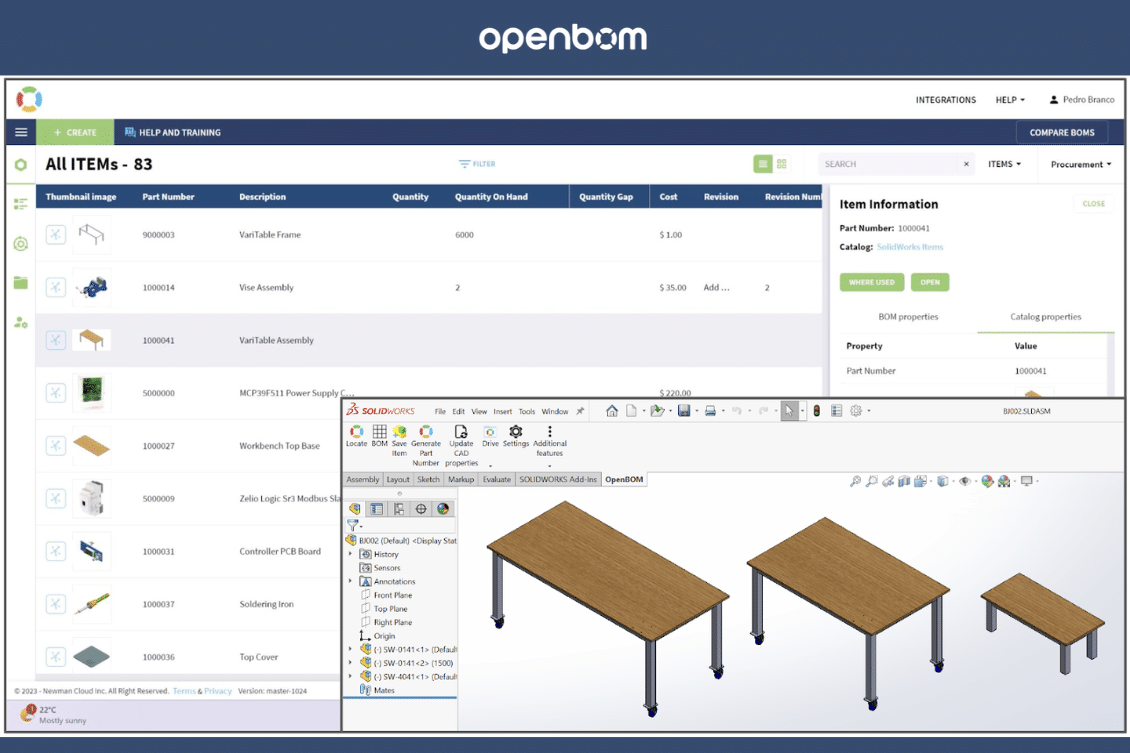
Configurations offer robust functionality that has been present since the inception of SolidWorks (introduced in SolidWorks ’96), and numerous users have discovered their immense utility. However, as the saying goes, ‘With great power comes great responsibility.’ Misused configurations can lead to challenges in your modeling and CAD data management, potentially resulting in a complex predicament.
Moreover, the landscape varies significantly based on your role within the SolidWorks environment. Whether you’re an individual user, crafting your designs with a unique approach, or a team player collaborating with fellow SolidWorks users of varying skill levels, the dynamics shift. This dichotomy extends further to encompass the industry you operate in, compliance requirements, regulations, the cost of errors, the mission-critical nature of your product, and the reliance on delicate data structures.
This article dissects the pros and cons of utilizing SolidWorks Configurations, providing insights into whether they should be employed for diverse part numbers. Join me as we delve into this discussion. Certain sections of this article reflect the author’s viewpoints, shaped by his experience in implementing and integrating SolidWorks Products across diverse industries.
Are SolidWorks Configurations the key to optimizing your design process? Let’s explore together. 🚀💡”
Introduction to configurations
Configurations in SolidWorks allow you to create multiple variations of a part or assembly model within a single document. Configurations are a convenient way to develop and manage families of models with different dimensions, components, or other parameters.
You can create configurations manually, or you can use a design table to create multiple configurations simultaneously. Design tables provide a convenient way to create and manage configurations in a worksheet. You can use design tables in both part and assembly documents.
