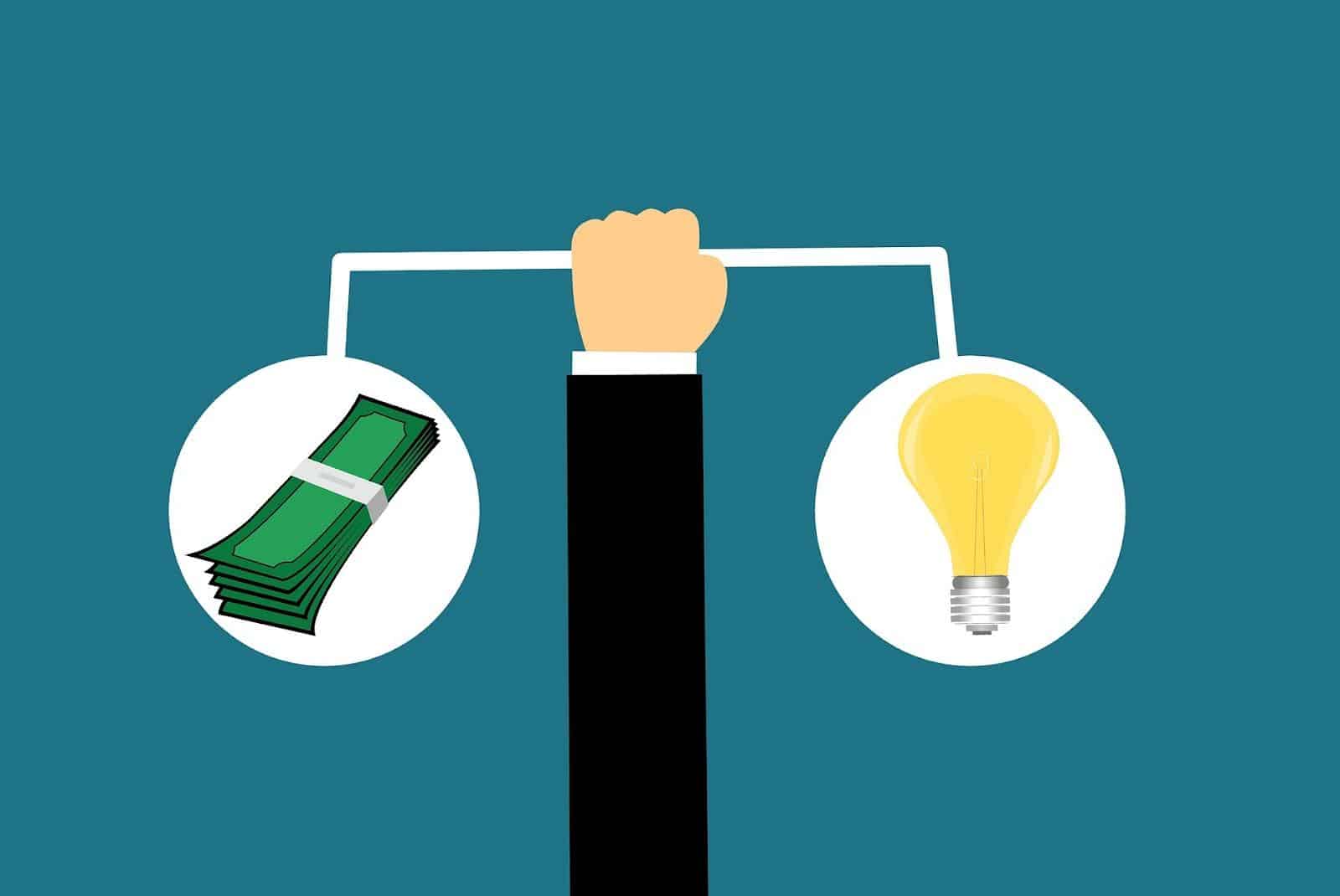
Throughout the life of a product, you will look at making improvements to your product. You might have noticed that your product is losing its competitive advantage. Or you might see your profits dwindling. Regardless of the reason, value engineering will be able to help you.
I usually don’t quote Investopedia for manufacturing topics, but I will here. Investopedia states that “Value engineering promotes the substitution of materials and methods with less expensive alternatives, without sacrificing functionality. It is focused solely on the functions of various components and materials, rather than their physical attributes. Value engineering is also called value analysis.”
Value engineering looks at improving two parts of your product, cost & functionality. By improving the cost, function, or both, you ultimately improve the value of the product.
To understand how to improve your product, you need to first understand where your customers see the true value in your product. Once you know this value, you can move forward to the proposal, design, and implementation stages
There are 5 steps in the value engineering process.
Collect your Product Information
Before you make any decisions about going forward you need to understand your costs. Try to break your costs down into categories. The more granular you go, the clearer picture you will have of your costs.
Here is how you can break your costs up:
- Bare PCBs
- PCB Components
- PCB Build
- Plastic Parts
- Metal Parts
- Off the Shelf Parts
- Scrap Costs
- Packaging Material
- Sub-Assembly
- Final Assembly
- Logistics
- Warehouse
- Shipment (warehouse to end-user)
Each item here should have a dollar value associated with it. You can quickly figure out the percent each of these items contributes to your cost of goods sold (COGS).
Once you see the costs associated with each item and the value they bring, you can identify the cost drivers. If you notice that metal parts and PCB components are your cost drivers then value engineering should focus on your metal and PCB parts.
Something else you need to collect is customer feedback to see where your customers see the value in your product.
Brainstorm
A team has been assembled at this stage and the goal here is to develop ideas on how to improve the value of the items you identified as being cost drivers in the previous step.
It might have also been a while since you looked at this product. So, there might have been some ways of doing things years ago that have now changed.
Again, the goal is to improve the value of the product and you do this by decreasing the price or improving functions. During the brainstorming step, you can look at the following:
- Analyze the materials that are being used and think of whether you can use alternative materials.
- What features are no longer relevant and can be removed?
- Are there features that should be added to keep up with current trends?
- Can you change your overall supply chain strategy to keep up with supply chain trends?
Evaluate
Like everything else, after you think about it and brainstorm ideas, you need to select the ideas that will improve the value of your product. Go through all of the ideas and develop a quantitative scoring method to see which idea you should proceed with.
Implement
This is where we dive in and execute the solutions we identified during the brainstorming step. On the engineering side, there will be a lot of the same tools used during design for manufacturing (DFM).
On the other side, you will need to assign a person to drive through the changes that were requested and agreed upon during the brainstorming and evaluation steps.
Review
The last step is to review the result. You want to see how you and the team performed. The best way is to look at ROI to see if there have been any positive changes.
What Can You Do Today?
During the life of a product, there will be multiple revisions and change requests that must be managed. It is easy to lose historical data or fail to share changes with the correct team members. A centralized platform that connects your team, contractors, and suppliers is your solution.
OpenBOM is a cloud-based platform to manage your engineering and manufacturing data. Companies from startups to Fortune 500’s use OpenBOM to create a centralized database to bring in, store and manage their manufacturing data. With this infrastructure, users also use OpenBOM to streamline both their change management and PO processes.
If you need to improve the way you manage your data and processes, contact us today for a free consultation.
Regards,
Jared Haw
Join our newsletter to receive a weekly portion of news, articles, and tips about OpenBOM and our community.