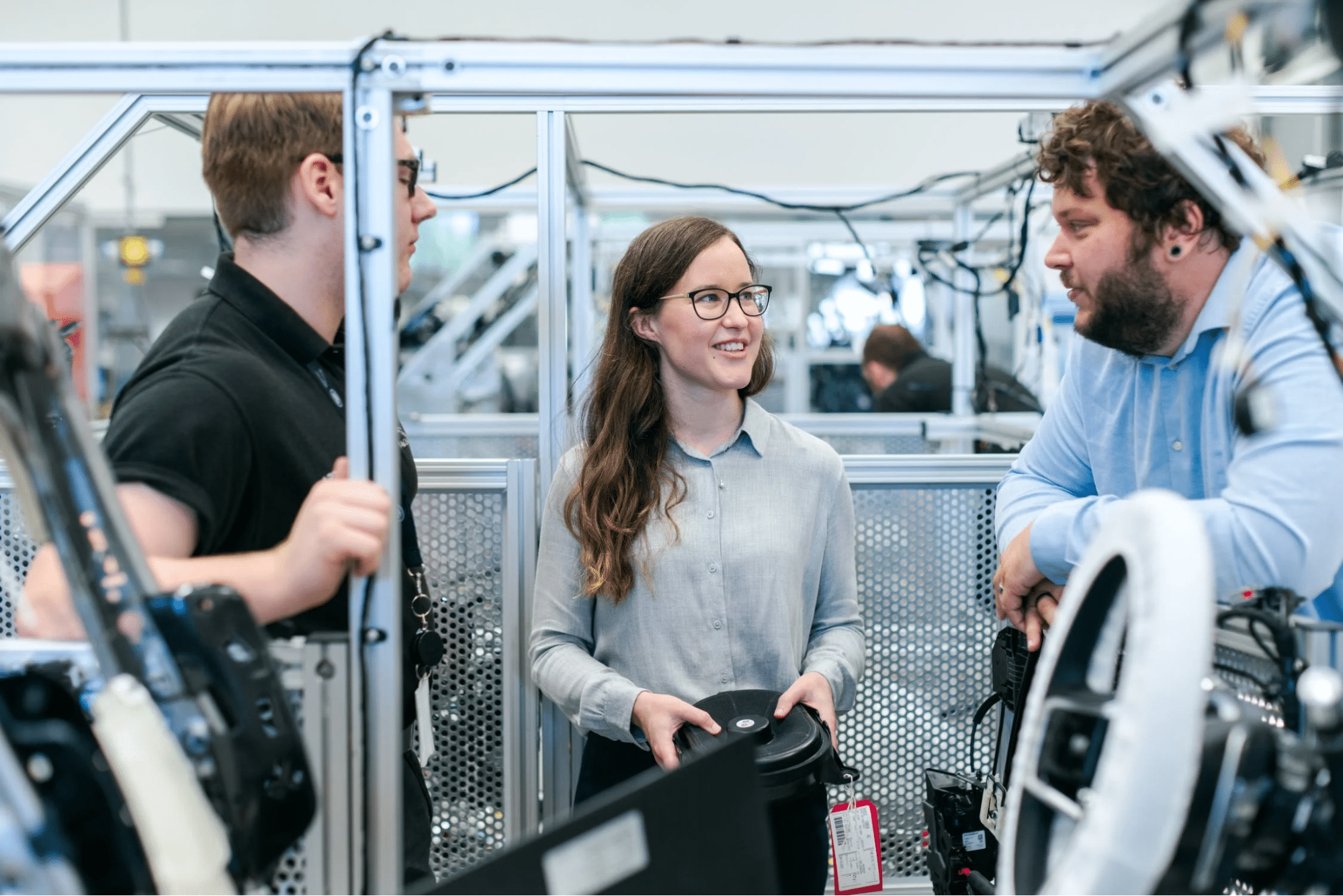
If you are developing a new product, you most likely have asked yourself, when should I engage with my contract manufacturer? Before answering this, we should look at the overall development process.
The Development Process
There are a few steps to manufacturing a product. Shopify has listed seven different steps. These will be idea generation, research, planning, prototyping, sourcing, costing, and commercialization.
