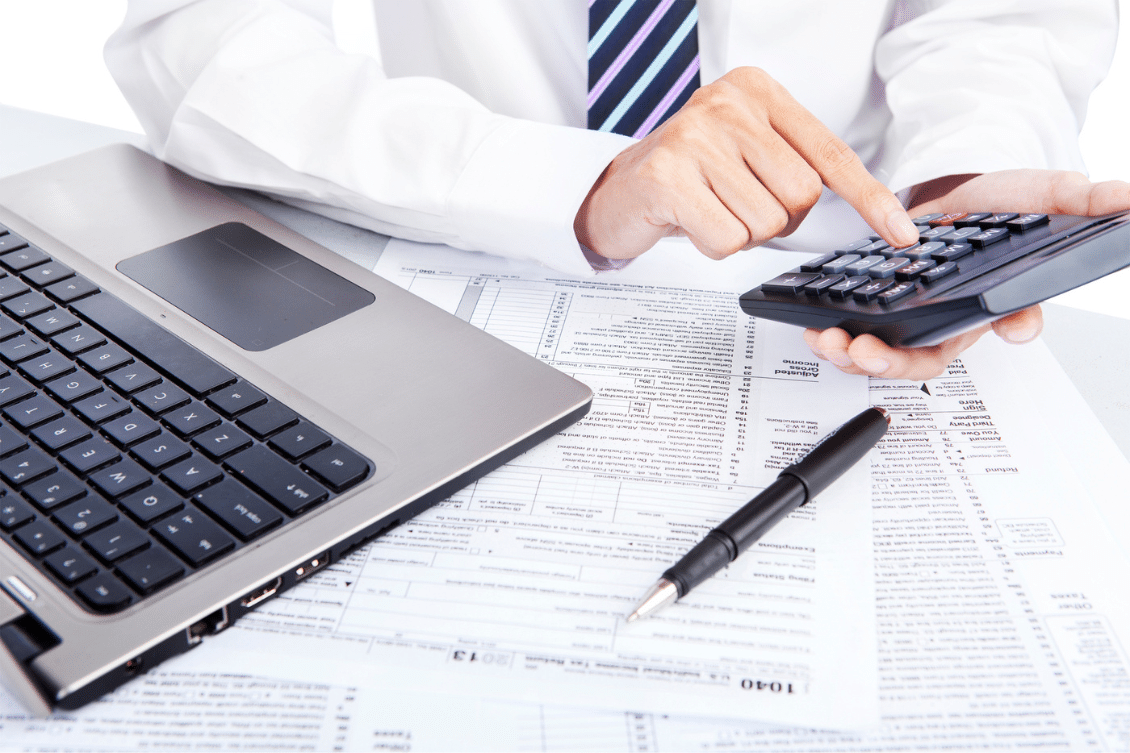
Last month, I wrote an article discussing whether it’s a good idea to store cost and supplier data in CAD systems. Most of my colleagues on LinkedIn agreed that cost info shouldn’t be kept in CAD systems, and I totally agree with them. Cost calculations can be a real headache. Cost info usually comes from different sources: quotes for custom parts, catalog prices for off-the-shelf items, and calculations based on materials and labor costs. But, unfortunately many engineers and manufacturers still use very inefficient method of cost rollups using Excel or other spreadsheets.
The Problem with Excel:
Many engineering teams use Excel for calculations, but when it comes to figuring out the total cost of a product assembly, Excel falls short. CAD data can be pulled into Excel, but it often doesn’t include all the materials, especially when they come from different sources. Adding unit costs for components and factoring in labor becomes a messy process that both engineering teams and production planners have to deal with.
How OpenBOM Helps:
OpenBOM simplifies cost management by providing three essential tools:
Item Catalogs:
You can create a database of all components, whether they are custom, off-the-shelf, assemblies, labor, or materials. These catalogs help you define unit costs and other essential information. Collaborative tools allow you to share catalogs with contractors and suppliers to keep unit cost data up to date.
Product Structure (BOMs):
OpenBOM lets you create a structured bill of materials that includes all components, sub-assemblies, and extra information needed to build a product. You can generate BOMs automatically from CAD systems with just a click, even if you use multiple CAD systems. You can also add non-CAD elements, labor, and other details to your BOMs.
Cost Rollup Formula:
OpenBOM comes with a formula roll-up mechanism designed to work with structured data. It collects unit information from all levels and sublevels and calculates the cost. You can define different formulas, including specific business logic, and the rollup will pull data and calculate the total cost. You can also exclude certain components or entire assemblies from the calculation.
Collaboration and Cost Changes:
OpenBOM’s collaborative editing tools allow everyone to make changes in catalogs and bring BOM data directly from CAD simultaneously. No one has to wait, and the cost is automatically recalculated. Revision history keeps track of cost changes.
Documentation and future steps
You can check OpenBOM documentation to learn more about formula and rollup management. Check this link. Watch the following video to learn more about cost management:
Conclusion:
OpenBOM offers a practical solution for organizing product information, including suppliers and cost data. Once your data is organized, you can use BOMs created from CAD systems and adjust them manually to calculate costs effectively.
Give it a try with a 14-day free trial to see how OpenBOM can simplify your cost management.
Best, Oleg
Join our newsletter to receive a weekly portion of news, articles, and tips about OpenBOM and our community.