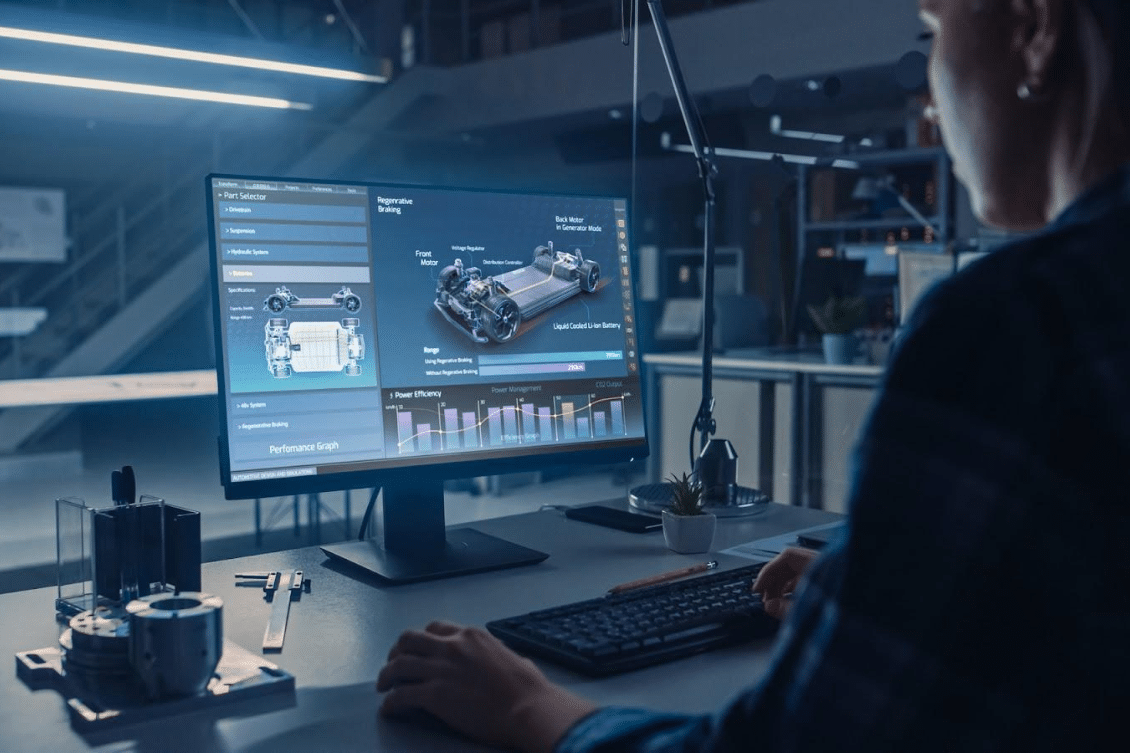
In the world of manufacturing, a common strategy I often hear about is the idea of syncing CAD data to an ERP system. This approach is seen as a way to integrate engineering and manufacturing processes. A simple question – can OpenBOM send CAD data to ERP? Yes, it can. However, a more critical question arises: should you do this? For many companies, this question triggers important discussions about process integration, process management, various business processes (ETO, CTO, etc), management of raw materials compared to design, information flow, engineering processes, and establishing a digital thread between engineering and manufacturing. This is the time when companies start to think about PLM solutions and what is the right business strategy for information systems. If the company is engineering to order (ETO), it also brings questions about project management and project lifecycle management. Let’s dig into these topics a bit more and try to find recommendations to build a business strategy to optimize product lifecycle.
CAD, PLM, ERP, and Product Models
In a manufacturing company, different departments (or teams) manage information in their own ways. The design and engineering sector is different from production and procurement. The process of designing and building products starts with computer-aided design. While the CAD system holds design information, alone it doesn’t have all the information. Sometimes you need multiple CAD systems working together. How to do so? This is how engineering product models come into play (often called EBOM). Engineering product models focus on combining various pieces of information about a product. They manage CAD files, Engineering Bills of Materials (BOMs), and lifecycle processes including release stages. On the other hand, production and procurement are focused on how to manage ordering and manufacturing planning. This model is different. The first model is traditionally revision-based, dealing with lifecycle changes, whereas the second is effectivity-based, focusing on procurement timeline and production process.
