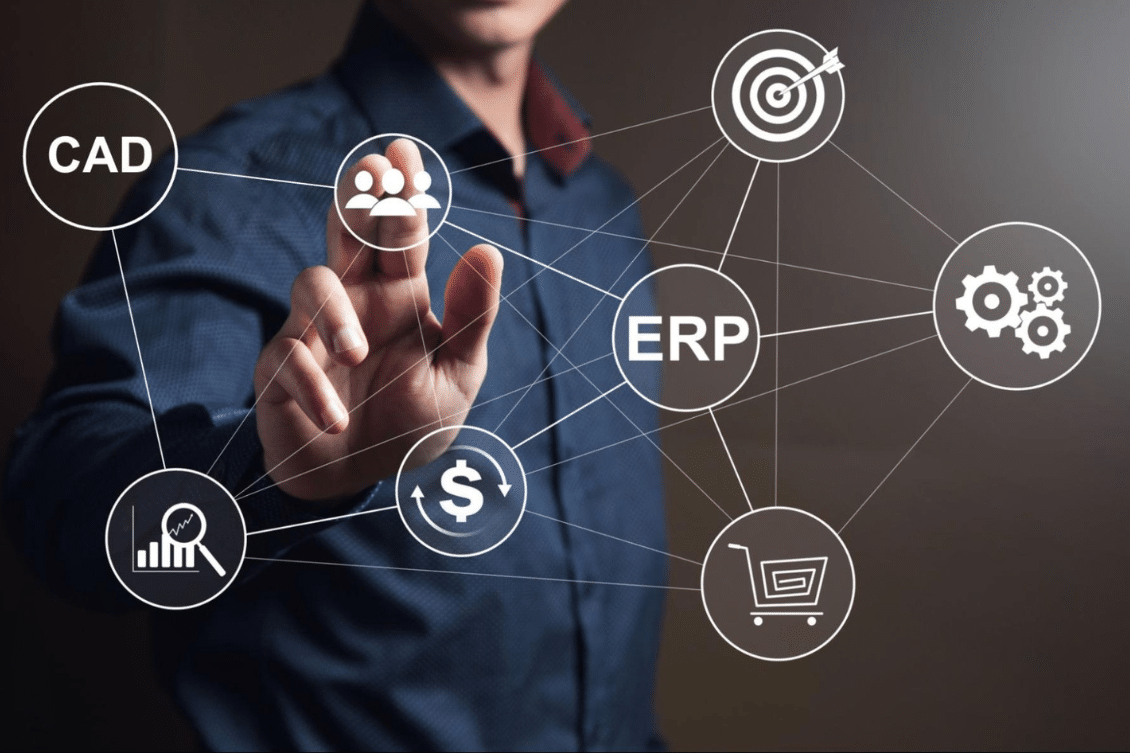
CAD and ERP are the two most mature domains of information that stand out in the domain of engineering and manufacturing. Those are two pivotal technologies that you can find at the core of operations. Design is done using Computer-Aided Design (CAD) and finance and procurement are done using Enterprise Resource Planning (ERP) systems.
CAD systems are ubiquitous and used universally for their precision and efficiency in design processes. On the other hand, mid-size to larger enterprises rely on ERP or Material Requirements Planning (MRP) systems to streamline their finance and operational workflows. For many companies, the integration of these two systems seems a logical step forward. Yet, the path to achieving a seamless connection is fraught with controversy and challenges.
In this article, I want to discuss what options companies can see on the path of connecting engineering to manufacturing to discuss the benefits, pitfalls, and best practices for integrating CAD and ERP systems.
Two Worlds: Engineering and Operations
At the heart of the integration challenge is the fundamental difference in data representation between CAD and ERP systems. Engineers and manufacturing planners operate on distinct domains; what is intuitive for one is often foreign to the other.
This disparity is not merely philosophical but manifests in the practical, everyday handling of Information. The task then is to find a bridge that can span these two worlds, facilitating a dialogue that enhances both design and production efficiency.
Data Structures Incompatibility
A key obstacle in integration efforts is the incompatibility of data structures. Engineering departments frequently manage product data through versions, revisions, and changes, focusing on the evolution of design. Conversely, ERP systems are grounded in production, scheduling, and the management of resources, with time-specific effectivity dates.
Aligning an engineering revision with an ERP effectivity date is challenging, as these systems do not naturally correspond. Although ERPs often include a Bill of Materials (BOM) function, this typically serves financial and production planning rather than engineering purposes, further complicating integration.
Mapping the Data
The typical idea that usually sits in the heads of IT and engineering is to “map” data between CAD and ERP. The process of mapping data between CAD and ERP systems introduces significant complexity. While it’s possible to map certain attributes, aligning the lifecycle operations and structures of engineering and manufacturing processes is a challenge. Most companies discover these challenges already in the middle of the process when they start asking questions like “What will happen when we release a new CAD part (or drawing)? This complexity can hinder effective data transfer, raising questions about the best methods for achieving integration.
Three Options for CAD-ERP Data Transfer
Let’s talk about possible best practices of integration between engineering and manufacturing and how to make it efficient and avoid unnecessary complexity and pain.
Simple Synchronizing Data:
The most straightforward approach involves synchronizing data between CAD and ERP systems and making on-the-fly decisions about BOM transformation. Although relatively simple to implement, this method can become complex and difficult to maintain over time, especially when determining the timing and necessity of transferring specific events or revisions.
Single BOM (or EBOM):
A more streamlined approach is to establish an Engineering Bill of Materials (EBOM) that provides a complete, structured product representation for transfer to the ERP system. This method minimizes overhead but requires a clean, well-organized BOM baseline, including revisions and approvals before data transfer can occur.
xBOM or Multi-BOM Approach:
The most advanced option is the xBOM approach, which utilizes two BOMs – EBOM for engineering and Manufacturing Bill of Materials (MBOM) within a Product Lifecycle Management (PLM) system. This method allows for the setup of comprehensive business logic between EBOM and MBOM, simplifying data transfer to the ERP system.
Conclusion
The integration of CAD and ERP systems is often touted as a straightforward solution to streamlining product development and manufacturing processes. However, the reality is far more complex, with many companies grappling with data transfer challenges through the implementation of bespoke scripts, synchronizations, and various software solutions.
At OpenBOM, we advocate for a structured approach to data organization, whether through EBOM or a combined EBOM/MBOM strategy, to formalize the business process of moving from engineering to manufacturing.
Heads up – OpenBOM is coming with xBOM feature later this year, introducing capabilities to define multiple BOM types (EBOM, MBOM, SBOM, etc). Check with us if you’re interested in learning more.
For more information on best practices and to begin your CAD/PLM/ERP integration journey, register with OpenBOM today.
Best, Oleg
Join our newsletter to receive a weekly portion of news, articles, and tips about OpenBOM and our community.