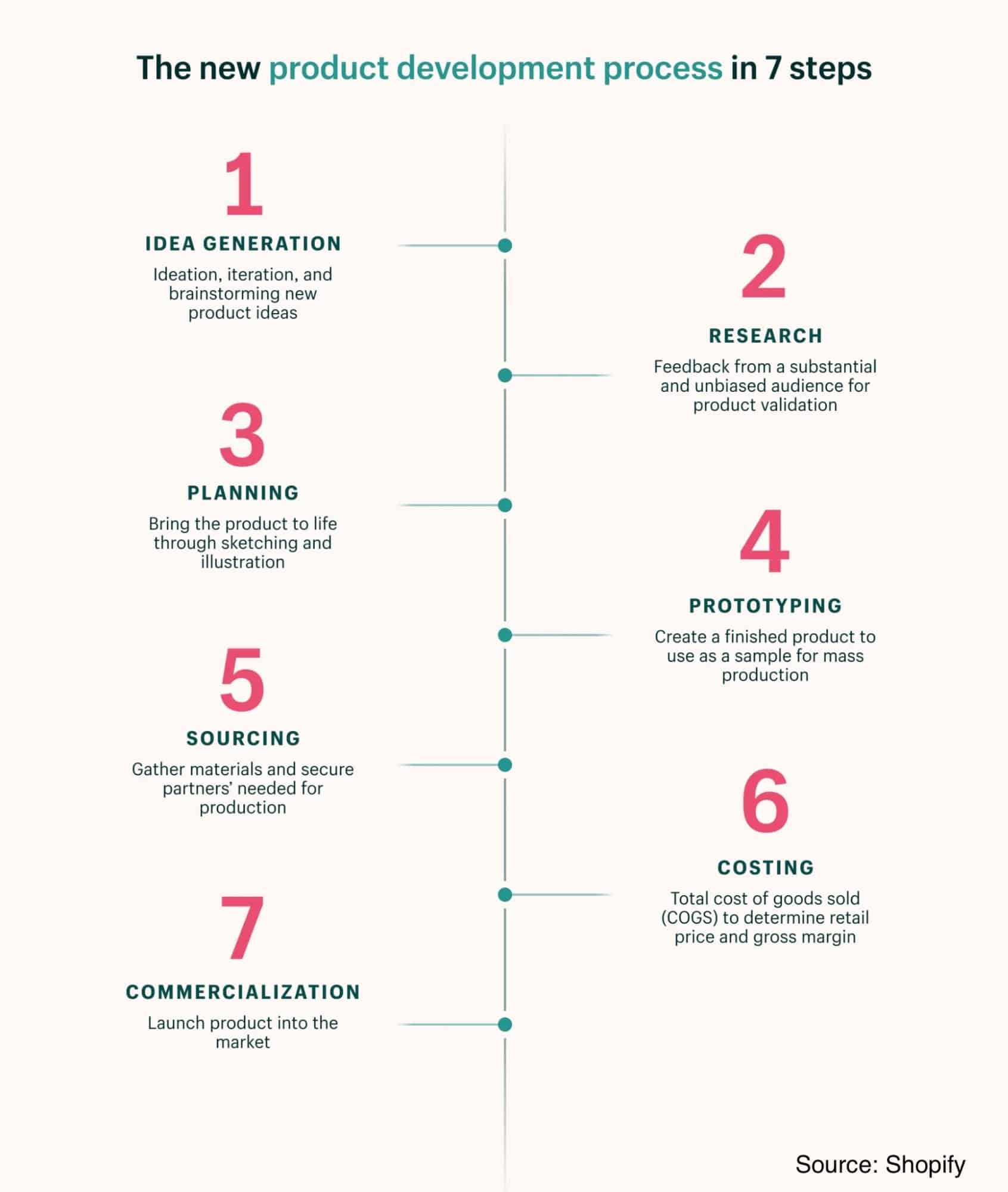
However, when in these steps should you engage with your manufacturing partner? During the initial steps, no contract manufacturer would be interested, except for some unique cases. A contract manufacturer should not be engaged before product-market fit or validating your product. Their value is shown after demand has been generated.
When your contract manufacturer can get involved with your product is when you have a working or semi-finished prototype and there has been some initial demand generated from unbiased people. Of course, the best is when there is a commitment from users. For a basic example, contract manufacturers would be willing to work with a company that generated $1 million in backing from a crowdfunding campaign. But they might not be willing to work with a company that only generated $20,000.
Don’t Make These Mistakes
From Shopify’s development steps, you will most likely choose your CM at the 5th step, sourcing. However, there is a lot of work to be done between this step and commercialization. Depending on the product, it can take years before you can commercialize it.