Let’s see the great functionalities of SolidWorks Configurations:
- Design tables
- You can easily represent different parts or assembly sizes in a single file
- You can easily change parametric dimensions or Suppress or Unsuppress features or components
- You can very easily change the configuration on Drawing Views or in an assembly switch the component to another config.
In my view, they are very good for:
- Represent Simplified versions of Parts or Assemblies. Tip: Use Open Advanced to select or create a simplified config.
- Simplify or Defeature the Part or Assembly for FEA analysis
- For simulation projects to represent different study iterations
- Represent different states of the same Part/Assy
- Configs are a great way to conceptualize design quickly in a single file and then can be divided into separate files with Save Configurations.
- Be used for Non-Revision manages Parts with the same Form Fit and Function (e.g.: Toolbox)
Important Limitations to know of using Configurations:
They are Fragile
You can simply overwrite all dimensions with a mistake and ruin your configured Model, this is usually only noticed (too late) when another user wants to re-use the design.
If you delete a configuration. Next time you open a parent file the configuration will be reattached to last active.
Files can be Bigger
By adding configurations to your SolidWorks files you are increasing the data stored within the file, resulting in the assembly or part files getting bigger. It will also consume more resources in RAM per file, although in the latest releases, SolidWorks Corp. has reduced this problem by enabling purge configuration data and loading to memory only the active config. Purging configuration data can lead to longer rebuilds to recreate it in favor of quicker opening files.
Lose One File, you Lose More
If you are working with your SolidWorks master models and all your automated design configurations are kept within one file – if anything happens to this file (e.g. it gets deleted or becomes corrupt due to working on network share) all your master model data could be compromised.
More Complex Relationships
Added complexity to manage the references between files, creates a matrix of dependencies harder to manage changes and permissions.
Limited Search Capabilities
You can search for file names not inside configurations.
Using configurations to represent different Part Numbers in the same file is a good or bad practice?
In my 24 years of experience implementing SolidWorks products and integrating SolidWorks data, I believe this approach has more disadvantages than advantages. The more you rely on master CAD models for ERP integration, CPQ, configure price quotes, or design automation the more the limitations will hit your CAD data, and you end up with bigger challenges to manage changes and revisions over a growing CAD user team with different experience levels.
Let’s summarize the Advantages and Disadvantages
Advantages
- Seems faster with fewer files to manage.
- Fewer clicks or steps for the users compared to using separate files.
- You can change or add a feature in a master part and propagate that to all configs.
- (Workaround is to use base parts).
- Flexibility in Design variances.
- Less CAD user skill to manage file references.
Disadvantages
- Their fragilities are incompatible with controlled critical data (Part Numbers)
- You cannot keep the same Drawing filename with the Model Filename, compromising the Open Drawing command used in API for automation
- The time to fix errors can be bigger compared with the time you save on the advantages of use.
- You need more user skill to manage file references and reuse: save as, pack and go, save configs to separate into files
- Performance. If you are on a race, opening, and saving can be slower vs independent files or slower rebuilds if you purge them.
The more you are invested in your CAD data and the size of your CAD team the more you have processes to control CAD data and changes (ECO/ECR) the more you can benefit in the Long run to separate Make Items, or Part Numbers that have a revision managed Drawing into a single file and do not use different part number for different configurations.
It can be used for non-revision-managed parts, like toolbox or standard purchased components.
On a bigger design team with an engineering process in place and change management policies, this approach will struggle, best to have a single independent file with a single part number with a linked drawing. One lifecycle from concept/prototype state to released, Controlled Change, and revisioned until obsolete. The file is a container that does not influence other parts.
Configurations in my view should be used as they were first intended; as alternate representations of a single part with a single part number in a single file. If the Form Fit Function changes then get a new file.
OpenBOM Supports both methods and it’s independent of whatever you choose.
You can easily Auto-Number the Part Number Property per File or per Config.
In this video, we show you how to create Multiple BOM with Different Part Numbers in SW Configurations:
By Pedro Branco
Join our newsletter to receive a weekly portion of news, articles, and tips about OpenBOM and our community.