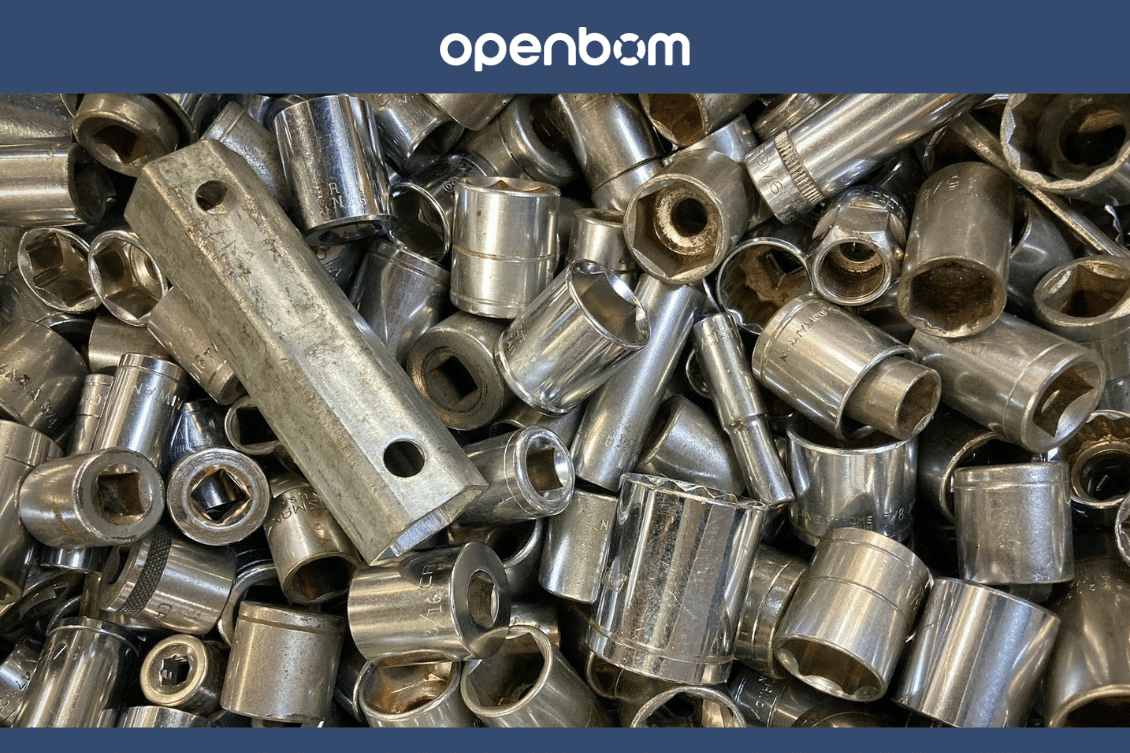
In the vast and intricate world of manufacturing, where precision and efficiency reign supreme, there exists a hidden language that speaks volumes without uttering a single word: part numbers. These seemingly innocuous combinations of letters, numbers, and symbols hold immense significance within the manufacturing realm, serving as a key to unlock the intricate mechanisms that drive production processes. From automotive giants to mom-and-pop shops, the adoption and understanding of part numbers have become indispensable in ensuring smooth operations, effective inventory management, and seamless collaboration within the industry.
While part numbers may appear as simple labels to identify components, their true power lies in the structured information they encapsulate. They serve as the backbone of communication, enabling manufacturers to navigate the labyrinthine world of complex assemblies and intricate supply chains with unparalleled ease. In this article, we delve into the importance of part numbers in manufacturing, exploring how they streamline processes, enhance productivity, and pave the way for innovation in an increasingly competitive landscape.
In this blog post, we uncover the pivotal role of part numbers in orchestrating the symphony of modern manufacturing.
Why is it Important to Manage Part Numbers with Your Suppliers?
Effective management of part numbers is crucial when collaborating with suppliers in any business. Part numbers serve as unique product identifiers, enabling clear communication, streamlined operations, and efficient supply chain management.
By establishing a robust system for managing part numbers with suppliers, businesses can enhance accuracy, minimize errors, improve inventory management, and foster seamless integration within the supply chain.
Here are the main reasons why it’s important for suppliers to effectively manage part numbers.
Clear Identification
Suppliers need to assign unique part numbers to their products to ensure accurate identification and differentiation. Clear and unique part numbers help prevent confusion, errors, and mix-ups during the ordering, production, and fulfillment processes.
Efficient Communication
When suppliers and their customers use consistent part numbers, it simplifies communication and ensures that both parties are referring to the same part. This helps streamline transactions, inquiries, and discussions related to specific parts.
Inventory Management
Properly managed part numbers enable suppliers to track their inventory effectively. By associating part numbers with specific products, suppliers can monitor stock levels, plan for replenishment, and ensure the timely availability of parts to meet customer demands.
Quality Control
Part numbers play a crucial role in traceability and quality control processes. With unique part numbers, suppliers can track the origin, manufacturing details, and performance characteristics of their products. This enables efficient recalls, warranty management, and quality assurance.
The Connection Between your Part Numbers and your Supplier’s Part Number
The connection between part numbers from a supplier and a manufacturing company forms an essential link in the complex network of modern manufacturing. It is a bridge that facilitates seamless collaboration, effective inventory management, and efficient production processes between these two entities. Let’s explore the intricacies of this connection and understand its significance.
Suppliers are key partners for manufacturing companies, providing the necessary raw materials, components, or sub-assemblies required for production. Each supplier typically assigns their own part numbers to the items they provide, which serve as unique identifiers within their internal systems. These supplier part numbers are crucial for tracking inventory, managing orders, and facilitating communication between the manufacturing company and the supplier.
Additionally, the connection between part numbers allows for effective collaboration and communication between the manufacturing company and the supplier. When issues arise, such as quality concerns or design changes, both parties can quickly refer to the corresponding part numbers, ensuring a clear understanding and swift resolution of any challenges.
Furthermore, the connection between part numbers enables the manufacturing company to maintain consistency and control over their production processes. They can accurately identify and manage components, ensure proper assembly, and maintain product quality and traceability throughout the manufacturing lifecycle.
Part Numbers or Part Names?
When you are speaking with your supplier, it’s common to use part names to discuss a part. If you are going through design for manufacturing (DFM) it’s also common to refer to part names. However, part names are not very objective.
If you say a part name, it might not provide you with the entire story. If it’s a plastic housing then just saying housing will not paint the full picture. Meaning, if you have multiple colors, then which color is it?
Should you use Supplier Part Numbers?
Each company, such as your company will manage their part numbers. If you are purchasing an off-the-shelf item, such as a battery, motor, etc.. then do you want to use the supplier manufacturing part number (MPN)?
What happens if the MPN changes? If it does then your BOM will have a problem.
What Should You Do?
The debate on how to manage part numbers has been debated for quite some time. This is because of the significance of them and what they mean to your business. Not properly managing these part numbers will lead to multiple issues.
OpenBOM is a cloud-based PDM & PLM platform to manage your engineering and manufacturing data. Companies from startups to Fortune 500s use OpenBOM to create a centralized database to bring in, store, and manage their manufacturing data. With this infrastructure, users also use OpenBOM to streamline both their change management and PO processes.
If you need to improve the way you manage your data and processes, contact us today for a free consultation.
Regards,
Jared Haw
Join our newsletter to receive a weekly portion of news, articles, and tips about OpenBOM and our community.