CAD Is Limited To Representing Engineering Data
One major gap in the engineering data model is that it cannot be fully represented by CAD systems alone. Most CAD systems are document-driven and only represent one aspect of product definition, such as mechanical, electronic, or software. Also, there are multiple pieces of information that don’t fit CAD data structure even if you try to do so. For example, you will experience significant problems placing manufacturer data, suppliers, and cost to CAD systems. To bring all these pieces of information together, validate them, and release them requires more than a single CAD system. So, how to do so? You need to have an engineering product model to support a comprehensive design digital thread of information.
It is capable of getting all your multiple pieces of design, combining them, adding everything that is not defined in CAD, and releasing it. That will establish a baseline that can be used to kick off the production planning process.
MRP Data Model and Engineering Information Are Incompatible
Another potential issue in connecting CAD to ERP is the inability of the MRP (Material Requirements Planning) data model to adequately handle engineering information and revisions. The MRP model is designed for production, and attempts to store complete product data in an ERP system usually fail. This is because the ERP system is not equipped to manage the complex and detailed information involved in engineering processes. An attempt to “squeeze” design data into ERP can succeed at first but as soon as you move into a process of changes, ordering, freezing a baseline for production, and many other specifics related to manufacturing, you will find yourself deep in the complexity of data integration.
The Right Approach: Building Efficient Product Data Models
So, what’s the correct approach? You should think holistically about product lifecycle management and the product development process. That is exactly what a PLM system can do. You need to start from efficient product data management, instead of only focusing on document management for CAD systems. Companies managing product development should start by building simple and efficient data models for each stage of product development: design, engineering data, production data, and production and maintenance data. Once these are established, the process for data flow between these silos should be seamless, connecting different data areas together in a single product knowledge graph. It will allow management of the product development process by connecting steps in the product life cycle, and the engineering process with the manufacturing process.
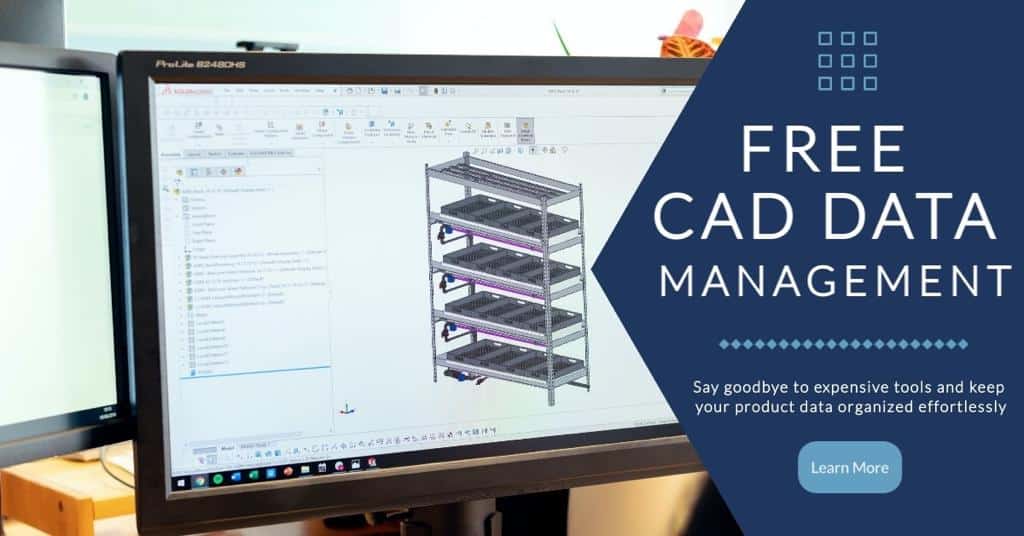
Conclusion
The initial idea of sending CAD data to ERP is sound, but it lacks many crucial details. Companies need to transform design data into a product model that represents engineering data (usually the Engineering BOM), manage engineering releases, and only then send the data to ERP. This is what modern PLM technology can do. This way, the engineering product model maintains the entire history of engineering releases. It includes all engineering information. It uses data snapshots to translate this information for specific manufacturing and production planning (Manufacturing BOM). Thus, while ERP systems are valuable, they cannot replace the need for PLM systems in managing the intricate details of engineering BOMs.
REGISTER FOR FREE and learn how OpenBOM helps. Do you have questions? Reach out to us here at OpenBOM and we will help you to find the right solution.
Best, Oleg
Join our newsletter to receive a weekly portion of news, articles, and tips about OpenBOM and our community.