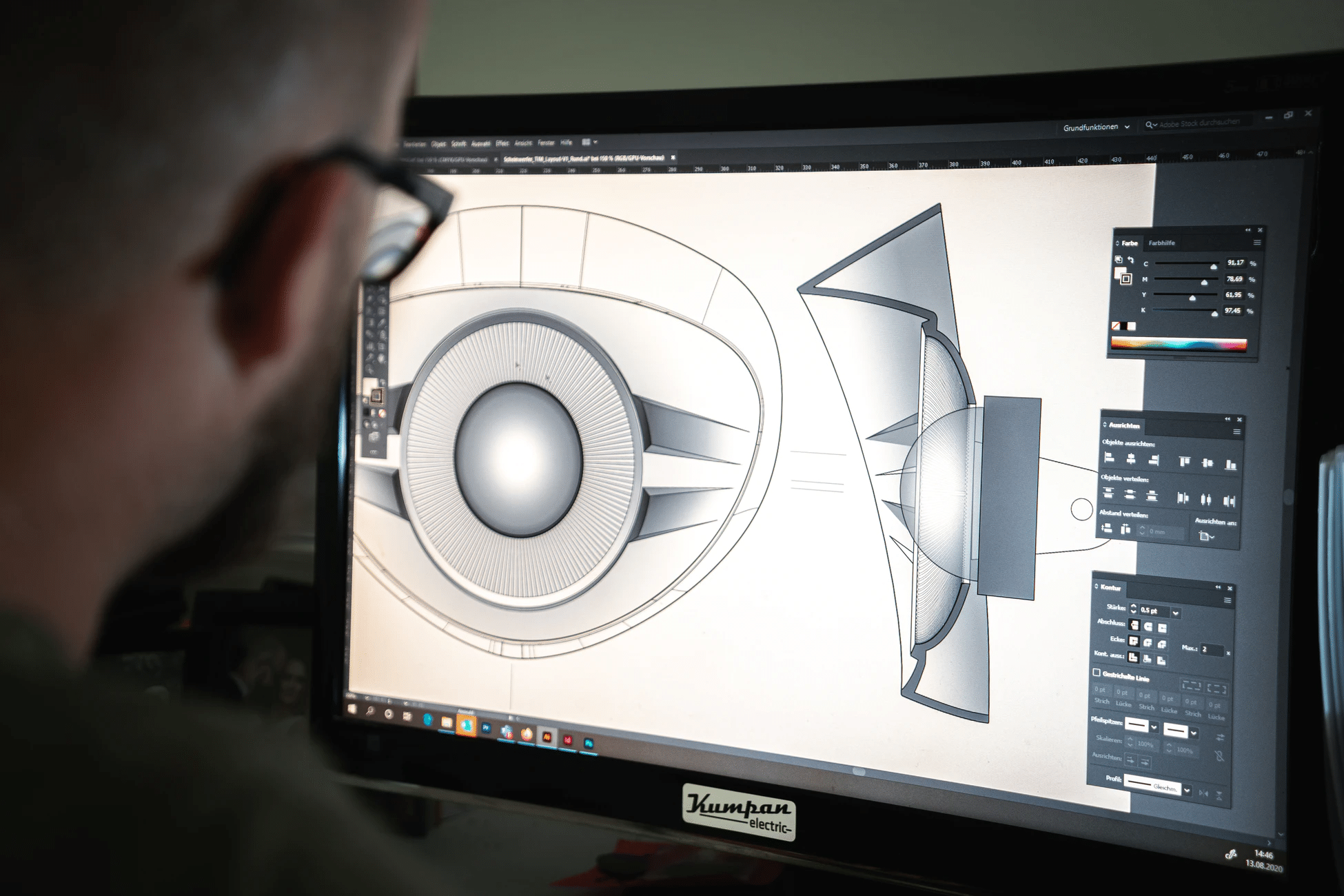
After the demand has been generated, your contract manufacturer will likely be willing to engage with you. The best thing you can do to get ready for commercialization is to leverage their engineering support. This is because 95% of the time, no matter how good your crowdfunding video was, how great your prototype is or how many big-box stores want to purchase your product, there will usually be additional developmental steps. This is design for manufacturing (DFM).
DFM
Whether you know it or not, not every prototype can be made efficiently in production. There will most likely be quality problems, assembly problems, lead time issues, and costing problems.
Design for manufacturing (DFM) is one of the most important manufacturing steps to preparing yourself for commercialization. The point of DFM is to eliminate waste and ensure a smooth transition from development to production and scale-up.
During this process, there will most likely be re-designs and changes that are made to the product. You will want to figure out a change request process, so your contract manufacturer can request changes that go through an approval process.
Prototyping
Prototypes at this stage are made to confirm the validity of a design. Meaning that prototypes will test whether or not the design works.
Prototypes also serve other purposes as well that will transition you into production. The first one is to confirm your manufacturing costs. This will be especially helpful to calculate the assembly costs. The second one is for the final assembly. Prototypes will give the engineers experience of assembling the parts. They can use this experience to create work instructions (WIs) or standard operation procedures (SOPs). And thirdly is for quality control. Before production, you must have a quality standard and have prototypes that will objectify the standards.
Lastly, before you made any promises to your clients, make sure you engage with your contract manufacturer. You should always confirm from their side the final costs, the development timeline, and lead times to bring your product to life.
How Can OpenBOM Help?
OpenBOM believes engineering, supply chain, and manufacturing teams should be able to seamlessly manage their parts, vendors, bill of materials, purchase orders, and change orders. All BOM, engineering, and manufacturing information are stored in the cloud which you can share with your team, contractors, suppliers, or anyone else that has access to your account. OpenBOM keeps everyone on the same BOM while providing you with the tools to streamline your development to production & scale up operations.
Register for FREE to create your OpenBOM account and reach out to us via support @ openbom dot com if you have any questions.
Best,
Jared Haw
Join our newsletter to receive a weekly portion of news, articles, and tips about OpenBOM and our community.